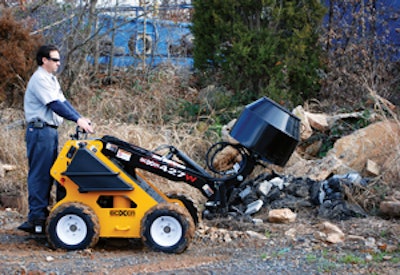
Using professional equipment will get you professional results. Jobsite mixing leaves the contractor in control of batch size, timing and details of the mix such as additives and color.
As a concrete contractor, you're probably using concrete mixes, repair mixes or overlays on a daily basis. You want to ensure proper and efficient mixing of your materials. Jobsite mixers are a great resource to help you achieve this.
There are times for a ready mix truck and times for jobsite mixing. Anytime you have a project that requires more than 5 cubic yards of concrete or a continuous pour, you'll most likely call in a ready mix truck. For smaller jobs, projects that will be poured in stages, or on jobsites not easily reached by ready mix trucks, jobsite mixing offers you flexibility and quality control.
Hand mixing
Hand mixers are the most portable and flexible of jobsite mixing equipment. Contractors can carry hand mixers up or down stairs and easily transport them around a jobsite. While some contractors mixing small batches of concrete might turn to a drill with a mixer paddle attachment or a hoe and wheelbarrow, those devices aren't designed for professionally mixing concrete and could result in a mix that won't harden like it should, has air pockets or won't meet its intended strength. A hand mixer designed for mixing concrete and similar products will prevent those errors.
"A professional mixing tool will help ensure proper material integrity by mixing it correctly," says Bruce Coleman, product manager with Multiquip. "Sometimes a product bag or bucket will suggest an RPM at which to mix a product. Our mixers employ gear boxes with adjustable RPMs that allow you to spin at an optimum rate the product suggests."
The amount of mixing a contractor does on the job will dictate what kind of mixer he might want to have on the jobsite, Coleman explains. If a contractor is typically mixing small batches a few times a week in 10-gallon buckets, he can get by with a single-paddle hand mixer. If he's mixing several 20-gallon batches daily, he might want to consider a dual-paddle model. "In a one-man operation, where a contractor doesn't want to waste time mixing, that's where we would suggest an automatic system," Coleman explains. "These mixers can handle a great volume of throughput every hour."
To optimize a mixing solution, various geometric paddle designs are available to match the material and viscosity. Choices are available for conveying material upward from the bottom of the tub (usually for heavy bag mixes), downward (normally thin liquid products), and for parallel swirling action where higher shearing force is necessary (thick fillers, mortars and sealants).
Attachment mixing
Another option for jobsite mixing is a concrete mixer attachment. One of the benefits of this type of mixing equipment is oftentimes a concrete contractor will already have a host machine working on the jobsite. A skid-steer loader, compact utility loader or other host machine can use a variety of attachments for various projects on the jobsite, including demolition, excavation, grading and leveling, and concrete mixing and dumping. There are several cement bowl attachments available, with models typically screwing onto a high torque auger power head. The hydraulics of the host machine powers the bowl's turning action.
Common sizes of mixing bowl attachments for skid-steer loaders include 5- and 9-cubic-foot models. Bowls for smaller equipment run a bit smaller. Boxer Equipment offers a 3.2-cubic-foot cement bowl mixer for its Boxer line of compact utility loader.
"One of the advantages of an attachment is a contractor can mix 200 pounds of concrete, then drive it where it needs to go and precisely dump it without the need for a wheelbarrow," says Andy Lewis with Boxer Equipment.
Ideal projects for a mixer of this size include a small patio, small batch work, or a job where you need to move concrete around the jobsite such as a fencing contractor who might use his host machine to drill holes with an auger then use the equipment to mix and pour concrete.
Portable mixers
Portable concrete mixers are a common sight on construction projects. Sizes can vary from a 2-cubic-foot capacity to a 12-cubic-foot capacity, with larger models available with a tow package.
There are some jobs for which you will clearly need a ready mix truck, but Gary Wiebe, plant manager with Crown Construction, explains there are advantages to jobsite mixing. "A truck will charge a minimum for travel time and amount of concrete, but with a portable mixer there's no waste because you mix what you need. And you also always have on-time delivery with the portable mixer - when you mix your own concrete you get it when you want it," he says. "Contractors also have more control over the mix and can add more stone or cement to get the exact mix they want."
When deciding what size mixer to purchase, contractors should look at their typical job size. You can always mix a small batch in a larger mixer, but your productivity will be hindered if you choose a mixer too small for your company.
"Generally, if a contractor is doing a small patio or a job like that, a 4- to 7-cubic-foot mixer is fine. You'll see a lot of that size doing patch work, too," says Ed Varel, engineering project manager at Stone Construction Equipment, Inc. "When you get to the 9-, 10- and 12-cubic-foot mixers, you're doing something more than patch work. You might be doing work in a larger confined area project like a large patio, sidewalk, garage or platform."
Concrete mixers are fairly basic units and don't vary much from manufacturer to manufacturer, Varel says. But there are a few options and quality features to look for when choosing a jobsite mixer.
Make sure the concrete mixer you choose, whether it's a tow-behind unit or an attachment, is built with quality steel thick enough to offer you longevity and durability. A simple design with minimal consumable parts will ease maintenance. When choosing a tow unit, check for the proper tongue weight, tow package and safety chains to ensure safe towing.
Another safety issue concerns the mixer itself. "You want to make sure you have a drum lock so you can mix without the drum rotating into the dumping position," Varel says.
The decision between a steel mixing drum and a polyethylene mixing drum is something else to consider. Most units come standard with the steel drum, but manufacturers offer a poly option on some units. A poly drum has a higher price point but allows for fast and easy clean-up. Contractors mixing small batches or multiple batches a day will find a time-saving advantage with the poly drum.