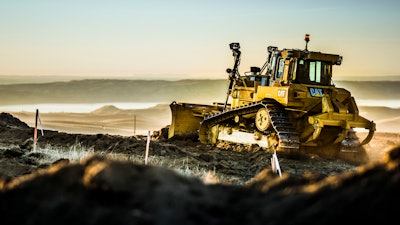
Loenbro is an industrial construction and energy services company based in Montana. It has several divisions that share equipment, and the divisions rent equipment from each other when possible instead of using a rental company to fulfill resource needs. While this is efficient and saves the company money on rental fees, Loenbro found it wasn’t getting an accurate idea of how many hours the equipment was being used.
Loenbro decided to add HCSS Telematics to its HCSS suite of products – which includes HeavyJob and Equipment360 – to help track equipment utilization, manage preventive maintenance and accurately charge costs to each job. HCSS Telematics is now active on 95% of its equipment and on-road vehicles at all times; the other 5% is equipment that has been idle for more than two weeks and is no longer part of the equipment audit.
The telematics software and GPS hardware are now helping the company manage equipment across multiple states.
Loenbro has HCSS Telematics active on nearly all of its equipment. The telematics software and GPS hardware help the company manage equipment across multiple states.HCSS
Because Loenbro’s jobs are spread out across the country, tracking and providing on-time maintenance on equipment was also a challenge for its shop. “During the boom out in the Bakken (Formation), we would send a piece of equipment out to a job and the mechanic never saw it for a year,” Micheletti comments. “By that time, it was far beyond its needed service.”
HCSS Telematics has enabled the company to set up a preventive maintenance program. “Now, the GPS data feeds into Equipment360, and any of the shop managers are aware of the machine’s upcoming service and can dispatch a mechanic accordingly,” says Micheletti.
Performing service on a scheduled basis has helped cut down on overall maintenance costs for the fleet.
Accurate Job Costing
Assigning job costs is another headache HCSS Telematics has helped to address. Prior to the program’s implementation, project managers received a lump sum cost for equipment that they would have to split up for each job on their own.
GPS data from HCSS Telematics feeds into Equipment360, making shop managers aware of a machine’s upcoming service needs so a mechanic can be dispatched.HCSS
Project managers input employee and resource hours into HeavyJob timecards, pulling the hours in from HCSS Telematics. Those hours then go to Loenbro’s accounting system, where the accounting department pays out employees but also charges equipment to the correct job.
“It gives our field engineers and project managers instantaneous costs to the job because we have calculated hourly rates of what the equipment costs, and they’re able to get real-time job costing data to monitor how much it’s costing them,” says Micheletti.
To resolve any discrepancies, Micheletti runs a report each week that compares what project managers entered in HeavyJob with what the GPS units have reported. “I may credit them back if they overstated hours, or I may charge them more,” he says. “It’s more automated.”
Loenbro also uses the HCSS Telematics geofence feature to set up markers around jobsites to know when equipment is entering and leaving a site. The geofences tie into Micheletti’s weekly report and help him true up equipment time. For example, if a field engineer forgets to put a pickup truck on his or her timecard, and Micheletti’s report shows that it ran for 10 hours, a geofence around the jobsites gives him the truck’s location to assign those hours.
HCSS Telematics also lets you to create a geofence around an area and identify the past location of vehicles or equipment. This proved valuable to Loenbro in verifying a recent fuel charge.
“A gas station in Wyoming claimed that one of our trucks fueled up and didn’t pay for it,” says Micheletti. “I was able to put a geofence on the gas station and go back a month and a half and verify if we had a truck there or not. He was there. His card wasn’t working outside, so he went inside and they turned on the pump for him. He thought that his card scanned, so he took off.” Without this feature, it would have been much more difficult to verify the charge was in fact accurate.
The Value of Data
As Loenbro has continued to grow, the push to know where equipment is and where it is moving has also expanded. This has led to increased usage of HCSS Telematics to get the data the company needs.
That data can then be used to better inform decisions about the company’s equipment. “I can see that we’re not using that many backhoes, so we don’t need those as much as we’re using the heck out of our dozers," Micheletti cites as an example.
“The main benefit is the valuable data, whether it is job costing and dispatching for the field or with equipment utilization and recommendations to managers. Machine cost is associated with utilization vs. spending a lot on equipment we’re not using,” Micheletti points out. “We really started understanding the value of the data.”
Information provided by HCSS and edited by Becky Schultz.