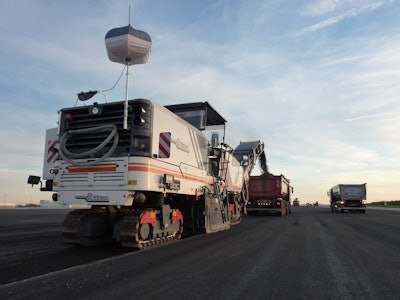
Cold milling is an integral part of the construction cycle of any road. Asphalt milling is used to remove an old and worn wearing course or the entire asphalt pavement. It can also be used to improve the surface friction or remove ruts on a wearing course that is otherwise in good condition.
The asphalt milling machine — also known as a cold planer, pavement planer, pavement recycler or roto-mill — is used to remove bituminous pavement or asphalt concrete from roadways. The result is a somewhat rough but even surface that can immediately be opened to traffic.
The milled surface is accomplished by bringing a rotating mandrel or "head" into contact with the pavement at an exact depth or slope. The mandrel has hundreds of hardened teeth on its surface, which bite and cut away at the roadway's surface.
The surface material that is removed is normally fed by conveyor into a dump truck or semi-trailer, but can be left in place or windrowed to be removed or recycled later. A water spray system provides cooling for the mandrel, as well as dust management.
There are several steps – or best practices - you can take to ensure your milling machine and operators produce a high-quality milled surface.
As Tom Chastain, applications specialist with Wirtgen America, says, “It’s the little things that affect production and efficiency. Control those and you’ll have a quality mill job.”
Preparation
Before beginning a milling project, the number one item to prepare is the milling machine itself.
“The milling machine should be at 100%,” says Chastain. “Preparation of the machine as far as machine maintenance, drum maintenance, and making sure you have the proper leveling controls operating properly.”
To ensure you’re using the right machine for the job, you need to understand the details of the application. “Understanding what and where we need to cut is crucial,” says Chastain. “Having support tools available such as water and trucking is important. Know how many and what is a typical turnaround. You need to have an understanding if there are any weight restrictions. This may dictate what size machine you can use.”
The crew is also an important piece of the preparation puzzle. “The crew is everything,” he says. “As manufacturers, we can produce high quality machines using amazing technology. If the crew is not in sync, this throws everything out of rhythm. A quality crew, is the most valuable thing on any job. A good crew, using their machine properly, is the best tool a contractor has.”
And of course, to make it all come together, communication is key. This starts from the top, and goes down, says Chastain.
“Giving the milling crew as much information regarding the job allows the crew to communicate, and decide the safest, and most productive way to get the job done,” he says. “When on the job, if everyone -- from the milling crew to the paving crew to the flaggers and truck drivers -- has a firm grasp of what you’re trying to achieve, this allows everyone to be synced and makes for a safer work environment. You can only control what happens behind the safety barrels. Be aware of your surroundings and make sure you’re looking out for everyone’s safety.”
Operation
When performing a milling job, good operational practices are key. The speed of the milling machine can make or break both the quantity and the quality of the mill.
“Start slow, stop slow,” says Chastain. “When starting, move forward at a slow pace so the rear tracks can walk into the cut. This allows the hydraulics for all legs to adjust accordingly.”
Starting too fast, he says will make a dip right off the gate. When stopping, slow down before coming to a complete stop.
“If we’re milling at 100 fpm, then stop quickly, the machine will stop,” he explains. “But some think that the machine is settling when they take off again. This is not the case. The drum is simply ‘catching up.’ The drum is turning at a certain RPM. The teeth are just hitting the same spot. Start slow, stop slow.”
If the machine is paced correctly, operators can achieve both a productive quantity and high quality mill.
“If you look at the average milling job per hour, you’re only cutting for 30 to 40 minutes,” says Chastain. “With truck exchange, water stops and checking teeth, these variables don’t allow us to cut for a solid hour. So if you’re used to milling for 30 minutes an hour at 110 fpm, and sitting the rest of the hour, you could slow down to 80-90 fpm and cut for 45 minutes out of the hour still get the same quantities while your quality goes up.”
Milling at a high speed isn’t worth the extra quantity you might think you will achieve.
“Milling at high speeds puts unneeded wear on the machine and will create a coarse pattern,” says Chastain. “This also makes for larger RAP material, which means producers may have to run the material through a crusher before it’s used.”
New machines have different drum speeds, which, of course, is different than machine speed. Running a machine in the highest drum speed at a lower machine speed will help achieve a fine texture quality, without the line spacing of a fine textured drum. This also makes for better sizing of RAP material.
Technology benefits
Technology allows users to work smarter not harder. Milling machines built today allow users a higher quality material output while achieving production goals. Technology allows users to monitor the machine and the job parameters and eliminate guesswork.
There are myriad new technologies on today’s milling machines, says Chastain.
“For example, using smart cylinders for grade control allows you to actually use the side plate now as an averaging ski,” he says. “In the past, you were referencing from one single wire rope sensor which could cause more deviations in our cutting depth.”
Other modern technologies include job calculations that monitor how many tons are loaded in the trucks, truck counting, and area covered. Vacuum cutting systems for a dust-free work environment and silica regulation compliance. The ability to trouble-shoot mills and obtain diagnostics from a single display.
Machine telematics are crucial for eliminating downtime. “By having machine monitoring, this allows the operator to see when they a problem, and what to check,” says Chastain. “In the past, it took longer and you had more downtime when troubleshooting.”
Another best practice that technology can help with is properly maintaining the milling machine. Proper maintenance helps with achieving production and quality goals while also providing a safe environment for the crew.
Always follow your manufacturer’s maintenance procedures. “With new technologies being used, these machines can be monitored offsite,” says Chastain. “This allows service personnel to be aware of when the machine is due for service and if there are any malfunctions.”
As always, safety is number one. “If you’re on a job and something doesn’t seem safe, stop,” cautions Chastain. “Have a conversation, and collectively, come up with the safest way to complete the task.”
For more information on milling machines, visit ForConstructionPros.com and Search 12239632 for "The Evolution of Milling Machines."