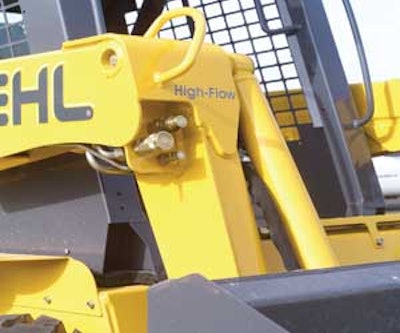
The term high-flow encompasses a wide category of skid loaders with varying flows and pressures. Flows range from 26 to 40 gpm and pressures range from 3,000 to 5,000 psi.
The flow in the auxiliary circuit is important to any attachment that uses a hydraulic drive motor. “The key is just getting a little more flow because then you are turning that motor a little bit faster and that means more productivity,” says Kelly Moore, product manager, Gehl Co.
Work capacity is directly linked to flows and pressures in the hydraulic system. “Usually, higher flow and pressure will allow use of physically larger high-flow attachments, i.e., the ability to use a 30-in. cold planer attachment vs. a 24-in. unit,” says Bob Lessner, product manager for skid steers, Komatsu America Group.
High-flow attachments typically work with a range of different high-flow carriers. For example, an attachment may require a minimum of 30- up to a 40-gpm maximum. “Most high-flow attachments are designed to operate within a flow and pressure range because they may be installed on different prime movers from skid-steer loaders and backhoe-loaders to wheel loaders,” Lessner explains.
Calculate Hydraulic Horsepower
“The critical performance measure is hydraulic horsepower,” says Gary Ringenberg, commercial manager for skid loaders, Caterpillar. Available flow and pressure are the variables that determine hydraulic horsepower in the auxiliary circuit. “Hydraulic horsepower is calculated by multiplying the pressure in psi x the flow in gallons per minute and dividing by 1,714.”
This provides a good measure of auxiliary hydraulics productivity. “In order to get maximum attachment productivity, you need maximum attachment horsepower,” explains Rusty Schaefer, marketing manager, Case Construction.
But he cautions that auxiliary hydraulic horsepower must be matched with available horsepower in the base unit. “If you put a high-flow system on a unit that doesn’t have enough base horsepower, you are not really going to utilize it,” he states.
Moore also stresses the importance of matching engine power to the hydraulic pump. This results in unique flows for different size skid loaders. For example, Gehl’s two smaller-end high-flow units draw power from a 60-hp engine and pump out 30 gpm to the auxiliary circuit. The next two larger sizes in the lineup are powered by 82-hp turbo diesels. They produce 36 gpm at the auxiliary circuit. “Our largest machine is a 115-hp turbo. We are pushing 40 gpm on it,” says Moore.
Two Distinct Systems
High-flow skid steers utilize either open-center or closed-center, load-sensing hydraulic systems. Open-center systems use time-proven, durable gear pumps. “Open-center systems have been used for years, not only on skid steers, but on other pieces of construction machinery,” explains Moore. “They are a little lower cost, but very reliable.”
Moore adds that the closed-center system with a variable-volume pump is more energy efficient. “A true load-sense system uses a variable-volume pump to only move the amount of oil required,” he says. This saves fuel and engine horsepower while reducing heat in the hydraulic system.
Manufacturers must balance the cost and performance equation to determine which models most benefit from the open-center system vs. the closed-center, load-sensing system. Komatsu, for example, has chosen to use the closed-center system. “Komatsu’s system is closed-center and load-sensing so it allows for peak performance during maximum output,” says Lessner.
On its loaders offering 30- and 36-gpm high-flow auxiliary power, Gehl uses open-center hydraulic systems. “We have been able to get very good production out of these systems and better control the costs,” explains Moore. The large 115-hp loader with 40 gpm uses a closed-center load-sensing system. Moore claims the load-sensing system compliments this size machine very well.
Under Pressure
Some manufacturers even offer two different high-flow systems: one that has the same pressure as a standard system with increased flow, and one that offers both high pressure and high flow.
These high-pressure, high-flow systems increase productivity in the most demanding applications, such as with cold planer attachments. AAA Grinding and Trenching Inc., Ventura, CA, relies heavily on cold planer attachments to perform work in parking lots and around buildings. It uses cold planers with drums ranging from 24 in. down to 12 in. The company also uses rock saws to cut asphalt so excavators can easily open utility trenches across roads. “I can grind faster than a wet saw and I leave a 3-in. gap on both sides of the ditch where the excavator can just bail the thing out,” says Dee Willingham, owner.
Willingham has experience with high-pressure, high-flow systems. “I have the 5,000-psi, high-flow system. It is very important because pressure is horsepower,” he notes. The low-pressure, high-flow system will allow a cold planer to cut. “They just don’t cut as fast,” he adds.
