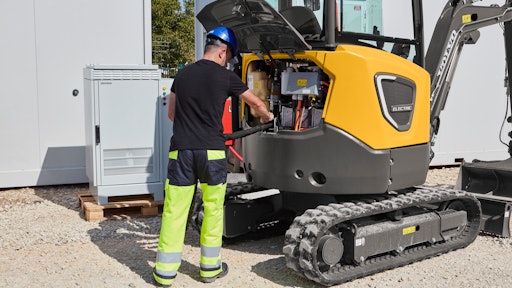
The adoption of electric construction equipment is quickly growing domestically and globally. Driving factors include noise reduction; lower operating fuel and maintenance costs; government emission regulations; federal and state tax credits; carbon credits and offset, and environmental, social and corporate governance goals.
Hurdles to more widespread adoption include upfront costs because electric construction equipment is typically more expensive to purchase than diesel-powered equipment. More charging infrastructure is also necessary to support the increasing number of electric vehicles (EVs) in construction. Battery life can still be limited for larger vehicles and applications.
Electric Construction Equipment Offerings
VOLTEQ begins production of the fully electric 20kW SKY 1000 mini track loader with a 1,000-pound capacity in the first quarter of 2024. The larger SKY 2000 with a 2,000-pound capacity will follow in the first quarter 2025.
A skid steer with a 3,300-pound capacity will be introduced later in 2025. Mini excavators also are in development. Some form of hydrogen-powered innovations could be seen as early as 2026.
Volvo currently has six electric machines commercially available: two compact wheel loaders, three compact excavators and one compactor. The company has an electric mid-size excavator in testing and is working on more.
The range of electric equipment from JCB North AmericaJCB North America
A recent IDTechEx report shows while it is in its early stages, the electric construction machine market will “benefit from other sectors having already gone through electrification and will be able to accelerate quickly with existing supply chains for batteries, motors, and other EV components that it will need to make this transition. [Original equipment manufacturers (OEMs)] are moving quickly to electrify their product ranges.”
Having started with mini-electric excavators, it is progressing to larger machines. OEM activities, policy drivers and potential total cost of ownership savings lead IDTechEx to predict a 10-year compound annual growth rate of 38 percent and growth to an electric construction machine market value of less than $150 billion in 2043, putting the construction industry on target to hit international carbon neutrality goals by 2050.
As this ForConstructionPros.com story, “Power Prospects for Construction Heavy Equipment,” noted, hesitancy to work with EV construction equipment centers on having enough power and torque to do the work, keeping equipment charged and operator training.
High-performance and fast-charging batteries are decreasing range anxiety and improving vehicle reliability and user experience. Economy, technology and resource availability will play a greater role in driving the change.
EVs are seeing high adoption rates across various industries globally, as this ForConstructionPros.com story, “What’s Driving Commercial Vehicle Electrification?,” noted.
“As carbon reduction goals and regulations continue to gain traction, transitioning to electric is an easy and significant way to reduce a fleet’s emissions,” Lars Arnold, product manager – sustainable power, Volvo Construction Equipment, said.
Arnold noted that early adopters have been pleasantly surprised by how quiet the machines are and how much less vibration operators feel.
Operating indoors with electric equipment is preferred to eliminate hazardous exhaust.JCB North America
The ability to perform work for which diesel machines may not be right is another perk, Arnold said.
“This includes work in densely populated areas, night jobs, indoor demolition, agriculture, food production and high-dust environments where sparking is a concern,” he added.
Idle time is another big differentiator, Arnold said.
“With diesel equipment, operating time is defined by engine runtime; a lot of those hours are counted while the machine is idle,” he said. “With electric, as soon as the operator stops working—such as a landscaper waiting for a pipe to be placed in a trench they just dug—the motors turn off and no operating hours are accumulated.”
Jobs that can rack up 10,000 hours on a diesel machine might only add 6,000 hours or 7,000 hours to a comparable electric machine, Arnold said, adding that saved hours lower operating costs and improve resale values.
“Some buyers may be hesitant because the initial purchase price is higher for electric, but it’s important to remember how much money they will save on maintenance and fuel,” Arnold said.
Arnold indicated that these factors significantly reduce maintenance time:
- Maintenance-free electric motors featuring auto shutoff
- Fully electric drivelines reducing hydraulic oil needs by half
- Easy ground-level access to lubrication and maintenance points
- Maintenance-free, lithium-ion batteries
Incentives on the local level through the federal level are another benefit for Arnold.
