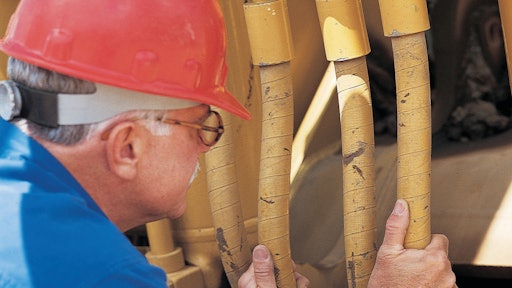
Hydraulic hoses are literally the lifelines of most construction equipment. Nothing can grind productivity to a halt faster than a ruptured hose. A little time invested up front to monitor the condition of the hydraulic hoses and fittings can dramatically reduce expensive failures in the field.
The potential cost of hose failure in terms of lost production, environmental impacts and possible injury to operators and others argues strongly in favor of replacing hoses on a time-based schedule, a periodic visual inspection, or some combination of the two. Hose replacement while equipment is already 'out of service' as part of a planned preventative maintenance schedule can prevent critical downtime and expense.
Hoses should be replaced as part of a preventative maintenance (PM) program, especially in critical applications. Hose self life is similar to automobile tires. After four to six years the rubber begins to break down and you can expect to see visual cracking and weeping around the couplings.
Begin with a through inspection. If there are no signs of leaking, abrasion wear, cracks or twisting, then there is no reason to proactively replace the hose assembly. However, other considerations including the remoteness of the jobsite or the cost of the machine being down may prompt some customers to replace hose assemblies at a scheduled overhaul.
Technology Predicts End of Life
In many (but not all) cases, there are indications of an impending failure. Wetness or leaks, cracked rubber, loss of flexibility or worn rubber are all signs of a potential problem. There is really no reliable way to tell how long a hose assembly will last once these symptoms are noticed.
That’s why it’s important to conduct a daily visual inspection before operating hydraulic equipment. But never conduct an inspection by running your hand over the hose while the system is pressurized. Hot hydraulic fluid can cause serious bodily harm, or even death if injected through the skin.
Until recently, however, there has been no practical way to detect those failure indicators and proactively replace hydraulic hose. Technology now exists to monitor those indicators and provide a warning of impeding failure. Eaton LifeSense hose delivers this capability. This can reduce the premature disposal of functioning hydraulic hoses
Gates also offers advanced hose monitoring technology known as Gates Sentry IQ. It monitors what goes on inside a working hydraulic hose. It measures pressure spikes and correlates them to the temperature inside the hose when the spike occurs. This correlation between the temperature and the pressure estimates the end-of-life for hydraulic hose assemblies.
Prevent Abrasion
It is generally excepted by that approximately 80% of hydraulic hose failures are caused by external damage, primarily abrasion. The most common cause of abrasion is hose assemblies rubbing on each other or surrounding surfaces.
Cover abrasion exposes the wire reinforcement to the environment. Sometimes the wire is also broken by the abrasion; and it may corrode from exposure to water and other environmental contaminants, thus weakening the hose.
In some cases external guarding can be used to reduce abrasion. Hydraulic sleeving or guarding is used primarily as additional protection against abrasion, erosion, snagging and cutting due to the environment, temperature and machine application. Replacement hose assemblies should include sleeving or guarding if the machine application requires it or the original assembly included it.
Another consideration is using an abrasion resistant hose, such as Caterpillar ToughGuard hose that is designed for severe abrasion applications.
Several types of hose guards or sleeves are available to protect hydraulic hoses from external damage and wear. They include metal spring guards, plastic spring guards and textile/nylon sleeving.
Metal spring guards help protect exposed hose from flexing, twisting, kinking, tensile or side loads, a tight bend radius and/or vibrations. This type of guard must be fitted to the hose during assembly.
Plastic spring guards or coil sleeves protect hose from exposure to water, air, gasoline and hydraulic fluids. They can be fitted after the hose is installed. Textile or nylon sleeving helps protect hoses from abrasion, either inside the equipment or in areas where hoses are likely to rub against one another.
But there is a downside to abrasion sleeving. Because the sleeve prevents easy visual inspection of the hose, it makes it more difficult to detect damage that may lead to a catastrphic failure. For this reason, a growning number of users are moving away for the use of abrasion sleeves.
Understand specifications
While many types of hose may look similar and even have the same physical dimensions, there are key differences that you must understand. “The important thing to remember is that the replacement hose must meet or exceed the specifications of the old or original hose assembly.
