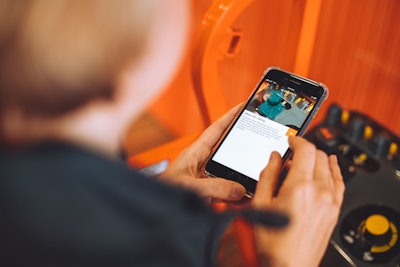
In today’s world, we’re inundated with information and notifications all the time. At work, the flood of questions, instructions, and data is just as constant. And everyone in the construction industry is feeling the impact as modern jobsites present a new set of challenges related to interpreting machine data, improving worker productivity, and increasing equipment utilization — but new technologies like augmented reality can help.
What is augmented reality? It's a digital solution that can streamline jobsite operations. It enables users to determine the right equipment for the job, can improve machine service, and enhance operator knowledge and productivity. With these capabilities, this technology can alleviate some of the most common challenges in the construction industry today.
Challenge #1 – Simplifying the Data
Data overload. It’s what happens when there’s so much data available that you don’t even know where to start to find the answers you need. With so much data at our fingertips, it’s become increasingly difficult to access the right information at the right time.
Here’s how augmented reality can help. Using an augmented reality app downloaded to your mobile device, you can get on-demand, digital access to information specific to a machine or your work area without ever leaving the jobsite.
For example:
- Operators can scan decals and read them in their native language.
- Project managers can use machine visualization to ensure the equipment they’re ordering will fit in their workspace and reach the required areas without looking up dimensions in a manual or online.
- Rental companies can use accessory visualization to be confident that they’re ordering the right accessories to fit the models they carry without referencing a parts manual to verify fit.
- Technicians can use their phone to walk through inspection protocols to ensure they efficiently document every step.
Challenge #2 – Recruiting the Next Generation
Service technicians in the construction industry have a valued and desirable skillset. However, studies indicate future generations have little desire to enter the field.
In fact, 64 percent of Millennials said they wouldn’t consider working in construction, even if you paid them $100,000 or more. As many construction workers are at or near retirement age, recruiting the next generation of workers seems like a daunting task.
Augmented reality can also help drive efficiencies when workforce numbers are limited. For example, having access to service information without needing to reference a manual or make a call streamlines a technician’s job.JLG
However, emerging technologies like augmented reality have the capability to attract younger workers (you know, those people who are more accustomed to using technology in their daily lives) to the construction industry. Using technology to assist newer workers with formerly cumbersome tasks can also be a benefit for technology-driven Millennials and Generation Z or even those turning to constructions as career change options.
Augmented reality can also help drive efficiencies when workforce numbers are limited. For example, having access to service information without needing to reference a manual or make a call streamlines a technician’s job. This enables them to fix issues more quickly and move on to the next task.
Challenge #3 – Raising Utilization Rates and ROI
The most important factor to the success of a rental company is equipment utilization. The more days a piece of equipment remains in the field working for a customer, the more money it brings in for the business.
Keeping machines in use means making sure operators have the tools they need to operate machines safely. Using augmented reality, operators can scan a machine’s control panel and double-check control functions, translated into their native language. Operators can also scan decals and see translations of the decals to make certain they are following safety protocols. Streamlining operator efficiency keeps machines in use on the jobsite, not idling while operators consult manuals.
Incorrect equipment specification and delivery can also impact a machine’s utilization. When equipment is too large or too small for the worksite space, or when it cannot reach the required heights for the work, the productivity of the end-user is affected and the utilization rate of the machine drops, which negatively impacts the rental company’s bottom line.
Thus, having a suite of augmented reality tools that can confirm the size and fit of both equipment and accessories before they’re delivered helps lower total cost of ownership.
The U.S. Chamber of Commerce says the construction industry is well-positioned to recover post-COVID-19. Knowing this, rental and construction companies should prepare themselves for future contracts. Augmented reality can help rental businesses drive efficiencies while addressing the need for more workers and more utilization.