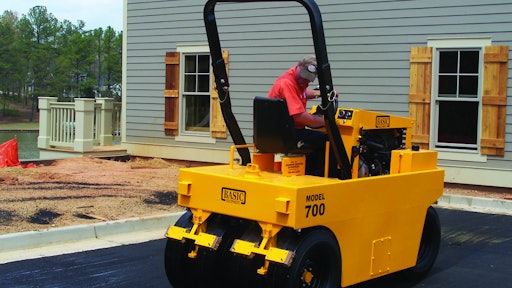
While most contractors may use a steel drum roller to complete their paving jobs, a time can come when rubber-tired rollers might be a consideration. Also called pneumatic rollers, rubber-tired rollers used with steel drum rollers provide contractors with a better base before paving, achieve a better density or compaction, and improve the look of the finished product.
Pneumatic Rollers
Before purchasing a pneumatic roller, contractors should understand the role a rubber-tired roller plays in a paving operation. Compared to using only a steel drum roller, pneumatic rollers have many benefits for contractors. "On any paving job you need a roller, a lot of guys just use a steel drum roller," says Bill Wilkens, engineering manager at Leeboy. "For guys that are getting a little bit bigger, it [pneumatic roller] weighs just a little bit more, in addition it's versatile. It can be used for paving, and it puts that nice smooth finish into the job. It allows the tire pairs to oscillate for any imperfections in the paving process."
The manipulation of the asphalt comes from ballasting the pneumatic roller to achieve a specific weight. "The front four tires will rut the material, and along in the back you have five back tires that will fit around the four tires," says Chris Connolly, product manager for asphalt Bomag. "You've created a situation where not only have you vertically put pressure on the material by rutting the material, but you're coming along and counter-rutting." The effect of the rutting and counter-rutting is the manipulation being used to bring density and stiffness to the material, Connolly says.
Pneumatic rollers help achieve compaction; however, compaction is often a greater concern for larger, highway jobs compared to parking lots. "Your typical parking lots and driveways are not necessarily as concerned with density as a neighborhood street or highway because they aren't getting a lot of heavy truck traffic," Wilkens says."The asphalt base may be a little thinner or maybe the subsoil preparation is a little different than the highway so a small roller is there to do compaction but it's not used to get the real high dense numbers like on the highways." Regardless of the project, the pneumatic roller helps contractors achieve a consistent density.
Unlike steel drum rollers, pneumatic rollers are able to conform to the surface being paved.
"Using rubber tires that are air inflated and have some give conform to the work surface whether it is rolling stone or asphalt," says Shannon Chastain, owner of Basic Equipment. "In comparison, a steel drum roller has no give to it causing a bridging effect over parts of the work surface. In the design of a rubber-tire roller every wheel on it can oscillate, and in addition, you have the flex and give of the rubber tires as well."
This is especially useful with patching utility cuts or potholes. By having all wheel independent movement the pneumatic roller is able to dip down into a pothole and compact it much more thoroughly, Chastain says. "No matter what the contour of terrain on the work surface, the pneumatic roller is going to be able to get a more consistent compaction density across the entire work surface," he says.
Bruce Monical, the marketing manager of Hamm, says contractors using a pneumatic roller can achieve a compaction that will eliminate the voids of air and space in the asphalt mix that would otherwise cause potholes to appear. "One thing that happens when rubber-tired rollers roll over the top is that it compresses the asphalt making it more dense," Monical says. "There is a side affect with a rubber-tired roller because that rubber-tired roller kneads it gently at the surface driving the bigger stuff lower and bringing the fines to the surface. A side affect to that is it seals the top better." According to Monical, if the fine sands are at the top it is sealed better, and the chances of water going into the asphalt when it rains decreases.
In most situations, pneumatic rollers are used as the intermediate roller in a paving train following behind the breakdown roller about 50-100 feet.
"Most guys buy a pneumatic roller to complement their use of a steel drum roller," Wilkens says. "They might do some compacting with a steel drum roller, and as they approach the end they may run over that same asphalt with a pneumatic roller to improve the overall finish of the material."
Pneumatic rollers can be used on several different projects such as subdivision streets, large parking lots, and driveways. Pneumatic rollers are also used on chipseal projects. "When you do chipseal if the rocks, chips, or small aggregate that you put in the oil, are rolled with a steel drum roller you will crush it and break the rock," Wilkens says. "Pneumatic rubber-tired rollers will set the rock into the oil a little bit more and the point or the edges of the rock won't be broken by the rubber tires."