Caterpillar and Case are two of the manufacturers that offer both systems. Caterpillar XPS skid loaders offer pressures to 4,067 psi. This results in significant hydraulic horsepower gains. “For example, the hydraulic horsepower on a Caterpillar 226B High Flow is 50.6 hp and the hydraulic horsepower on a 268B High Flow XPS is 78.3 hp,” says Ringenberg.
“Caterpillar has performed tests with different types of high-flow systems on different machines and with different work tools,” Ringenberg adds. “The results show that higher pressure gives greater performance and productivity.”
Case Corp. offers a 40-gpm, 3,000-psi high-flow system on its 75XT, 85XT, 90XT and 95XT. “Then we have the 5,000-psi system, which we offer on the 90XT and the 95XT,” says Schaefer.
This is a closed-center hydraulic system with a load-sensing pump. “It has its own piston pump to drive the attachment,” Schaefer explains. He claims this system can be 60% more productive than the 3,000-psi high-flow system. “The fact that it is a variable piston pump, which is more efficient than a gear system, that’s what makes the increase in productivity.”
The separate pump for the auxiliary circuit offers other advantages, as well. “It allows you to adjust your loader without affecting power to the attachment drive,” says Schaefer. “With other high-flow systems, when you move the loader, you affect flow to the attachment drive. That is real important when you are in high-performance applications with a planer, cutter, rock wheel or trencher.”
Caterpillar also uses a closed-center, load-sensing system on its XPS model skid steers. “The choice of open-center and closed-center hydraulic systems does impact the productivity of the hydraulic system,” says Ringenberg. “In a closed-center system, as fitted to the Cat 248B and Cat 268B High Flow XPS machines, the hydraulics can be tailored much more closely to engine performance than can be achieved with an open-center system. The result is a machine that gives more power at different engine speeds. This allows the high-flow hydraulic work tools to be operated up to peak engine torque without stalling the engine or generating excess heat,” explains Ringenberg.
Consider The Attachment
There are specific tools designed for high-flow and high-flow, high-pressure systems. “This is important as it gives the combination of the machine and work tool high productivity compared to a standard-flow work tool,” says Ringenberg. Never use standard work tools on a high-flow auxiliary. If an orbital motor is not designed for the flows and pressures, catastrophic failure can occur.
Likewise, make sure the flows and pressures available are up to the task. “Attachments must be matched to the prime mover or the hydraulic requirement of the attachment may be more than the prime mover can provide, resulting in poor performance,” says Lessner. “If you install an attachment that requires 30 gpm (minimum) at 3,000 psi on a prime mover that has a max output of 24 gpm at 3,000 psi, the end result is an under-performing attachment.”
But not all attachments benefit from a high-flow system. “I would estimate that 85% of the attachments in the industry today utilize standard-type flow,” says Moore. Only a small percentage of customers truly benefit from high-flow skid loaders and attachments. “Be cautious and investigate your needs,”Moore advises. “If you do not have a need for a high-performance attachment, you sure don’t have to invest more dollars for a high-flow-type skid loader.”
For customers who use attachments with orbital motors on a consistent basis, the choice of high-flow attachments and skid loaders is a little more clear. “You literally get jobs done faster with having more flow potential and high-flow type attachments will then prevail,” says Moore.
Some machines offer the flexibility to run both high-flow as well as standard attachments. “On a Gehl machine, for instance, if a customer invests in a high-flow model skid loader, he will run high flow from a set of couplers located on the right side of the machine. On the left side of the machine, he still has standard-flow couplers,” says Moore. “There are some machines in the marketplace that cannot do that.”
“The Caterpillar 248B High Flow XPS and the 268B High Flow XPS machines also have standard-flow hydraulics that can be used for work tools requiring standard flow,” adds Ringenberg.
By The Numbers
Increased purchase cost is the largest drawback to any high-flow system. Schaefer explains that it costs about 7% more to purchase a Case skid loader with the 3,000-psi, high-flow hydraulic system vs. the standard system. It is approximately 12% more than the standard skid loader to purchase the Case skid loader with the 5,000-psi high-flow hydraulic system.
“But you would get about 75% more performance or productivity going to the 3,000-psi high-flow system from the standard auxiliary,” says Schaefer. “With the 5,000-psi dedicated system, you would basically double your performance over the 3,000-psi high-flow system.”
Moore explains that you can spend in excess of $1,500 to upwards of $2,000 for the high-flow option on some loaders in the industry vs. a standard hydraulic system. “The larger the pump, the more cost there is involved,” he states.
Another consideration is the added versatility. “Some contractors have high flow on their machines just in case they may get a contract that requires the use of a high-flow work tool,” says Ringenberg. “They are then in a better position to win a contract.”