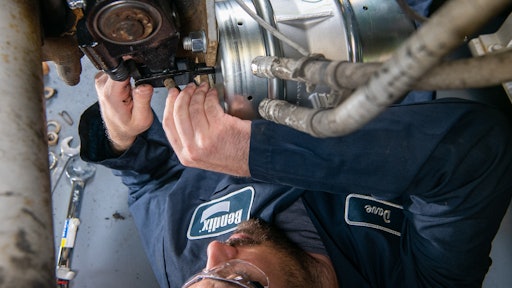
Air brakes have a long history of reliable performance in the medium- and heavy-duty truck markets, yet these systems cannot be ignored without costly consequences. A good inspection process and Preventative Maintenance (PM) plan can keep you trucks from being sidelined.
Improper air brake maintenance accounts for a large percentage of trucks being tagged out of service during DOT inspections. For instance, the Commercial Vehicle Safety Alliance (CVSA) performs Roadcheck, an annual inspection as part of an initiative to drive awareness to keep roadways safe. According to CVSA, one-fifth of the more than 50,000 commercial vehicle inspections during the 2020 International Roadcheck event resulted in a vehicle being taken out of service because of safety violations. Close to 40 percent of these vehicles were tagged out of service due to the brake system and/or brake adjustment.
“Many of the critical issues flagged during these inspections are maintenance-related, and many are issues that could have easily been prevented with regular, thorough maintenance procedures,” says Fred Andersky, Bendix Director – demos, sales and service training. Pre-trip inspections are a good starting point. First, look for visible brake system problems such as loose hoses or damaged brake components including air chambers or pushrods.
Recently, air disc brake systems have been gaining popularity due to both performance gains and the ease of maintenance. But disc brake systems shouldn’t be ignored. “Regardless of whether you have a drum or air disc brake system, regular maintenance is required to ensure safe operation and longer service life,” says Mark Holley , director of marketing and customer solutions, wheel end, Bendix. “Although service intervals may be longer with many air disc brake applications, they do require regular inspection and maintenance. With air disc brakes, some technicians inspect at the PM, but most of the time technicians fail to conduct a good visual and caliper movement inspection.”
Perform Routine Inspections
Since brakes are critical to uptime and safety, it is critical to inspect as often as possible. “Do a quick inspection when the vehicle is in the shop – even if it is not for a brake issue,” says Kevin Pfost, technical service,” Bendix. A quick visual check can prevent future problems. “Make sure all brake chambers have the rubber plug properly installed in the caging bolt hole to keep contaminants out of the chamber.”
Brake systems must operate in often hostile environments. For instance, exposure to winter chemicals can wreak havoc on brake systems. “Chemicals are not good – even without winter weather,” says Pfost. “Chemicals contribute to rust on parts like drums/rotors. Water with salt and chemicals can be ingested into seals and bushings.” You can combat this with the proper application of grease. “Greasing the cam brake can help force water and contaminants out. Slack adjusters should be regularly greased. Lubricate the clevis pin so the brake can operate and adjust properly.”
While in the shop, Bendix recommends that air brake inspections should include:
- Conduct a 90- to 100 psi brake application and listen for leaks
- Measure chamber stroke at each wheel end to ensure proper brake adjustment
- Examine friction material for good condition and minimum thickness
- Measure/inspect each rotor and drum for wear and heat cracking and/or leopard spotting
It is difficult to predict exactly when brake components need to be inspected and/or replaced. The vehicle’s duty cycle will impact the frequency of maintenance. “Obviously, the more cycle time you have, the more often you should inspect and lubricate the components,” says Holley. The environment is also a big issue for brakes. Compared to highway applications, brakes on vocational trucks are often exposed to mud, sand and water. These elements create additional wear factors.
Ensure Proper Adjustment
Brakes being out of adjustment is a common DOT citation. On an air brake system the slack adjuster is used to adjust the brakes. It takes up the slack is the stroke as the friction surfaces wear away. Modern trucks are equipped with automatic slack adjusters that adjust themselves during full brake applications and should only require manual adjustments during installation.
“Always follow the manufacturer’s guidelines for slack adjuster operation and trouble shooting,” says Pfost. “When backing off a Bendix slack adjuster, it could take up to 70 lb.-ft. to back off. Leave the wrench on the adjuster nut or mark the nut and slack adjuster body and cycle the brake a couple of times to see if the wrench turns in the clockwise direction. This will tell the tech if the slack is adjusting properly. If there is no resistance when backing off the slack, the slack adjuster is bad and should be replaced.