The machines can be used on other projects besides asphalt, Connolly says. "A lot of times these machines will find themselves on different types of material," he says. "Anything that is tough to move, particle wise, you will find a pneumatic."
Before purchasing a pneumatic roller, contractors should consider several points such as the asphalt mix they are using, the types of projects they are completing, and the equipment their competition is using.
"One consideration would be what asphalt mix they are using and what target density requirement they are on," Monical says. "It's really a matter of what the job is and if the job would require them to have a pneumatic rubber tire roller."
Connolly says that contractors should consider purchasing a pneumatic roller when they find themselves unsatisfied with the results of a conventional paving train. According to Connolly, people are looking for longer lasting mix designs, as a result the mix designs are getting stiffer. Due to the stiffer mix designs compaction is more challenging to achieve, and over-rolling with a steel drum will result in breaking aggregate, Connolly says. "If I've got a tougher mix design, if I'm having problems getting density with the double-drum vibratory roller, or if I'm over compacting to get density and I'm crushing the aggregate," Connolly says. "My solution is the pneumatic tire roller."
While requirements of the job may factor into a purchase decision of a pneumatic roller, Chastain says that contractors should look at their competitors. "It's a situation many times of what is the competition doing first off and being able to compete with the competition on the quality of work," he says. "Customers are kind of forced into the situation to be competitive. Ideally, every asphalt-paving contractor would be running a pneumatic roller." Chastain says that the benefits to using a pneumatic roller are there, but they aren't always seen immediately.
Benefits of purchasing
Bomag offers contractors three pneumatic rollers: the BW11RH, the BW24RH, and the BW27RH. The BW11RH has nine tires with a Cummins 4B3.3TA diesel engine. The other two units, the BW24RH and BW27RH, have eight tires and can be ballasted to provide specified weights.
If contractors are looking for a smaller unit, Shannon Chastain's Model 700 pneumatic roller is one possibility. "Our number one goal in designing any equipment is to make it as simple as possible," Chastain says. "Job site breakdowns and repair work are all as simple as possible and as minimal as possible." The unit is a 1 ½ to 3 ton class roller weighing 3,000 to 6,000 pounds. It has all hydrostatic drive and all wheel oscillation with seven tires.
Another unit is the Leeboy 420. The roller has four front tires and five rear tires with a 39 horsepower Koboda engine. The small size of the unit makes it easy for contractors to maneuver in small areas being able to make small, sharp turns.
Rosco, a LeeBoy Company, offers a 6.5 to 15 ton ballastable nine wheel rubber tire roller the Tru-Pac 915 Pneumatic Roller. The Tru-Pac 915 has the choice of engines: 85 HP Kubota Turbo Diesel or 83 HP Caterpillar Turbo Diesel. Key features include: Responsive Hydrostatic Drive, Articulated Frame for Tru-tracking Compaction, ROPS with Sunroof, Suspension Operator’s Seat, 100-gallon Pressurized Water Spray System, All-wheel Oscillation, Coco Mats with Spring-loaded Scrapers & can be equipped as an 11-Wheel Roller that is Optional.
Contractors can choose from five different models manufactured by Hamm. Hamm offers contractors one unit with three different optional weights and a second unit with two different weight options.
Keeping rollers in top condition
When making the investment to purchase a pneumatic roller it is essential to maintain the unit in top condition. There are several areas of the unit that must have continued maintenance to achieve it.
Contractors must regularly check tire conditions and air pressure. "By adjusting the air in the tire, you're adjusting the ground contact pressure," Connolly says. Therefore, the air pressure must be checked before each roll to ensure proper wheel load.
Many variables go into determining the life of a tire. Connolly says that the kind of material the rollers are on as well as the number of hours it is used will affect the life of the tire.
It is also important for contractors to maintain proper care of the coco mats to preserve the life of tires. "Checking and/or replacing coco mats on the tires is one step to follow," Chastain says. "The coco mats pick up some of the material off of the surface. They act like a brush to brush that material off of the tire to prevent material from collecting." Chastain says that if contractors operate pneumatic rollers properly and use caution tires can last up to five years.
"Keeping loose asphalt or any picked up asphalt from building up on the unit is part of the regular maintenance that would help keep the unit running for many years," Wilkens says.
Along with proper tire care, it is important for contractors to follow standard general maintenance practices. "The drive system should be maintained as the manufacturers ask them to maintain it," Monical says. "Oil changes, filter changes, the hydraulic system needs to be maintained." Due to the large size of the equipment, Monical says that it is especially important to maintain the condition of the brakes.