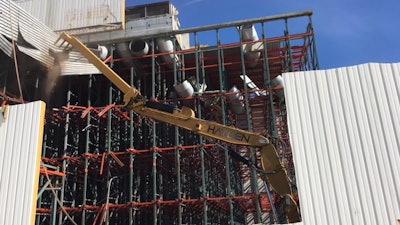
Information from this article was first published in Demolition Magazine and is being reused with permission from the National Demolition Association.
By Katie Condon
After its functionality became obsolete, the abandoned freezer near the center of Butterball’s 400,000-square-foot Mount Olive, NC, facility became an enormous sap of energy and space. To make matters worse, new construction boxed in all four sides of the 95-foot-tall gravity freezer which hindered any removal activities. The facility kept the entire section cooled below freezing while Butterball looked tirelessly for the right solution
ARCO National Construction and Hayden Wrecking Corporation, with oversight management from Lloyd Copeland, collaborated on the project to present a tailor-made demolition approach that would satisfy the unique needs for removing the 26,000-square-foot food processing freezer. The Hayden, Butterball and ARCO teams met extensively and visited the site to get a better understanding of the specific requirements of the active facility for demolition and future construction. The creative work plan exceeded customer expectations, greatly benefiting from top-level support including the corporate safety officer and professionals from Hayden’s environmental, operations and saw-cutting divisions.
Using wall saws and a Brokk 180 to breach exterior walls, crews created a tunnel through a refrigeration room.National Demolition Association
Cold and compact conditions
To accomplish the access and pre-removal that allows for structural installations, Hayden’s high demolition and saw-cutting crews had to work in extremely difficult conditions. Because the area could not warm up until partition walls were installed, high demolition torch crews had to work in -40-degree temperatures in the flash freezer section. Using wall saws and a Brokk 180 to breach exterior walls, crews created a tunnel through a refrigeration room, mere inches between the operations and active ammonia systems. Crews deconstructed the roof deck — to allow for recycling and ammonia system removal — while simultaneously completing the steel walking torch demo to allow for access of lifts and the assembly of a high reach excavator. In addition to the cold temperatures from the freezer, the crew had to endure challenging weather conditions, including high winds and rain, while they torched and stabilized the upper structure.
Active and occupied on all four sides, the facility required an extremely selective demolition of high structure using a very specialized Hybrid high reach machine and hand demo. All demolition had to be completed with a 10-foot- to 11-foot-wide opening. Demolishing in extremely tight quarters meant that bulkier machines, like a high reach excavator, had to be dissembled, moved out and moved back in several times to properly remove all of the material. The margin for error was so high that Nick Hayden, owner of Hayden Wrecking, personally operated the excavator with a shear to demolish sections of the structure. The implementation of the project had a high degree of difficulty, considering its tall but narrow composition and proximity to major utilities.
Innovation in green demolition
Despite the unique challenges of the Butterball freezer demolition project, the crews used a variety of methods to remove the structure in a safe and environmentally conscious manner. As an environmentally conservative company, Hayden Wrecking built environmental controls into every aspect of the job and took a creative approach to recycling or re-purposing every possible piece of material. For instance, concrete from insulation was detached using a technique developed specifically for the project that allowed under-floor insulation to be reused in construction. The process collectively saved 175 truckloads of landfill material, over $100,000 in costs for replacement insulation and over 1,000 hours of transportation time.
Crews used a variety of methods to remove the structure in a safe and environmentally conscious manner.National Demolition Association
A holistic outcome
The team successfully conquered these arduous challenges in less than four months. While the initial stages took a lot of time to complete, the project moved much quicker once the 95-foot-tall high bay was removed and loaded out. Notes Rick Reams, Hayden Wrecking’s corporate safety director, “This demanding schedule was met by close coordination with ARCO and Butterball to fast-track disconnects and isolations from the operating plant, as well as engineering and installation of support structure.”
Completing this project had a major impact economically and environmentally. The successful removal of the Butterball processing freezer means the plant will continue to be viable for years to come, saving hundreds of thousands of dollars in energy costs and literally hundreds of jobs in the surrounding facility. At the completion of the project, a whopping 98% of the building contents were reused or recycled, and over 90% of the material generated from demolition by weight was recycled.
Overall the project addressed all of the customer’s goals and was considered a huge victory. The key stakeholders were pleased with the commitment to safety, efficiency and waste-reduction at every phase of the project.