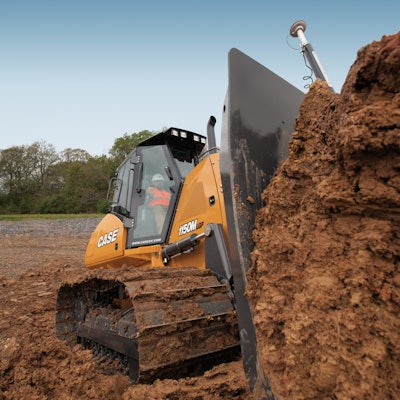
Novice operators can impact the cost to operate your dozers and related undercarriage expense, but modern electronics help protect your investment while dramatically increasing productivity.
“The industry will always need skilled operators, but smart technology like machine control and automation can certainly speed up the learning process for inexperienced operators,” says John Bauer, brand marketing manager, Case Construction Equipment. “These technologies also make seasoned operators more efficient, allowing them to focus less on precision grading and more on safe operation on the jobsite.”
There are many ways to measure productivity. “But it really comes down to completing more work with less effort, eliminating rework, reducing maintenance and fuel costs and more intelligently utilizing equipment to get more out of your fleet,” says Bauer. If you can reduce the number of passes it takes to final grade a site, you reduce engine hours and fuel costs, as well as lessen wear and tear on ground-engaging tools and other machine components. “My advice to new dozer operators is to make sure that you’re utilizing all of the technology features available. They are there to help make you more efficient.”
There’s an amazing amount of technology on these machines and learning how to apply it to your work will not only increase your productivity, but also your skills and value to your company.
Basic principles of slot dozing, blade steering, ripping and other tasks should be understood to maximize your productivity. “Learn to use the autoshift, bi-directional and traction control systems to your advantage,” Meeker advises. “There’s an amazing amount of technology on these machines and learning how to apply it to your work will not only increase your productivity, but also your skills and value to your company.”
Even simple technology solutions can yield impressive results. “I’m amazed at what customers are able to do with our Slope Assist system, a basic 2D system that provides tremendous value at very little cost,” says Meeker. “A customer can grade house pads, cut road ditches, spread material and cut in drainage on a site with no setup of a laser or GPS base station.
“On the other end, the Cat GRADE with 3D systems provide extremely accurate grades while reducing manpower and improving safety,” he continues. “I enjoy pulling up to a stake-less jobsite and listening to how the customers have changed their work and become more productive. Customers learn to take the tools and apply them to exact the most value possible.”
[VIDEO] Contractor's View: How Cat Slope Assist Cuts Two-Thirds of Road Staking
[VIDEO] Contractor Shares How Cat GRADE with 3D Makes Grading Fast and Easy
The power management system on John Deere dozers is automatic and makes the machine easy to control, regardless of operator skill level. When the machine encounters a heavy blade load, the power management system simply adjusts hydrostatic load to maintain ideal engine rpm.
John Deere also recently launched dozers with integrated grade control. “SmartGrade dozers are another way to get new operators up to speed sooner,” says Horstman. “SmartGrade dozers not only control the blade automatically, but are also equipped with an anti-slip feature that helps operators maximize productivity and minimize undercarriage wear caused by track slippage.”
John Deere's 700K SmartGrade Dozer Takes a More Intelligent Approach to Grading
Drivetrains Increase Efficiency
While manufacturers still debate the pros and cons of hydrostatic (hystat) vs. mechanical drivelines, development continues on more sophisticated drive systems that simplify operation.
On its recently unveiled D6T dozer, Caterpillar wanted to combine the benefits of a mechanical powershift with those of a hydrostatic transmission. “Hystat dozers are definitely easy to operate,” says Meeker. “The trick with the D6T was to create a transmission and control system that provides the durability of a powershift with the ease of operation of a hystat.”
The solution came in a hybrid approach. “The latest D6T has a four-speed powershift transmission coupled with a lock-up clutch torque divider that provides exceptionally smooth shifting and amazing efficiencies,” says Meeker. The D6T offers 2.5% more productivity and reduces fuel burn by 15% to 30% vs. the previous generation model, all while giving the operator 30 speeds of control and smooth shifts.
Hydrostatic technology continues to evolve. “The hydrostatic drive systems have improved throughout the years,” notes Meeker. “On the latest D6K dozer and 963K track loader, we have redesigned the hystat system to further improve performance, efficiency and reliability. These systems provide lower fuel consumption for customers and longer life.”
But Caterpillar doesn’t believe there is a one size fits all solution. “We design and implement drive systems that are tailored to the machine and application,” says Meeker. “Smaller dozers typically work on jobs where the speed control, maneuverability and ease of use of a hystat is valued. Larger dozers need the durability and long-term efficiency that a powershift can provide.”
There are pros and cons to both. “Hystat systems are great for maneuverability, variable speed and easy operation,” notes Meeker. “In larger dozers, however, we feel the powershift transmission is still the best choice for long-term durability and efficiency. Over the last couple of years, we have introduced Enhanced and Advanced AutoShift systems that combine the benefits of the durability of a powershift and the versatility of a hystat.”
