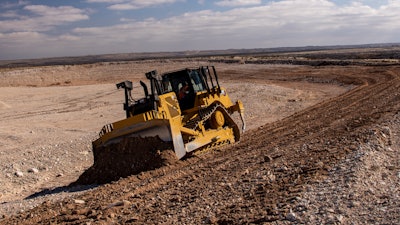
Operator training can pay quick dividends when it comes to machines running on a steel track undercarriage. Not only are operators running machines, more of them are being tasked with performing basic maintenance tasks and they should be conducting daily walk-around inspections as part of a preventive maintenance plan.
A steel undercarriage is expensive to replace. Maximizing its useful life has a major impact on operating costs. An experienced operator can ensure the undercarriage wears evenly, allowing the components to achieve maximum life.
Operating technique plays one of the most important roles in determining overall undercarriage life and cost of operation. Some techniques that generate premature wear include:
- Operating excessively in reverse, especially at high speeds
- Side loading a machine and working on too steep slopes
- Continuously turning in the same direction
- Counter rotating or pivot turns
Smooth, wide turns reduce stress
Modern hydrostatic machines allow operators to turn fast in a small radius. This creates stress on the undercarriage as the track group assembly is subjected to additional pulling forces coming from the final drive.
Any time the machine changes directions, wear to the undercarriage occurs. The more abruptly and aggressively the operator turns, the more forces are produced on components, contributing to wear. Sharp turns and pivoting the machine can also increase the potential for de-tracking. These factors can be minimized by training operators to make wide, less aggressive turns.
Turning constantly in the same direction can result in uneven wear. Undercarriage components on one side of the machine will wear at a different rate than those on the other side. For instance, turning left all the time accelerates wear on the right side and vice versa. Pay attention to the direction you are turning and change directions whenever possible.
Minimize speed and reverse operation
The design of the steel undercarriage has a direct impact on the effects of running in reverse. On a fixed bushing track, the bushing and sprockets will see increased wear rates while running in reverse. There is sliding wear between the bushing and sprocket at any speed, but as the speed increases, the amount of load and contact changes, which increases wear rates. Speed tends to move the bushing out of the root of the sprocket to a higher point on the sprocket tooth, which changes the contact pattern and results in higher wear. As such, high-speed reversing should be avoided.
The geometry of a steel undercarriage typically is optimized to run in the forward direction. Crawler tractors have the drive sprocket segments located at the back of the undercarriage. It is designed to pull the chain up and over so you can push material forward. The front idler doesn’t have as much tension on it. When you put the machine in reverse, the dynamics of the undercarriage change. It puts stress in the opposite direction, often leading to increased wear.
Reverse operation has traditionally been one of the fastest ways to wear out a track. It is the only time bushings rotate against the sprocket teeth under load. In some cases, reverse operation can accelerate the wear of the sprockets and bushings up to three times compared to forward travel.
Some of the newer track systems on crawler tractors are more resistant to wear in reverse. For instance, rotating bushing tracks are more tolerant since they take the sliding component out of the wear equation.
Even with rotating bushing designs, operators need to be cautious of excessive speed. Speed equates to friction and heat. Wear on any steel undercarriage is directly proportional to it. Non-productive high-speed travel should be limited.
Properly Position Tracks
When operating an excavator, always work over the idlers so that high vertical loads can be transmitted to the frame in a safe way through the links and idlers.John Deere
When operating an excavator, it is important to keep in mind the position of the idlers and sprockets in relation to the direction of work. Always work over the idlers so that high vertical loads can be transmitted to the frame in a safe way through the links and idlers. Working over the sprockets can cause premature bushing cracks or breakage due to the loads being transferred directly to the bushing/sprocket system.
In addition, avoid travel with the drive sprockets in the front. When traveling a long distance, always travel in forward with the idler in front of the machine. There is significantly more external and internal bushing wear when you travel in reverse.
Also consider the location of the drive motors when traversing slopes. When moving an excavator up or down a hill, make sure the drive motor is facing the back of the machine.
Keep the Tracks Clean
Mud left to dry in the undercarriage can harden and create excessive wear. If operators neglect to clean the undercarriage in colder climates, the mud and dirt can freeze.
A packed track robs horsepower and creates additional heat and stress. The material fills in the space between the frame and the track. The links eventually start to drag through the material, increasing the wear rates.
Mud packing on the undercarriage components can also lead to over-tensioning. Packing prevents the proper engagement between the mating components such as sprocket teeth and track links. This can cause increased loads on undercarriage components and higher wear rates.
In addition, cleaning the undercarriage helps the operator spot potential problems, such as loose or missing components.Steel undercarriage is expensive to replace and is designed so components wear out evenly. An experienced operator can ensure even wear, allowing the components to achieve maximum life.
Follow Best Practices When Working on Slopes
Many applications require slope or hillside work, which can wear the undercarriage components more rapidly since the loads are not distributed evenly on the whole undercarriage. The operator has a major impact in these applications. Constant operation on a slope or hill in one direction can accelerate wear.
The downhill side of the machine is especially susceptible to increased wear. When the machine is on the side hill, the link side is constantly working against the roller flanges, which accelerates wear on both the links and roller flanges. This contrasts to working on flat ground where undercarriage wear occurs mainly on the rail surfaces of both the links and rollers.
Operating on side hills wears off the flanks of the links, which reduces overall link width and the available contact area with the rollers. This leads to increased contact stress when the machine goes back to operate on flat ground.
Links and rollers on the downhill side experience higher than normal loads and an increased wear rate. Roller flanges and track guides on both sides of the machine that face the downhill side work the hardest and will see higher wear rates.
Operators can balance this wear and extend overall life by balancing machine orientation as evenly as possible. The operator should work half of the time with one side of the machine facing downhill and the other half with the opposing side of the machine facing downhill, where possible. This will allow for more even wear.Skilled operators will avoid loading the blade to the point where the tracks slip. More than 5% slippage of track increases undercarriage costs and fuel costs without improving productivity.John Deere
Limit Track Slippage
The goal with a crawler tractor is to maximize productivity, which tempts the operator into loading the blade to optimize the material being moved. But skilled operators will avoid loading the blade to the point where the tracks slip. More than 5% track slippage increases undercarriage and fuel costs without improving productivity.
Track slippage and spinning can accelerate shoe and grouser wear. Other components that see additional stress include sprocket teeth and bushing contact surfaces, track links and roller rails/flanges and idler tread surfaces.
An expert operator considers the ground conditions and the type of shoes and grousers on the machine to help minimize track slippage. Those who spend many hours in the machine will understand what the undercarriage normally sounds like; they should report any unusual sounds to help catch any problems early. For instance, a roller that stops rotating due to a material-packed undercarriage can start to wear the track chain.
Over the life of any steel track machine, the undercarriage will represent a significant portion of the operating cost. Training operators on best operating techniques and on what to look for during daily maintenance and inspections can offer a large return on investment. ET