A substantial reduction in operating costs is a prime reason to make the switch to battery-electric equipment.VOLTEQ
Mike Slattery, VOLTEQ vice president of business development, said a substantial reduction in operating costs is a prime reason to make the switch. These savings result from the absence of a combustion engine that requires maintenance or eventual repair of the following:
- Oil, air, and fuel filters
- Engine coolant
- Radiator
- Thermostat
- Fuel sensors
- Injectors
- Belts
- Alternators
Savings by charging with electricity versus gas or diesel varies based on regional markets and fluctuations in commodity prices, Slattery added.
Slattery also said improved jobsite conditions for employees working with zero emissions and greatly reduced decibel output is a significant benefit, adding “this is nice to have for outdoor work and essential when working indoors.”
According to Slattery, VOLTEQ’s battery-powered SKY 1000 can also be operated by remote control, separating operators from any equipment vibration and distancing them from dust or debris at the point of work and providing an opportunity for improved visibility.The VOLTEQ battery-powered SKY 1000 can be operated by remote control, separating operators from any equipment vibration and distancing them from dust or debris.VOLTEQ
Charging Infrastructure Challenges
“Electric is not a fad—it’s here to stay,” said Arnold. “We can expect charging infrastructure to remain a top priority for the EV industry, construction industry and more.
“Charging is the part we get asked about most, but the options are better than some may think. The more power you can put into your electric machine, the faster it will charge. It’s like filling your vehicle with a gas station pump versus a gas can.”
The first option that is “built-in” is regular grid charging, according to Arnold.
“We recommend a 240-volt, 32-amp Level 2 alternating-current (AC) charging setup using an SAE J1772 charging adapter or J plug. That may sound complex, but it’s the same setup EVs usually use,” he added. “If you don’t already have the outlet needed for this, it is an easy update to make. You can also charge the machines on a common household 120-volt network, but it takes longer.”
A direct-current (DC) fast charger is another option for a quick charge to finish out the day, Arnold noted.
“At Volvo, our DC fast charging solution charges directly with 48 volts DC and up to 360 amps. Charging times are drastically reduced. For portable charging, we partner with a few companies,” he said.Charge during a workday pause. When possible, charge from mid-level to full as opposed to draining the battery.Volvo Construction Equipment
Micro-grid and on-site generation are promising technologies that can replace existing fossil fuel generating equipment, provide electric energy to battery vehicles and machines and power other site needs such as lights, Arnold noted.
Slattery said having charging plans in place before purchasing or leasing electric equipment is ideal.
Factors to consider are:
- The number of hours or shifts per day that the equipment will be used.
- The duty factor needed. “Digging or moving materials can be less demanding and allow longer run times while powering motorized attachments, such as an auger or trencher, can draw more power, reducing run times by approximately 40% to 50%,” Slattery said.
- Necessary charging requirements (voltage and amperage) and the connector type required to recharge. VOLTEQ’s SKY 1000 has a 20-kilowatt lithium-ion battery that can be plugged into a common 120-volt/20-amp single-phase outlet after a typical day’s work and recharge in 5 hours to 7 hours. For machines with larger battery capacity, higher voltage and amperage and three-phase circuits may be necessary. Ideally, equipment is equipped with an on-board smart charger offering faster charging ability when suitable circuits are accessible, Slattery said, adding that VOLTEQ’s SKY 1000 includes a smart charger compatible with 95 volts to 265 volts, making it possible to reduce charging time by almost half when the higher voltage circuit is available.
- Whether charging is required on the jobsite or if sufficient run time is available to meet daily requirements before moving equipment to a location where charging is possible. If charging at the jobsite is necessary and power is not already available, contractors should explore options for battery storage packs, said Slattery. While a generator is another option, “this is generally viewed as contradictory to the point of having electric equipment,” said Slattery, adding it may be possible to run a more powerful generator for a shorter period to recharge, greatly reducing emissions.
- Quickly and easily swapping batteries at the jobsite is not yet common for mobile construction equipment because of battery size, capacity, cost and weight but will change as technology advances, said Slattery. He added that it is more practical on less demanding platforms or where shorter duty cycles are needed.
Charging infrastructure challenges with electric construction equipment differ from that with an on-road vehicle, says Lee Tice, JCB product manager.
While on-road EVs have specialized Type 1 and Type 2 chargers, JCB machines use built-in onboard chargers using standard plugs, such as a 110-volt outlet and a 220-volt option, for its construction equipment, eliminating the need for a specialized plug for charging, Tice said.
“If you’re on a remote jobsite, most construction sites are going to have a temporary power source from the power company that would be 110 volts, 220 volts,” he added. “Our machine [will] accept that power interface where they can charge that machine at the end of a work shift.”
