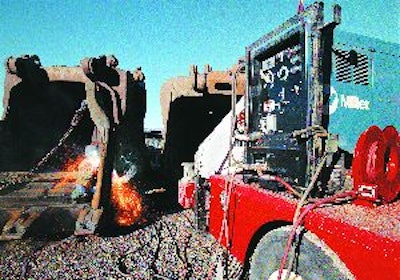
When selecting a welding unit for on-site equipment repair, several variables come into play. What type of welding will you perform? How much continuous power will you need? How much does the unit weigh? The right unit for the job depends on the answers to these and other questions that apply to your unique situation.
Simplicity vs. productivity
The simplicity of stick welding makes it a natural for equipment repairs. "It is simple to set up," says Eric Snyder, product manager for engine-driven welders at Lincoln Electric. "You don't have to worry about a wire feeder."
Instead, you just clamp the ground connection to the work, hook the electrode to the other cable and start welding. "The simplest equipment will handle a wide variety of repair applications," Snyder adds. "Most people in the field want the simplest setup possible. There is less to go wrong - less to maintain."
John Leisner, product manager, Miller Electric Mfg. Co., agrees, noting, "[Stick] is simple, inexpensive and easy to use, and is very common because of it. All you need are two leads and your electrode."
But stick welding has a reputation for being a little more sensitive to operator technique. "The welding technique is more difficult with stick than with GMAW or MIG welding," says Leisner. "It requires a little more hand/eye coordination. You have to be manually feeding the electrode, as well as progressing in travel."
Even so, the expertise required for stick welding has become less demanding than in the past. "Stick is so much easier to use today than it was even 10 years ago," says Leisner. "It is not like you have to be an expert."
The material costs also favor stick welding. "When you go to buy materials, generally you pay less on a cost per pound basis for stick electrode than for wire," says Snyder.
Larger repair jobs, however, may favor the use of self-shielded, flux-cored, wire welding. "You are definitely going to put down more weld metal in a given period of time with GMAW or flux-cored vs. stick," says Leisner.
When choosing between the two methods, factor in the quicker setup time of the stick welding process vs. the speed of the wire welding process. "You start up your machine, you weld with stick and you are done in an hour," says Snyder. "Now, if you are looking at an eight-hour job, you would probably like to switch to wire. For bigger jobs, you are going to have more productivity with wire."
When wire welding, you will generally need a higher-output machine. "This does depend on the diameter of the welding wire," notes Snyder. "People sometimes want to go to a bigger diameter welding wire because that also improves productivity."
A 200- or 250-amp machine is usually big enough for most stick welding applications, Snyder indicates. "A 200-amp machine is probably a little bit on the small end for wire welding," he adds. "A 300-amp machine is probably pretty good for handling a lot of different diameter wire."
Ultimately, the determining factor between wire and stick is the size of the typical repairs. "If half of your jobs are bigger ones, then you really should look at flux-cored," says Leisner. "But if most of them are smaller, stick is probably the easier way to go."
Consider weight
Contractors are moving toward smaller and lighter service trucks. "The costs of service trucks has really skyrocketed since 2007, when the new emissions went into effect," says Leisner. "So smaller and lighter really saves them a lot of money now vs. what it used to."
But smaller trucks also mean less available payload capacity. This has driven the popularity of gasoline-powered welder generators. "More of them actually use gas than diesel because of the size, cost and weight," says Leisner. "Diesel units usually have a longer engine life than their gas counterparts and can use less fuel, while gas engine drives are typically less expensive and are smaller and lighter. We do make some light diesels, but the gas machines are still 200 lbs. lighter."
Diesel engines do offer greater longevity, but this is not often an important consideration in repair work. "Because the core job is not welding, [the technicians] will not wear out an engine anyway," Leisner points out.
However, the fuel type itself can be an issue. "Some construction sites mandate diesel fuel only," says Leisner. Since the welder/generator is bolted to a mobile service truck, you may get away with a gas engine. But on other sites, there may be safety concerns with using gasoline.
"A lot of times, the thinking is I want to match the welder fuel to the truck fuel," says Snyder. "When I get re-fueled, I can do it all at the same time. Plus, I don't have the risk of putting the wrong fuel into the welder."
Gouging determines size
Carbon arc gouging is a common practice that often determines the size of the welding unit required. Consider the case of a cracked bucket. "Generally, the procedure is you want to remove the metal down to the sound material at the base of the crack," says Snyder. "You don't just fill the crack in. One good way to do that is with the arc gouging process."
