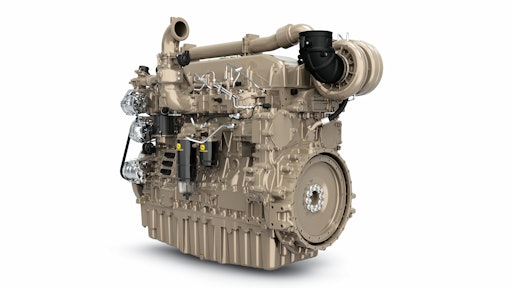
As the off-highway industry, including construction, navigates changes to emission regulations, the growing adoption of electrification, and the development of renewable fuel technology, manufacturers are working to optimize and adapt their diesel engines.
Diesel engine technology still has a long life ahead, especially for heavy-duty off-highway applications like those found in the construction industry. The path to a sustainable future does not rely on one solution. While battery electric power will play a key role in the lighter-duty equipment segment, internal combustion engine technology will continue to be one of the most viable near-term solutions for some heavy-duty applications.
To support this multifaceted approach to power, companies are developing more choices to meet the needs of the off-highway equipment industry, including renewable fuels, battery electric, hybrid electric and advancements to internal combustion engines.
Optimizing Large Engine Architecture
Diesel engines have long been the workhorses of industries from agriculture and forestry to construction and mining. Their efficiency and durability make them a critical solution for powering heavy-duty equipment. At the same time, industry experts know that it must invest in and evolve this technology to meet the challenges of today and tomorrow. One of the primary ways to do this is by exploring and vetting the most viable renewable fuel solutions.
Anticipating the potential for these fuel types, some engine manufacturers are developing engine architectures with features that will more easily allow these engines to burn non-diesel fuels while having similar engine performance. This new engine architecture features dual overhead cams that will adapt its engines for spark ignition to burn liquid and gaseous fuels.
The Impact of Changes to Emission Regulations
Previous changes to emission regulations were challenging for manufacturers and end users regarding the overall equipment design and new packaging requirements for emission-compliant engines. As the industry prepares for the next iteration of emission standards with U.S. Tier 5 and EU Stage VI, some engine manufacturers are optimizing their engine technologies now. That means developing solutions that will create new value for end users and prepare their equipment operations to help minimize disruption for contractors in the adoption of new technologies such as electric drivetrains and renewable fuels. This new engine architecture enables variant extensions that can unlock the potential for broad integration of renewable fuels with combustion engines.
More Power, Smaller Engine
Equipment owners are often looking for more power in a smaller package.John Deere Power Systems
More Power Density
The off-highway equipment industry has navigated rapidly evolving emission regulations and increased demands for power density. To meet these changing standards, an engine must have more power per liter. More power per liter allows machines to work faster, lift more and operate more efficiently. If it is smaller (many are), the engine’s reduced footprint helps save space while meeting the needs of heavy-duty applications.
More power per liter allows machines to work faster, lift more and operate more efficiently.John Deere Power Systems
No Aftertreatment Required
One of the biggest pain points identified by OEMs and end users is the increased complexity of aftertreatment that can come with larger engines. One engine with peak power ratings from 572 kilowatts (kW) to 677 kW (767 hp to 908 hp) and new combustion technology does not require aftertreatment, meaning users have one less fluid to manage.
Ideal for heavy-duty mobile equipment, it features a rear gear train, which produces excellent direct power, and options up to two rear aux drives for a total of 902 newton meters (665 pound-feet) max torque and provides quiet operation. The new combustion technology features a simplified air system with fixed and wastegate turbos, allowing the engine to meet emission requirements without applying aftertreatment. A high-pressure common-rail fuel system delivers optimized fluid consumption, and the diamond-like coating improves biodiesel compatibility and system robustness.
Diesel Engines Continue to Play a Role
Manufacturers are helping transform the diesel engine landscape as the off-highway industry continues to navigate changes in power trends and technology. By optimizing engine technology to build in flexibility for renewable fuels, manufacturers are not only supporting contractors in future-proofing equipment operations but also contributing to a more sustainable future for the industry. As the world continues to seek cleaner energy solutions, the adaptability of diesel engines will play a crucial role in shaping the future of power generation.