JCB also offers a rapid charger.
“If the machine is going to be on a large industrial site or construction site for an extended … period, the contractor can have an electrician wire this box into the facility,” said Tice, adding that it offers onsite charging in about 2 hours.
While lower operating costs can quickly make up for higher prices of electric equipment, the initial cost can be a barrier.
“Savings of 60% to 70% in operating costs can overcome the price difference when compared to an internal-combustion-engine (ICE) powered equivalent in as little as 12 months, depending on the frequency of use,” Slattery said.
Slattery indicated that the fear of battery life being too short and expensive to replace is another challenge.
“A battery life charging cycle is one complete charge from 0% to 100%,” he said. “A 50% charge session equals [a] 0.5 charging cycle. Commercial lithium batteries in construction equipment can be rated with 2,000 to 3,000 charging cycles and estimated to provide more than 12 years of battery life.”
Replacement costs can be planned for by setting a percent of operating cost savings aside for future battery replacement. Battery costs will significantly decrease as their popularity increases in the coming years, according to Slattery.
For those who view battery life or capacity as challenges, Arnold offers these best management practices:
- Charge during a workday pause. “Because these are lithium-ion batteries, they have no memory effect,” he said. “You can top them off during a break and continue working.”
- When possible, charge from mid-level to full as opposed to draining the battery completely before recharging. “When you charge from 30% or 40% back up to 80% or 100%, it’s better for the overall lifetime of the battery,” Arnold said.
- Don’t operate an electric machine at full throttle all the time. “You usually don't need the excessive power anyway,” he added.
- Don’t worry about turning the machine off to save battery. “Most come with auto shutdown, so if you stop running the machine, the electric motor turns off,” Arnold said. “To get working again, it turns on instantly.”
“As with most things new, people may be concerned about what they don’t know or have experience with,” Slattery said. “The rental path will be one way for people to get the experience and understanding they don’t yet have with electric construction equipment.”
Arnold thinks that the rental channel is quite receptive to electric equipment and is expected to have good availability in the next few years because of its simplicity of maintenance, no fuel-related hassles for renters, mechanics at the rental center and enhanced features such as GPS and telematics that help track equipment and reduce risk of theft.
Electrification: Not the Sole Solution to Reducing Emissions
“There is no single solution when it comes to sustainable power,” Arnold said. “That's why, on various products, we are exploring technologies like hybrid, hydrogen fuel cells and alternative fuels.
“Compact machines are where electrification has started; [electrification doesn’t] work for every application. We have an electric mid-size excavator in pilot testing and are working toward electrifying bigger machines.”
“EVs do not scale very well as we start talking about the larger construction equipment such as excavators and large wheel loaders,” said Tice. “You would be looking at an enormous [number] of batteries on the machine and extended charge times ...”
JCB has explored hydrogen combustion technology for its construction equipment.
“This is not your typical hydrogen fuel cell running hydrogen through a series of plates and then charging batteries to run the machine,” Tice said. “This is an ICE running off hydrogen gas, still producing zero emission. You’re putting steam out of the tail.”
JCB focuses on compact equipment that will benefit from electric technology to keep the 8-hour runtime in the machine to avoid losing performance, Tice said.
The EC230 from Volvo is an electric, mid-size excavator in pilot testing.Volvo Construction Equipment
“Electrification is proving to be a long-term solution for construction equipment, but as infrastructure and technology become established, there is great potential for hydrogen as an alternative, clean-energy solution,” Slattery said.
“Two exciting benefits of hydrogen fuel when compared to battery-powered equipment are refueling options and refueling time,” he added. “While charging batteries can take hours, refueling with hydrogen can take minutes. The cost of hydrogen needs to come down by almost 50%, but that could come as the hydrogen infrastructure evolves.”
According to Slattery, infrastructure will make bringing hydrogen to jobsites or taking equipment to hydrogen stations for refueling convenient.
“The electrification evolution will be advantageous to the use of hydrogen fuel options,” he added. “Either a hydrogen fuel cell or a hydrogen-powered ICE will generate electricity that continuously charges smaller batteries powering the electric drivetrain of equipment rather than plugging in to replenish much larger batteries that you must stop and recharge over … longer times.”
Slattery predicted it could be 3 years to 5 years before hydrogen solutions truly enter the construction segment.
“JCB is making great progress, and the U.S. government recently announced plans for seven major hydrogen hubs across the country,” Slattery said. “Providers of fuel cells with suitable power are making their way to market. Cummins is now offering two popular displacement engines to run on hydrogen, and multiple brands of trucks are pioneering hydrogen options.”