The arc gouging process consists of melting the metal using an arc created with a carbon rod, then using compressed air to blow the molten metal away. "Usually, a separate compressor supplies the air," says Snyder. "However, a few engine-driven welders are manufactured with built-in compressors."
Under-sizing a welding unit for carbon arc gouging ranks among the most common mistakes. This problem is compounded when you try to use carbon rods that are too large for the welder output. "Then you get the call that the machine doesn't work real well," says Snyder.
He explains, "Every engine-driven welder will do arc gouging. The difference is how big a carbon electrode it can support. Gouging is an extremely demanding process. It is both high amps and high volts."
There are several different sizes of carbon electrodes available. "It is really a productivity issue," says Snyder. "The bigger the carbon electrode, the faster and deeper you can go. This is a repetitive process."
As a general guideline, you can gouge down approximately as deep as the diameter of the carbon rod with each pass. So if you have a 3/8-in. carbon rod, you will be able to gouge to approximately 3/8 in. per pass. But a 3/8-in. carbon requires a big machine. "If you are going to run that carbon, you need to have a machine that has 450 to 600 amps of welding output," says Snyder.
You can get away with a smaller welder if you use a smaller carbon rod. However, your production rate will correspondingly decrease. "If you have a 3/16-in. carbon rod, which is half the diameter, you are probably going to need a 250-amp machine," Snyder advises. "If you have a machine that is smaller than 250 amps, you would probably not have enough output to run that carbon rod at full capacity. It is going to take you a lot longer to get the same thing accomplished."
Leisner adds, "For carbon arc gouging, engine drives with a 300-amp output work best... They can run 1/4-in. carbons, which is the most common diameter of carbon arc sold. If you need to remove a lot of metal, an engine drive with 500 amps of output power will allow you to run 3/8-in.-diameter carbons for increased speed and metal removal."
Compressed air can also be an issue with carbon arc gouging. "You want to keep compressed air blowing away the metal to get a good result," says Snyder. "Generally, you want to have about 80 psi or more of compressed air."
Generator quality issues
When performing repairs, a grinder is most always used in conjunction with the welder, with the generator end powering the tool. "Practically any welder/generator can operate grinders," says Leisner.
But to ensure optimal performance and prevent tool damage, the quality of the power is important. "Some light-duty generators don't hold the voltage up where it needs to be when they are under heavier loads," says Leisner.
Although the label may list the amp rating (i.e., 13 amps), power tools actually operate in watts. Wattage equals amperage multiplied by voltage. "As the volts go down on the generator, the amount of amps the tool needs to keep operating goes up. As you turn up the amps, you are generating a lot more heat in your tool," Leisner explains. "If the generator goes down to 110 or 105 volts, the amperage is 15 or 18 amps, rather than 13. So you are really putting more heat into that tool than what it was designed for."
The amount of power you need from the generator really depends on what you plan to do with the welding unit. "Generally, machines with 3,000 watts are plenty for a grinder," says Snyder. "Now, if you start getting into things like plasma cutting, you are going to want an engine-driven welder with more generating power than 3,000 [single-phase] watts. You definitely want a machine that is going to handle 10,000 watts or more."
Although you can do some plasma cutting under 10,000 watts, you may not get the full output of the plasma cutter. "You probably want at least 12,000 watts of single-phase power to cut 3/4 in.," Snyder advises.
Another key consideration is whether the machine will be used to perform more than one operation at a time. For example, one service tech may be performing metal preparation with a grinder, while the other is welding.
This is where welder/generators - with independent generators separating welding and generating power - shine. "A sudden load from a grinder does not affect the welding arc," says Leisner.
Of course, selecting the correct welder/generator is only part of the total solution. There are many potential pitfalls, including literally hundreds of choices when it comes to electrode and wire selection, as well as various choices of welding cables, etc. To find the best combination for the work you perform most often, obtain expert advice from your local welding equipment supplier.
Duty Cycle Defined
"Duty cycle, as defined by the National Electrical Manufacturers Association (NEMA), is the ratio of arc time to total time, expressed in percent," says Eric Snyder, Lincoln Electric. "For example, if the output is applied continuously for six minutes within a 10-minute period, the duty cycle is 60%."
Simply put, duty cycle is an indication of a unit's ability to operate without overheating. It tells you how long you can continuously operate the machine.
"For example, Miller's most popular welder/generators are rated for 100% duty cycle, which means you will not hurt the unit if you run it for long periods of time with the amperage turned wide open," notes John Leisner, Miller Electric.