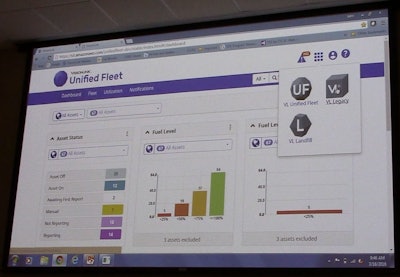
Throughout 2016, Caterpillar will release updates to the VisionLink user interface, making it faster and easier to use with today’s smartphones and tablets. Cat customers will continue to experience the value offered by more efficient management of their fleet:
- Tracking equipment location
- Monitoring equipment usage
- Monitoring and managing fuel consumption
- Identifying operators needing training
- Planning and scheduling maintenance
VisionLink is integrated with Cat Product Link hardware to create a powerful telematics system that provides a wealth of information based on data from machine sensors and control systems. Product Link hardware is standard on most Cat equipment and can be used to retrofit both Cat machines and machines from other manufacturers.
As John Thomas, director of marketing, Virtual Site Solutions, Caterpillar Inc., notes, most major heavy equipment OEMs utilize a proprietary telematics system, often available to customers during a free subscription period with an equipment purchase. In the past, customers with mixed fleets had to access each manufacturers’ individual system to monitor their equipment.
The new VisionLink will support data being exported to and from other business systems complying with the AEM/AEMP Telematics API Standard, which includes both OEMs and third-party telematics suppliers. “At the customer's request, the data collected by the OEM's machine and telematics device, that is identified by the AEM/AEMP telematics standard, can be shared with the customer or with anyone the customer designates to act on their behalf," Thomas explains. "This is to enable the customer to access and view data from their mixed fleets in a single software solution. This solution could be a custom-designed software solution, an ERP system, or a system specifically designed to meet the needs of construction customers with mixed fleets, such as VisionLink. When a customer requests to have their mixed fleet data accessed and viewed through our VisionLink software, that mixed fleet data is hosted by Virtual Site Solutions as a third party on the customer’s behalf, it is not stored in any OEM’s databases.”
This ability to import data enables customers to view their entire connected fleet using just VisionLink, which is a cost advantage when applied to manufacturers offering free telematics periods.
System Enhancements
The VisionLink redesign incorporates a number of refined features, including easy-to-read and navigate screens whether using a phone, tablet, notebook or desktop. Whereas the legacy VisionLink had separate desktop and mobile versions, the new version incorporates a responsive design to ensure users experience a more intuitive transition between mobile and desktop user interfaces.
"This means the application is the same whether you access it on a desktop, a laptop, a tablet or a phone. There’s no loss of functionality," says Thomas. "All that happens is the screen changes in size and configuration."
The new version also includes a suite of apps, enabling the customer to select a view and information based on the user’s role or the task needing to be performed. "The applications will be focused on a task or a job role, so that the customers are going to be exposed to just the information that they need to do their job instead of having to wade through every piece of information that’s available," says Thomas.
The apps can be readily accessed for quick reference and easy viewing. For example, equipment or fleet managers can access data related to asset hours, location and utilization without having to sort through extraneous information such as fault codes, maintenance schedules or productivity information that may not pertain to their responsibilities.
One of the first applications to be released is the VisionLink Unified Fleet app, developed for equipment managers and owner/operators. It features easy and intuitive views of information such as hours, miles, location, idle time, asset status and customer-defined asset states. This approach simplifies information on the screen, allowing users to focus on information needed to perform their daily tasks.
The VisionLink Landfill app, developed for landfill operators, features views to better manage solid waste operations to monitor fill and compaction when using Trimble CCS900 3D/GPS Compaction Control systems or Cat AccuGrade Compaction Control systems. The app calculates the volume of waste being placed and the compaction densities achieved.
Easing the Transition
The new system allows for an easy and seamless transition between the legacy VisionLink and new versions. Existing features have been moved into new apps, plus a single sign-on to all apps and the ability to easily move back and forth between apps and existing features are available in the VisionLink Legacy app. The new and the legacy format will co-exist for a time until all relevant features are completely migrated.
When the rollout is complete, the new system will offer a service layer called the VisionLink Services Platform, which enables partners and third parties to extend the VisionLink products to fit their unique needs. The services layer will enable developers to create unique solutions using VisionLink data to offer solutions that go above and beyond the standard offerings.