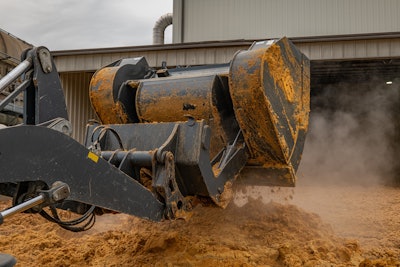
POET is the world’s largest producer of biofuels, with its Leipsic, Ohio bioprocessing location, which produces 90 million gallons annually. Most of the byproducts of the corn used to make its purified alcohol biofuel becomes feed used in the livestock industry. The Leipsic facility produces both wet and dry feed products with moisture percentages from 10% to 67%. When customers arrive, they expect prompt loading of the materials. Breakdowns and repair time are a nuisance for the customers, adding costs and creating delays. When Materials Manager Dan Karhoff noticed increased downtime and rising repair costs to keep their loader bucket operational, he sought alternatives. He found a solution, with Werk-Brau just a few miles east.
“The bucket we were using at the time was a 3½-yd. bucket built from a lighter gauge metal with fewer reinforcements in the high stress areas in the bucket,” said Karhoff. “After a few years of wear and tear and metal fatigue, we were forced to make annual repairs to the bucket. We rely on this piece of equipment daily to load trucks with wet feed product and move dry feed product around on our flat storage areas.”
As a 90-million-gallon per year biofuel plant, POET grinds roughly 70,000 bushels of corn a day. The dry and wet feed products created in the production process are sold and loaded into customer trucks daily. The physical attributes of the product vary greatly; the dry feed has about 10% moisture and the wet product has about 67% moisture. Switching between the two can wear down the bucket much faster, especially when switching often as they could load up to four or five wet feed trucks and six to eight dry feed trucks a day. Shutting down the loading operation for repairs is a headache for the customers and for the POET team. Because the old bucket could not be easily removed from the loader, to make repairs on the bucket, the entire loader had to be driven three to four miles to the repair shop, taking the machine out of service for a whole day each time. With customers expecting prompt loading, Karhoff realized he needed to invest in a quality piece of equipment that will hold up to their loading standards and keep pace with their production. That’s when he turned to Werk-Brau.
Karhoff upgraded from a Werk-Brau standard 3 ½-yd. bucket to the John Deere 544G loader. Manufactured with high-strength T-1 steel in all critical points and utilizing abrasion-resistant wear straps to reinforce the bucket bottom, the Werk-Brau bucket could withstand much more wear and tear than their previous bucket. Eventually, Karhoff decided to upgrade to a 544K loader with about 5,000 hours on it, since the 544G had about 15,000 hours and required more ongoing maintenance due to an issue with the motor. Since the Werk-Brau bucket worked so well on the 544G, when it came time to upgrade loaders, Karhoff decided to work with Werk-Brau again for a bucket for their new loader.
“The Werk-Brau bucket that was on the 544G still is in great shape with no issues. This is why I decided to stay with Werk-Brau for a new replacement bucket over our upgraded 544K loader,” Karhoff said. “I reached out to Neil Recker, Werk-Brau regional manager, for his experience and knowledge on the loader buckets. Neil and I worked together on redesigning a bucket that would meet our needs of loading feed product here at POET for customers’ daily orders.”
Over the course of many meetings, emails and phone calls between Karhoff, Recker, and the design engineering team, they were able to design a bucket that meets POET’s specific needs for loading feed products safely, and efficiently. Utilizing the latest CAD and finite element analysis software, Werk-Brau was able to design a bucket engineered for success and proven to withstand the stresses it would encounter. This software allowed them to determine what areas of the bucket would encounter the most wear and design accordingly.
The newly designed roll-out bucket has a deeper bottom that allows for more product to be picked up and held in the tilt-back position. This bucket has a depth of 56 inches, which is much deeper than the previous 34-in. bucket depth. This fixes the problem of product running out of the front of the bucket while it’s being tipped back, since the cutting edge will be almost the same height as the back of the bucket. There is also an arch up the center of the bucket to the cutting edge which prevents product from spilling over the sides during movement. The newly designed bucket is 4 yds. in volume, rather than 3 ½-yds. of the previous bucket. Because it is a high tip/roll out bucket design it adds 24-in. to the dump height which is important when loading trucks and maximizing pile height of stockpiled material. The recessed carriage improves the center of gravity which reduces stress on the loader and the bucket. All of these design changes enhanced Poet’s operations, allowing more product to be moved with each cycle of the loader.
“When you roll that thing back, you’ve got a full bucketful of product,” Karhoff said.
Once design for the new bucket was done, Recker invited Karhoff to the plant to inspect the bucket before it got painted to see if any other changes were desired. “When I went over there, I think there were just a couple minor things. They got that fixed, sent it off to paint, and we’ve been pleased with it ever since,” Karhoff said. Once the bucket was completed and put into operation at POET, Karhoff said he saw immediate results.
“After weeks of using this unit with the new design bucket, I was impressed with how it operated and the amount of product we were able to move in a safe environment,” Karhoff said.
After he noticed a minor design issue with some of the hoses rubbing, he mentioned the problem to Werk-Brau and they fixed it quickly, he said.
“They ended up changing the design a little bit on how they routed the hoses and put new hoses on. They stood behind their product, which means a lot to me. After six-plus months of use, I am pleased with the bucket and the service we received from Werk-Brau," he said.
Karhoff bought the Werk-Brau buckets through Murphy Tractor in Lima yet was still able to receive personalized adjustments and redesigns of the bucket to best suit his needs and receive top-quality service.
“The customers who purchase the wet and dry feed product are certainly pleased with the speed and efficiency of the loading process, and the fact that the equipment is ready when they are, with no loading delays due to bucket maintenance," he said.