General maintenance for both types of systems is similar, with filter and oil changes having a similar hourly cost. Long-term wear is the bigger consideration. “At the beginning of life, both powershift and hystat systems are very efficient in terms of putting power to the ground,” says Meeker. “Later in life is where the differences start to appear. Powershift transmissions retain their efficiency longer in general, and require less expensive component rebuilds when repair time does occur. This is often reflected in resale values of hystat vs. powershift machines.”
The power management system on John Deere dozers is automatic and makes the machine easy to control, regardless of operator skill level. When the machine encounters a heavy blade load, the power management system simply adjusts hydrostatic load to maintain ideal engine rpm.
Case Construction Equipment utilizes hydrostatic drive systems on all of its dozers from the 650L up to the 2050M. “There are fewer moving parts with the hydrostatic transmission than there would be with a powershift. You’re basically dealing with hoses, pumps and motors,” says Bauer. “There are no gears, so the operator has much more control over the speed of the machine.”
Plus, operators don’t have to be concerned with proper gear selection. “One of the benefits of hydrostatic transmissions from an ease-of-operation standpoint is that you have a variable control on the speed. A simple up or down with a button on your left-hand control will change the speed smoothly,” Bauer points out.
The hydrostatic transmission also ensures constant power transfer under load and allows for on-the-spot counter rotation with full power turns. Operators can customize machine responsiveness by adjusting steering and shuttle sensitivity settings between Smooth, Moderate or Aggressive.
Liebherr PR 716 Litronic Crawler Dozer
The hydrostatic system also enables the addition of features to balance traction and power. “These advanced features improve the performance of the dozer across the board. The hydrostatic travel drive system provides maximum tractive effort for the dozer and reduces track slip,” says Rogers. “This also allows the operator to concentrate on the work instead of trying to monitor speed and traction. It allows the operator to concentrate on the work while reducing the wear on the undercarriage.”
Traction Control Saves Wear and Increases Productivity
Traction control is essential to maximize productivity. “From our studies in dozer productivity, maximum productivity is gained with ‘Big Load Slow,’ maximum blade load at full speed in first gear,” says Meeker. “Traction control helps the operator determine what that maximum blade load is, and helps to reach that most productive speed in fewer passes. Conditions and materials change throughout the day and features such as Auto Traction Control help the operator react to those changes quicker and continue to be productive.”
In the Caterpillar K Series dozers, the Auto Traction Control system combines several inputs to determine if the track is slipping and apply appropriate changes to the hystat system to reduce track spin. “In dozers equipped with Cat GRADE with 3D, the AutoCarry feature actively senses machine and track movement, comparing the two to determine track slip,” says Meeker. “Just as track slip is beginning to occur, the system actively manages the blade to reduce track slip, all while maximizing the load on the blade for the most productivity.”
The goal is to push the maximum load possible. “With a load management system, the machine will always attempt to optimize the balance between torque and speed to maximize productivity,” says Case’s Bauer. “As the dozer builds a load in front of the blade, the load management system reduces the track speed to provide more torque to the ground. This functions automatically without any operator input. It takes a lot of the downshifting and other adjustments out of the picture so the operator can focus on running the machine safely and efficiently.
“Load management systems also help guard against engine stall when the machine is pushing massive loads,” he continues. “This helps to reduce wear on the undercarriage and other components of the machine.”
By automating the balance of available pushing power and speed, the dozer becomes easier to operate. “The power management system on John Deere dozers is automatic and makes the machine easy to control, regardless of operator skill level,” says Horstman. “When the machine encounters a heavy blade load, the system simply adjusts hydrostatic load to maintain ideal engine rpm, allowing the operator to concentrate on the work at hand, not shifting.
“The anti-track slip feature on SmartGrade dozers helps operators of all skill levels maximize productivity and minimize excessive track wear caused by slipping the track,” he adds.
Tailor Response to the Job
In the Liebherr dozers, the operators have the ability to adjust the responsiveness in the blade control as well as adjust speed control for the particular speed range settings. That certainly helps the operator cater to not only their needs for productive operation, but also the needs of the particular job they are on at the time.
Dozer controls have witnessed significant technological advancements. “New control customizations allow operators to better tailor machine performance to jobsite conditions — setting steering and shuttle sensitivity,” notes Bauer. “Case 1150M, 1650M and 2050M dozers feature a new electrohydraulic joystick that further simplifies operation by providing better feel and responsiveness. Fingertip blade shake allows for a quick blade cleaning, and a grade mode reduces blade speed by 40% for increased accuracy.”
John Deere K-Series dozers allow the operator to customize the machine feel through settings in the display monitor. “The operator can easily adjust ground speed limits, steering modulation, decelerator pedal, hydraulic speed and FNR aggressiveness,” says Horstman. “As an example, some operators like a quick direction change when shifting from forward to reverse. If you want the machine to ‘roll out’ a little when shifting from forward to reverse, you can have that, too.”
It’s about optimizing the machine to the operator. “The most efficient operators I’ve seen are the ones that treat the machine as an extension of their person,” Meeker observes. “Tuning the steering, forward and reverse speeds, blade control and any other factors truly helps that operator become more responsive to job conditions and to be more productive. It’s not only the initial setup, but being able to easily make changes as the materials and job change throughout the day that makes life easier, as well.
“The best operators are truly artists with the machine,” he adds, “and tuning controls is essential to equipping the operator and the machine to be great together.”