Equipment operators and technicians can reduce, if not eliminate, premature hydraulic hose failure by giving maximum consideration to hose assembly selection and installation. Yet, with all of the different types of hoses on the market, choosing the right one can be difficult. Gates suggests using the ‘STAMPED’ method to ensure you get the right hose assembly for the job. ‘STAMPED’ stands for Size, Temperature, Application, Material to be conveyed, Pressure, Ends or couplings, and Delivery.
Be wary of adapters that let you use a different size hose. Adapters allow field operators to change OEM hose with a different size or type that may not be appropriate for the OEM equipment. For example, to save money, or because a parts store doesn’t have the exact replacement hose in stock, an operator may replace a -12 hose (3/4-in. ID) with a -8 hose (1/2-in. ID), using an adapter to drop down a size.
Using the smaller size could increase the volumetric pressure inside the hose, generating heat, crimping the hose, or exerting excess pressure on the coupling – all of which could lead to premature hose failure.
Many users can be tempted by adapters due to hose availability. The biggest offender is -10 hose (5/8-in. ID), which is not prevalent in North America. Operators typically want to drop down to a -8 (1.2-in. hose ID) to save money. On a drive or control mechanism, doing so could cause the equipment to behave unpredictably.
You should also keep track of any trouble spots on the machine. If a particular hose fails or requires replacement more often than average for all the hose on that piece of equipment it may be prudent to upgrade to a stringer or more durable product.
It is particularly important to follow proper installation procedures as well as guidelines regarding minimum bend radius, twist and orientation, securement and storage. Most hose will carry either a generic SAE or ISO specification on the 'Layline' or a manufacturer's product designation. For example, a SAE EN856 Type R12 is a four-spiral high pressure hose specification which prescribes certain levels of performance on matter who manufacturers it.
All manufacturers provide cross references between generic designations and their proprietary product numbers. "However, in some cases a manufacturer will exceed the specification providing even higher levels of service and longer life.
Keep the system clean
Also keep in mind that today’s high performance hydraulic systems utilize extremely tight tolerances that can easily be damaged by even small amounts of contamination.
Before removing hose from equipment, spray it down with brake cleaner to remove all the oil, grease and debris. This will minimize the chance of dust, dirt or grime falling into the port when you remove the hose. Use a cap or plug to close the ports on the machine while you are servicing the hose or waiting for a replacement, to prevent dust or debris from being blown into the ports. If you have a replacement hose on hand you can forego capping the ports and simply install the new hose. Use brake cleaner to clean the threads and surfaces that the replacement hose will mate to in order to avoid introducing contaminants into the hydraulic system.
When a broken hose assembly is removed, the preferred method to keep contamination from entering the system is to install clean plastic or metal plugs and caps to cover all open hose ends, tube ends and related ports. Wrapping exposed hose ends, tube ends or related ports with clean plastic is also acceptable.
Don'y leave anything exposed longer than absolutely necessary. Any system port exposed to the atmosphere is a potential entry point for contaminants, so the duration of that exposure should be as short as possible.
New doesn’t mean the same as clean. In some instances the new hose can have debris left over from the manufacturing process. It is very important to clean new hose assemblies prior to installation. An un-cleaned hose assembly is an easy way to introduce contamination into the hydraulic system.”
To remove contaminants from a new hose assembly, Caterpillar recommends shooting a foam projectile through the hose and couplings using forced air. “This procedure is done twice, once in each direction though the hose assembly. After cleaning a hose assembly in this manner, the ends should be capped and plugged to further protect the assemblies from contaminants during transport and storage.
There are other ways to clean the hose as well. Cleaning methods vary based on shop capabilities, the cleanliness level required and the critical nature of the application. For hose going to a pumping component, cleanliness is absolutely critical; while for hose going to a tank or filter, cleanliness is less critical.
Three different methods are used to clean hydraulic hose assemblies with varying levels of cleanliness – shop air blow, pellet gun (projectile or ‘cleaning pig’) or fluid flush. The easiest and most commonly used cleaning method is to blow shop air through the hose assembly after the hose has been rough cut to the desired length. However, a shop air blow offers minimal cleaning and is the least effective method.
A better method is to use a pellet or ‘cleaning pig’, which is shot through the hose with compressed air. The pellet breaks up the debris and cuttings that accumulate up to 6 in. back from the hose openings after the hose has been cut, and flushes them out of the hose.
A fluid flushing apparatus provides the most effective cleaning method. “With this technique, cleaning fluid is flushed at a high velocity through the hose until the hose meets the strictest cleanliness levels. After cleaning, cap the assembly on both ends to protect debris from entering until the hose is installed.
Through daily inspections, a proactive preventitive maintenance program, proper selection and a concerted effort of cleanliness you can eliminate much of the downtime due to hydraulic hose failure.
This article was initially published in 2011 and was recently updated. Information was provided Caterpillar, Eaton and Gates.