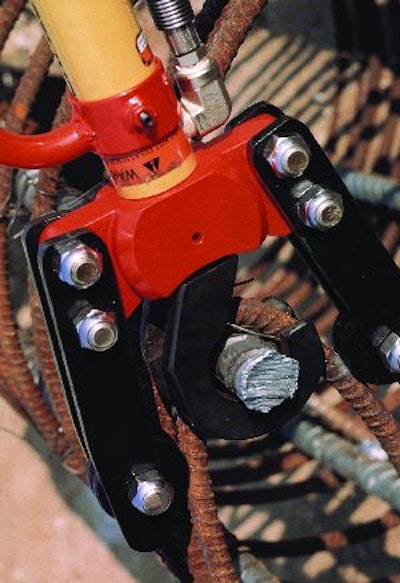
When concrete contractors need rebar cut or bent, they have three choices. They can have a fabricator pre-cut or pre-bend the rebar to the specs. They can have their crews use manual tools to hand cut or bend it on the job. Or they can use rebar cutting and bending machines at the jobsite or in their shops. Contractors say there is no difference in quality or strength between pre-engineered and do-it-yourself machine cut or bent rebar.
The benefits of owning machines
For large jobs where the steel is detailed in the blueprints, ordering all the specified rebar from a fabricator makes sense. But for smaller jobs, owning a rebar cutter and bender will get the job done more quickly and painlessly than using hand cutting tools. "As a rule of thumb, we tell people one person with one of our machines can do the work of two people in half the time," notes Frank Olah, president of rebar tool maker Fascut Industries. This means one worker can cut or bend four times as much rebar per hour using a machine compared to doing it manually.
Homebuilder Richard Cyr of Mastercraft Construction, who has two EZE Bend cutter and bender units, gets his rebar work done at least five times faster than with manual cutting. "It saves countless hours," he points out. "It makes the job so much easier. It used to be the guys who had to cut and fabricate the rebar, it was the worst job on site. Now everybody likes to do it."
Smaller rebar cutters and benders weighing under 200 lbs. can be lifted and carried by two workers for easy transport to the jobsite. Larger machines can weigh about 400 lbs., so a skid steer is needed to move them. These big machines are more often used in a shop. Smaller machines can handle up to #6 rebar, while larger ones can handle up to #8 rebar. Contractors who own both sizes usually take the small machine to the jobsite, using the larger machine indoors on bad weather days to pre-cut and pre-bend rebar for upcoming jobs.
Another benefit of using a machine is its ease in making numerous identically bent pieces. For example, when contractors need a large number of stirrups, or the square shapes used in concrete columns to hold vertical rebar, each stirrup must have accurate bends in the right places. It is difficult to get every bend the same with hand bending. "With a bending machine, you can set up a reference to put the bar against to get the same dimension of bend every time," says Olah.
Saving time and money
If rebar cutting and bending machines were not available, the main option for even medium sized jobs would be ordering prepared rebar from a fabricator. Contractors say this has two problems. "It would be more costly," says Mike Cuttle of The Jasper Company, where they use Multiquip rebar machines. "We would have to wait two to three days depending on the quantity. You can get your numbers in the field better and your quantity with your own machine, so this way you can be sure you have enough rebar." Otherwise, he says he would usually order extra rebar from the fabricator to be sure of having everything needed for the job.
The ability to make custom rebar is valued by Ian Giesler of ICF Builders. "Since most of our projects involve custom work, the EZE Bend system allows us to have near instant custom bent and cut reinforcing by ordering straight lengths of rebar and fabricating it on site on demand," he says. "We can use this system either in a 'fabrication set up mode,' where a person cuts and bends reinforcing as it is called out, as well as use the portability of it to bend tie-in dowels that were set in previously cast-in-place concrete walls into floor slabs. Without these machines, we would have a slower productivity on site and our cost of purchasing prefabricated materials would be higher. Using prefab materials can lead to delays caused by changes in design or improper detailing of reinforcing."
Giesler's company cuts and bends 99 percent of its rebar on site while building insulating concrete form wall systems. Some locations where the company builds do not have easy access to fabricators, making the use of their own cutting and bending equipment even more important.
Even though Sean O'Connor of Badger Swimpools says they have about half of the rebar they use in building swimming pools and waterparks prefabricated, they value their Fascut cutter and bender. "In the waterpark industry, there are so many things that are of irregular shape," he notes. "It allows us to have complete flexibility in the shape of the steel instead of having to rely on pre-engineered shop drawings to cut and bend things to size. A lot of people rely on getting their rebar pre-engineered, which works if their jobs are all standard dimensions. For us, it takes time to get drawings pre-engineered and approved and checked."
Giesler estimates that using on-site rebar equipment saves his company an average of $500 per residential project and more on commercial projects. "One guy can detail all the steel needed for a 5,000 sq. ft. floor of a condo in less than three hours, which includes cutting, bending, bundling, tagging and moving it to the floor where it will be used," he points out.
