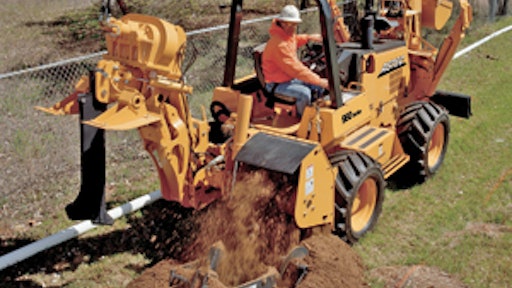
"A chain is only as strong as its weakest link" is the old saying. This is certainly true when it comes to the working end of a ride-on trencher. Chains, including teeth and sprockets, are critical components for cutting through everything from sand and loam to rock and frozen ground. How well you select and maintain these components in large part determines how efficiently and productively a trencher will perform.
When it comes to selecting digging components, resist the temptation to make due with less, advises Brent Bolay at the Ditch Witch organization. "It's human nature to try to operate without making any alterations," he says. "Many owners don't want to maintain extra inventory, or take the extra time to change teeth, chains and sprockets for different conditions. But in the long run, [your customers will] be more productive, and there are ramifications for trying to use the wrong components in the wrong conditions."
Excessive and/or irregular wear is the most common end result. "Using the wrong teeth -or the wrong combination of teeth -can cause expensive premature wear on the digging chain," explains George Whitaker, marketing director for Case Construction Equipment.
"In extreme situations, you can actually end up damaging the machine," notes Bolay.
Select for conditions
A mismatch between digging components and soil conditions can also cost you in the form of lost productivity. "If you try to use cup teeth where they don't belong, performance will drop because a cup cutter doesn't cut through material," says Brian Kenkel, product specialist at Vermeer. "It's the same for misapplication in soft conditions. If you try to use rotary teeth in soft conditions, you'll decrease footage because it isn't efficient. And the dirt will wear away the conical tooth."
Most manufacturers offer three basic types of digging teeth: cup teeth, shark teeth and rotary bits. Vermeer also offers Tiger Cup teeth, which are a cross between shark teeth and cup teeth.
Cup teeth are general-purpose teeth that are a good match for average soil conditions.
"They'll handle a fairly high percentage of the conditions that [your customers] would encounter," adds Bolay.
As conditions become more abrasive, shark teeth become a better choice. And for rock and frozen ground, manufacturers offer rotary bits. Manufacturers also offer chains with various combinations of digging teeth to suit unique needs and ground conditions.
Monitor tension
Once you've selected the right teeth and chains, it's important to maintain them for optimum efficiency. At the top of the list is proper chain tension. "All it takes is a couple of wrenches and about 15 minutes," says Kenkel.
Instruct customers to check chain tension at least twice a day -at startup and after lunch are good times. They should also check tension any time ground conditions change. The tougher the digging conditions, the tighter the chain must be.
Generally, these manufacturers suggest operating with the chain as loose as possible. Tension that is too loose has little, if any, detrimental effects to the machine. Excessive tension, on the other hand, can speed wear on the chain and sprockets, plus is hard on the boom end bearings, which can be costly to repair or replace.
"It also takes horsepower to turn a chain," says Whitaker. "A chain that is too tight requires higher levels of available horsepower in order to be productive."
Most operator manuals offer recommendations for chain tension. According to Kenkel, however, as a general rule proper tension for 30- to 80-hp ride-on trenchers is about three fingers between the boom and chain. For 80- to 120-hp machines, it's a solid three fingers.
Repair vs. replacement
It's also important to know when to replace worn teeth and chains. "Continuing to run a trencher with worn teeth only puts wear and tear on the rest of the trencher and eventually leads to costly, yet avoidable, repairs," says Whitaker.
While it's virtually impossible to dictate the number of hours at which teeth need to be changed, it's important that teeth be changed any time they are broken, or when the machine starts to experience lost productivity. Teeth with excessive or uneven wear should also be replaced.
When you check the teeth, also check for loose bolts and replace as necessary. In the case of a rock and frost chain, be sure the carbide bits are turning freely so they won't cause premature wear to the tooth or sprockets.
Monitor sprocket wear and replace as needed. "Never put a new chain on worn sprockets because this will wear out a new chain before its time," says Whitaker. "And if you have sprockets with greasable bearings, lube them at the intervals suggested by the manufacturer."
Also check channel and rock booms for wear and replace if necessary. You'll know it's time to replace channel bars when grooves begin to develop. Some manufacturers have wear bars on rock booms that are reversible, effectively doubling the bar's life.
"The most important step is to be observant," says Whitaker. "Monitor digging components on the machine and follow the maintenance and adjustment guides provided by the manufacturer. This will add life to components and the overall machine."
Astec RT960 Ride-on Trencher
INDICATE 90 ON INQUIRY CARD
Ditch Witch RT40
INDICATE 91 ON INQUIRY CARD
Vermeer RT450 Trencher/Plow
INDICATE 92 ON INQUIRY CARD
Case Trencher Line
INDICATE 93 ON INQUIRY CARD