After they are initially set up, a properly installed automatic slack adjuster that is lubricated and operating properly should never need to be manually adjusted. If it is out of adjustment, you need to identify the underlying cause.
You also need to ensure the brake stroke length falls within the recommended range so the brakes are functioning correctly and you are not cited with a DOT violation. To measure the stroke length, check the distance from the chamber mounting face to the pin with the brakes released. Then check this same distance after a full brake application. The difference between the two is the chamber stroke, and the maximum allowable stroke is based on chamber size and type.
One of the leading causes of brake failure is the cam brake stroke measurement is not taken with a tape measure. “Most of the time technicians just readjust the slack adjuster at the PM instead of measuring,” says Holley.
If the automatic slack adjuster is working properly and the brake stroke length is out of adjustment, Bendix recommends you check:
- For proper operation of the brake camshaft and cam tube
- The cam head and rollers for abnormal wear
- The brake’s friction blocks for wear level and cracks
- Camshaft bushings for wear. Check radial and axial end play
- The brake drums for maximum diameter and surface finish
- Brake shoe return springs to ensure a proper return to the ‘zero stroke’
- Return spring on the air chamber or on the service side of double diaphragm spring brakes
- The clevis pins connecting the chamber to the automatic slack adjuster to ensure they turn freely
Stop Air Leaks
The two types of braking systems in use today include hydraulic and air. Air brake systems are used on heavy trucks because they can reliably stop an 80,000-lb. load in a short distance. Unlike hydraulic brake systems – where a leak causes a loss of braking performance – a leak in an air brake system causes the brakes to be applied. Air pressure is required to release the brakes. But to keep the truck moving, the air system must be properly maintained and air leaks must be kept in check.
Loose fittings can often cause air leaks. To check for air leaks you can park the vehicle and monitor the pressure gauges. With the service brake applied, you should not lose more than 1 psi per minute. While minor leaks may be difficult to find, you should listen carefully for leaks during the pre-trip walkaround.
“Just because you don’t immediately see or hear any leaks doesn’t mean they’re not present,” says Richard Nagel, Bendix’s director of marketing and customer solutions – Air Supply & Drivetrain. “If you notice that it’s taking significantly longer to charge the tanks – say, three or four minutes compared to one or two – then that’s a sign that your air brake system is losing air. The same thing applies if you notice the system is charging more often.”
For most trucks, as the brakes are used, the air compressor should kick in at approximately 100 psi and kick out at approximately 125 psi. If the pressure drops to 60 psi, a low air warning light and/or buzzer should be triggered. As the pressure drops lower, the spring brakes apply between 20 to 45 psi.
Moisture is the Enemy
Moisture and air brake systems don’t mix. Excess moisture can degrade brake actuation performance and cause corrosion, shortening the service life of air system components. In cold weather, the moisture can even cause the system to freeze up.
To combat moisture, all air brake systems should be equipped with a dryer cartridge that removes both water and oil from the system. This dryer cartridge needs to be maintained and the compressed air tanks should be periodically drained to minimize moisture in the system.
“Service the air dryer per manufacturer recommendations,” notes Nagel. “Drain air systems regularly.”
In fact, it is often advised to drain air tanks daily. If water is found in the system, take corrective action. Check to make sure the charging/drying system is operating correctly. Check for air leaks in the system and check the governor to ensure a signal is being sent to purge the air dryer. Also verify that the drying cartridge is functioning properly and that the desiccant cartridge isn’t saturated. If it is saturated, replace the cartridge.
Clean, dry air can go a long way toward ensuring brake system reliability.
Don’t Skimp on Replacement Parts
The OEM air brake systems are designed to meet mandated performance standards outlined in FMVSS 121. Aftermarket replacement materials, such as friction materials, can change the braking performance. In some cases, the system may no longer conform the FMVSS 121 requirements.
To help mitigate any loss in performance, the Maintenance Council (TMC) recommends the torque value of aftermarket brake lining should closely match that of the original equipment that it is replacing.
Air brake systems are made up of many separate parts, all of which must be in good condition to provide reliable operation. Pre-trip inspections by drivers and periodic more through inspections by technicians are key to keep trucks safe and on the road.