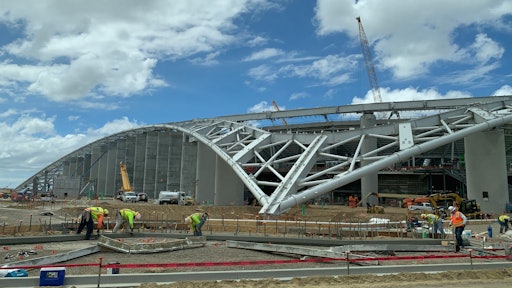
According to the American Concrete Institute CT-18, fiber-reinforced concrete is a concrete mixture that is reinforced with dispersed, randomly orientated fibers. These fibers can be used in lieu of traditional reinforcement, such as steel rebar. Defined by its composition, fiber reinforcement products for concrete fall into several different types of classification. A common classification is polymeric fiber, which include polypropylene, polyethylene, polyester, acrylic and aramid. Other types of fibers include natural, cellulose, glass and high- or low-strength steel.
Fibers may also be classified as either macrofibers or microfibers. Macrofibers have in the past been referred to as structural fibers and are intended to carry load and used to replace traditional reinforcement in certain non-structural applications and limit crack widths. They are also used to minimize or eliminate early- or late-age cracking in concrete.
Microfibers, on the other hand, are generally used to minimize early-age cracking. They are typically used at low volumes within the concrete and are easily specified.
Euclid Chemical
The Design of Fiber-Reinforced Concrete
Fiber-reinforced concrete is specified by strength, fiber type and content in the concrete mixture. Fibers added to concrete will most often not change the behavior of uncracked concrete. However, after concrete cracks, fibers can bridge the cracks and carry the tensile stresses, providing load-bearing capacity which is referred to as residual, or post-crack, strength. The level of residual strength in fiber-reinforced concrete will depend on the type of fiber material being used, along with its size, geometry, bond characteristics, dosage and, more importantly, their combined effect in hardening concrete.
In order to characterize the performance of fiber-reinforced concrete, flexural tests are typically conducted, and post-crack parameters derived from these tests are used in the design. The most common and preferred flexural test in North America is ASTM C1609/C1609M. To conduct this test, the complete pre-crack and post-crack response of a 6-inch x 6-inch x 20-inch fiber-reinforced concrete beam is recorded.
For the design of slabs-on-ground with fiber reinforcement, Chapter 11 in the American Concrete Institute’s (ACI) 360R guide provides detailed information and calculations. The load capacity of a slab-on-ground is a function of its thickness, the subgrade modulus, and the interaction between the slab and the subgrade.
Macrofibers can contribute to stress redistribution and enhance the flexural toughness of the slab after cracking. Therefore, a toughness parameter called residual strength ratio—expressed as R 150 / (T, 150) (or Re3 )is commonly used.
- Re3 = fe3 / fr (or fe3) is the equivalent flexural strength after cracking
- fr = the measured flexural strength at cracking
For a given concrete mixture with known flexural strength, higher dosages of macro-fibers will provide higher toughness values.
Specifications of Fiber-Reinforced Concrete
Euclid Chemical
In addition, fiber-reinforced concrete can be specified based on serviceability to meet specific crack widths. This alternative specification approach is used mainly for underground structures and other precast structures. For this method, a European notched beam test is typically performed to determine the residual strength at given crack widths.
For shotcrete applications, the performance of fiber-reinforced shotcrete is determined by the energy absorption capacity in panel tests following the ASTM C1550 or EN 14488-5 standards. In this instance, energy would be classified as the area under the load-displacement curve.
Determining Fiber Dosage
The quantity of fiber that is required for a project and a given application is determined by the specified performance requirements for the specific fiber-reinforced concrete being used. For plastic shrinkage crack reduction with the use of microfibers, a crack-reduction ratio is typically specified and the required microfiber determined from ASTM C1579 standards is provided by the fiber manufacturer. Microfibers can also improve hardened concrete properties such as abrasion, permeability and weathering resistance. For hardened concrete using macrofibers, the fiber dosage is chosen to meet the specified average residual strength, post-crack equivalent flexural strength or the energy absorption capabilities, which also take into consideration factors such as concrete thickness, strength, temperature and loading requirements.
For concrete slabs-on-ground, minimum dosage rates are determined by fiber manufacturers based on standardized product testing to meet industry standards. For composite metal decks, the IBC-2015 standard has a specified required minimum permitting a dosage of 4.0 lb/yd3 for synthetic macrofibers, or 25.0 lb/yd3 for steel fibers used for temperature and shrinkage control and the replacement of wire mesh.
Considerations for Mixture Design & Application
Adobe Stock Images | By bannafarsai
To assist with the workability of fiber-reinforced concrete, the ACI 544.3 standard provides recommendations and guidance to potentially modifying the mix design to improve workability.
Additionally, the use of chemical admixtures, such as superplasticizers or water reducers will assist in increasing the workability of the concrete without the addition of water. It is recommended that trial batches are performed to ensure mixture workability.
Finishing Fiber-Reinforced Concrete
Available fiber products for concrete reinforcement from Euclid Chemical are "grouped" PSI Fiberstrand Fibers, TUF-STRAND Macro-Synthetic Fibers, and PSI Steel and Blended Fibers.Euclid Chemical
The use of proper external vibration is one key factor when finishing fiber-reinforced concrete. It is generally recommended to finish fiber-reinforced concrete with the same finishing techniques and approximate timing as conventional concrete. When casting samples for testing purposes, no internal vibration within the molds can be used. Synthetic fibers in concrete can also delay the appearance of bleedwater at the surface, which can impact the overall timing of finishing operations on larger slabs.
There are a variety of broom finishing tips available to help minimize surface appearance, such as brooming in one direction only and using specific broom bristles to help align surface fibers. A torch can also be used, if necessary, to burn off synthetic fibers on the surface of the concrete but should not be used until all desired hardened concrete properties are achieved. When finishing industrial, commercial and warehouse floors where high dosage levels of synthetic macrofibers and steel fibers are used, a laser screed or vibrating screed is usually recommended.
As the uncertainties of the COVID-19 pandemic remain in 2022, fiber-reinforced concrete continues to be a financially wise and a viable health and safety solution for concrete applications. The use of fiber-reinforced concrete can also offer significant cost savings while reducing the required labor on a job site. Fiber-reinforced concrete will provide a more resilient, durable, cost-effective construction solution and still meet desired engineering properties compared to conventionally reinforced concrete. By following these best practices, you will be well positioned to utilize the many benefits of fiber-reinforced concrete on your next project, while ensuring the finished project is just as visually appealing.
About the author
Michael Mahoney is a professional engineer and the director of marketing and technology – fiber reinforced concrete for Euclid Chemical and a fellow of the American Concrete Institute.
Resources
ASTM C1609/C1609M, www.astm.org/c1609_c1609m-12.html
Chapter 11 in the American Concrete Institute’s (ACI) 360R guide, cecollection2.files.wordpress.com/2020/05/360r-10-guide-to-design-of-slabs-on-ground.pdf
ACI’s 544.4R guide, concrete.org/Portals/0/Files/PDF/Previews/544.4R-18_preview.pdf
ASTM C1550 or EN 14488-5 standards, astm.org/c1550-20.html
ASTM C1579 standards, astm.org/c1579-21.html
IBC-2015 standard, sdi.org/wp-content/uploads/2017/02/ANSI-SDI-C-2017-Standard.pdf