"The tools are basically small hydraulic cylinders," Giesler notes. "Hydraulic cylinders can withstand tons of abuse compared to electric motors. The EZE Bend power heads are lighter than most cutters and benders offered on the market and are much smaller with weight distribution in a manner that it can be used nearly all day long without two hands."
Giesler's company has adapted the equipment to meet its needs by using the hydraulic pump from the larger model on a portable unit, making it possible to bend a #5 bar 90 degrees in about three seconds.
ICF Builders also uses a gas saw for cutting entire rebar bundles to a set length. It speeds up rebar installation even more by using reverse yankee type zip tiers and forms that have integral reinforcing locks that eliminate tying splices. Badger Swimpools has a smaller Lobster machine it uses to cut out pipe penetrations and sleeve penetrations after the rebar has been installed. Its work goes faster by using rebar chairs and Max USA tiers, which are handheld electric rebar tiers that automatically tie the rebar in lap joints.
Planning ahead
Because the hydraulic pump can take about two weeks to repair, Cyr owns an extra one to keep his system up and running every day. He also bought an extra hydraulic hose as a precaution against downtime. He has found his EZE Bend machine to be reliable, with no repairs needed for the cutter or bender and only a few on the pump and hose.
Cyr's residential building company cuts and bends 90 percent of all the rebar it uses itself. That is partly because of the smaller sizes of its jobs but also because the nearest fabricator is 100 miles away, making pre-engineered rebar inconvenient. They plan all of the cuts first and then do them before attaching the bender and making the needed bends. Being able to prepare its own rebar is worth "thousands and thousands and thousands of dollars every year," Cyr says. "It saves a lot of man hours."
When the Badger Swimpools crews are working on a larger facility, O'Connor says it is more efficient to have a supplier cut and bend the steel, particularly since there are several fabricators located nearby. For small projects, they prefer using their own rebar machines. Because their jobs have slopes, curves and unique angles, cutting and bending their own rebar also saves time because the needed parts are readily available. "If you're doing a foundation, the majority of the time it's done in steps or increments, which allows them to do detailed drawings and have it fabricated efficiently," he explains. "For irregular shapes and slopes, each couple of bars is different. If you do a pool and it's 30 ft. by 60 ft. and 3 ft., 6 in. deep to 6 ft. deep, the slope is changing constantly, so you'd have to sort out the bars if you had them pre-cut. It's almost easier to do it to size there at the pool."
Even wall systems can have unusual angles. "For certain footings, it's too hard to have the rebar pre-engineered," notes Cuttle of The Jasper Company. "You have to figure it out on the job."
Low initial and maintenance costs
The entry level price for rebar cutters and benders is modest, and they run on electric power, either from wall sockets or generators. They also come with self-contained hydraulic pumps.
Maintenance requires simple but regular cleaning and lubrication of the few moving parts. Cutting blades can be flipped over on each of their eight sides when one side becomes dull, so blades last a long time. The machines themselves are also reliable and relatively easy to repair if needed. As labor costs increase, owning a rebar cutter or bender makes even more sense for concrete contractors who use rebar on many projects.
Rebar Tying Tool Helps Reduce Worker Injury
If your workers are involved in tying rebar, then you need to know about battery-powered rebar tiers. These tools can drastically reduce tying time and alleviate health problems associated with the manual tying of rebar.
A recent study by the National Institute for Occupational Safety and Health (NIOSH) reveals that using a battery-powered rebar tier significantly reduces the use of rapid and repetitive hand-wrist and forearm movements, thereby reducing the risk of developing a lower back, work-related musculoskeletal disorder.
In February 2003, NIOSH conducted the study for a Health Hazard Evaluation for Genesis Steel Service Inc. (GSSI), a construction reinforcing and structural steel contractor in Baltimore, Md. NIOSH evaluated the risk that GSSI reinforcing ironworkers have for developing back and hand musculoskeletal disorders as a result of hand tying reinforcement steel on concrete bridge decks and other large concrete slab jobs. The organization also investigated whether the use of a battery-powered rebar tier can be effective in the prevention of work-related musculoskeletal disorders of the upper extremities and back.
The study found that manually tying rebar at ground level using pliers and wire involves sustained deep trunk bending and rapid and repetitive hand and wrist movements. Using a battery-powered tier significantly reduced such movements and freed one hand to support the weight of the trunk during tying. Adding an extension handle to the battery-powered tier allowed workers to tie rebar standing erect, further reducing the potential for injury.
According to the manufacturer, Max rebar tiers are designed to reduce tying time as well as alleviate the potential for injury from repetitive movements. Max's model RB655 can tie up to #9 x #8 rebars (or any combination up to 17) using a combination of 16-gauge tie wire and a powerful twisting motor. Wire usage is regulated automatically to match the size of the tie and increase productivity. One roll of wire ties 120 to 230 ties.
For more information on the NIOSH study cited in this article, visit www.cdc.gov/niosh/hhe/reports.