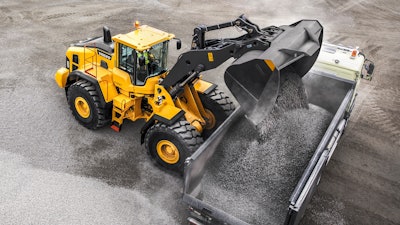
Even the most skilled operator can shorten a wheel loader's life and reduce its productivity by misusing certain functions or by operating the machine in a way that accelerates component wear. The risks increase dramatically when a new user gets behind the controls.
Operator training is essential, and even more so when a new machine comes into the fleet. An operator jumping on a new machine for the first time may not even realize they're using it incorrectly. Without education about its idiosyncrasies, features and technologies, they are likely to run the loader the same way as any other machine. But with technology changing so fast, uninformed operation can cause a lot of issues that could cause damage or wear.
The operator's manual is yet another invaluable resource. Along with basic operator training, studying the manual is one of the best ways an operator can get up to speed quickly and become more productive - both of which can have significant payback to your company in getting more work done.
Here are some other common problem areas with wheel loaders and tips on how to address them.
1. Take it easy on buckets
The most common wear areas on loaders are the front pins, bucket, bucket wear plates and teeth; this wear is accelerated by lack of general maintenance. For example, lack of greasing will speed wear of the front pin. So, it's important to stick to greasing and other daily service guidelines found in the operator's manual.
Monitor the buckets and turn or replace wear plates on the front before it starts tearing up the bucket itself. It can get very costly if you let the wear plates get gnawed down to the point that you start wearing on the bucket prematurely.
Matching the bucket to the application and material will reduce the amount of force required when driving into the pile. This in turn can reduce wear on the front pins, bucket, bucket wear plates and teeth.Doosan Infracore
Avoid running the engine rpms wide open and hitting the pile too hard, since this can stress the bucket and cause bushing and pin wear on the front of the machine. Plus, it burns more fuel than needed in the process.
2. Cool it on the brakes
All loader brakes (except hydrostatic machines) work by friction, which generates heat. Brakes that are over-applied can cause overheating and premature wear, which can make brakes fail before their time. Common causes include:
- untrained operators going too fast and then making short, quick stops
- unintentional application by "riding" the brake pedals
- hurried operators (under pressure to be more productive) going heavy on the throttle and then heavy on the brakes to stop fast or in a shorter distance
To extend brake life, train operators to slow down earlier and let the weight of the machine and load bring the loader to a near stop before applying the brakes.
3. Don't take shifting shortcuts
Transmission and transmission clutch wear can be a concern, depending on how the machine is being operated. Improper shifting can cause added wear and tear on the transmission and clutch.
High-speed shifts are the most common culprit. In other words, the operator uses the transmission and torque converter to change direction: The operator reverses the loader, "shoves" it into forward gear and hits the accelerator, or vice versa. If they are loading trucks all day and never touch the brakes, all that added force goes into the transmission and torque converter, overheating those components.
While this practice can lead to faster cycle times, it can also cause premature failure of very expensive components. Thankfully, manufacturers are taking the choice of whether or not to brake out of the operator's hands by automating shifting, among other functions, to reduce excess wear and tear.
Manufacturers are designing features into today’s wheel loaders to automate certain functions, enabling efficient high-production operations without sacrificing component life.Hitachi
4. Take time for warm-ups and shutdowns
Loader operators may be tempted to skip the warm-up during startup, but this can be hard on the engine and hydraulics. Cold oil doesn't lubricate as well, so getting up to operating temperature before operation will increase component life.
When starting the loader, allow it to warm up per manufacturer guidelines. Other systems such as hydraulics and axles will warm up as the machine is being worked, so the operator should expect that the machine won't have full performance until they come up to temp.
In addition to warm-ups, make sure all the fluid levels are correct during daily maintenance.
Shutdowns are just as important at the end of the day. Turbochargers on large diesel engines can reach speeds averaging 40,000 to 50,000 rpm. If you don't let the machine idle and cool down for at least two to three minutes, the turbo will still be spinning as much as 30 minutes later with no oil going to the bearings. This generates both heat and a lot of internal wear. Letting the machine cool down before you turn it off means the turbo won't spin as long after shutdown.
Manufacturers are working to reduce such risks by adding timed shutdowns on their machines. If offered as an option, consider it a bargain compared to the high cost of replacing a turbocharger.
5. How to stop spinning your wheels
Inexperienced operators are prone to spinning the tires, which is one of the worst things for a wheel loader. The machine is unable to use the differential locks the way they should to lock the front axle up, so all that power goes to both front tires instead of just one, which would reduce the spinning. Premature tire wear is the result.
Understanding how all of the functions operate on a particular loader will improve productivity and minimize the risk of misapplication, which can shorten component life.John Deere
In some cases, tire spin is the fault of the tire, not the operator. One reason is having the wrong type of tire on the wheel loader for the application. Make sure that the tread pattern meets the application requirements. For example, a high tractive tire with a more open tread pattern will wear faster on paved surfaces. So, if the loader will operate primarily on concrete or asphalt, an L4 or L5 will cut down on wear. If the loader will be working mainly in dirt, a more aggressive, tractive tread pattern is the better choice.
Information provided by Volvo Construction Equipment, John Deere, Hitachi Construction Machinery Loaders America, Doosan Infracore North America. Edited by Becky Schultz.