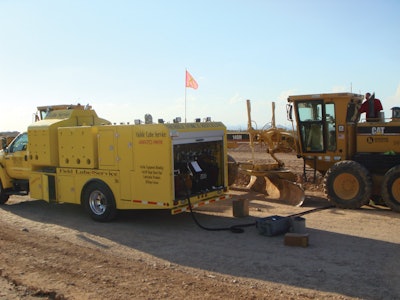
Water contamination is one of the chief enemies of any diesel-fueled equipment. All fuels contain some water in suspension, but unlike gasoline, diesel fuel is less refined and will hold a much larger amount. This water can cause severe problems with water separators on the equipment. It can also cause the fuel injector tips to explode, resulting in expensive repairs. In fact, slugs of water in the fuel can cause sudden cooling in the engine and may result in shortened engine life.
Diesel fuel can contain two types of water, water in solution or free water. “Diesel fuel can contain low levels of water that may be dissolved in the fuel, thus the term ‘water in solution’,” says David Harvey, manager of product and technology, Citgo. “These very low concentrations of water are reported in parts per million (ppm). There are various reasons that a diesel fuel may contain dissolved water. Among them are condensation of water in a fuel tank, components in the diesel fuel which help to retain the water in solution, and fuel temperature.”
But only low concentrations of water can remain as water in solution. “Water does not normally exist in a standard diesel fuel in high concentrations due to the significant differences in the chemical properties of diesel and water,” says Harvey. “The two liquids will typically separate, with water dropping out of the diesel fuel and accumulating at the bottom of a fuel tank.”
Water which is not in the diesel fuel as a dissolved component is considered ‘free water.’ “This would include water suspended in diesel as the result of agitation or water which is phase separated from the diesel fuel,” Harvey explains. “The most common cause of free water in diesel fuel is poor housekeeping of storage tanks. The most common cause of dissolved water is the composition of the fuel itself or additives which help to dissolve the water into a solution.”
Water in suspension in burning fuel reduces the amount of energy available and will result in lower horsepower output. Water in fuel tanks, lines, injectors, filters, etc., will freeze more readily than the fuel. Most fuels freeze at lower than -20°F. Water freezes at 32°F.
Read next: Tips for Monitoring and Maintaining Diesel Fuel Injection Systems
It is important to understand that low levels of water dissolved in the fuel are not necessarily a problem. “Diesel fuel containing low levels of dissolved water, in the ppm concentration range, will typically provide satisfactory service,” says Harvey. “However, free water in diesel fuel could result in excessive injector wear, filter plugging, power loss and corrosion of engine fuel system parts.”
You can often tell if there is a problem by a simple visual inspection, “If the fuel is hazy, or there is evidence of free water, then there is too much water in the fuel system,” says Harvey. “Hazy fuel would suggest that sufficient water is being retained in the fuel, typically by a co-solvent or additive, which is holding the water in suspension.”
Practice good housekeeping
Water becomes a problem during transport, storage and use. Newly refined fuel is clean and free of excessive moisture. Refiners and pipeline operators adhere to strict fuel storage tank maintenance procedures with regular removal of water bottoms and occasional chemical treatment to assure American Society for Testing and Materials (ASTM) specifications are met. Unfortunately, after it leaves these facilities water bottoms removal is often neglected.
Several factors contribute to moisture accumulation, including climate, storage tank installation and fuel handling procedures. Temperature changes can cause suspended water in the fuel to settle out. For instance, any time warm fuel is placed in a cooler tank, whether for storage or transport, moisture will drop out of the fuel as it cools. This makes it necessary to periodically drain off the water, which is a simple task. Water is more dense than fuel, so it always settles out to the bottom of the tanks.
Water condensation in diesel fuel storage tanks is a common problem. The longer the fuel is stored, the more pronounced the problem. If water is allowed to remain in the diesel while it is stored, microorganisms or bacteria can form that feed on the hydrocarbons in the fuel. This results in slime, which can clog filters.
“Good housekeeping practices are the most important means of minimizing water in diesel fuel systems,” says Harvey. “Such practices include periodic draining of water accumulated in fuel tanks, maintaining the seal integrity of fuel storage tanks, and allowing settling time of the fuel after a delivery into a storage tank (this affords water the opportunity to separate out from the diesel prior to distribution). You must also adhere to a maintenance program which includes eliminating or preventing microbial contamination of the tank contents.”
Read next: Diesel Fuel Housekeeping Cuts Construction Equipment Downtime
There is no set schedule for draining water from storage and equipment tanks. “Water should be drained from a fuel/water separator whenever free water is detected or visible in the system,” says Harvey. “Tank size does not necessarily influence the maintenance interval unless the fuel system is not properly sealed. Climate can have an impact.”
Above-ground tanks are more prone to significant daytime to nighttime temperature swings, which generates water. The fuel temperature drops at night, lowering the water solubility limit, and moisture drops out of the fuel. Unless the fuel is agitated, this water does not return to the fuel.
When the tank warms, humid air above the fuel cools and water condenses from the air. Underground tanks are often cooler than the air above ground. As fuel is dispensed, warm humid air takes its place. As the air cools, water condensation forms.
No matter what types of tanks are used, make sure they are properly sealed to prevent rainwater contamination.
Humid climates with temperature fluctuations require attention
“Areas of high humidity accompanied by low temperature would be expected to experience greater incidences of water accumulation from condensation,” says Harvey. “Diesel fuel can hold some water in solution, but as the ambient temperature decreases the water has a higher potential of separating from the diesel and accumulating in the bottom of the tank.”
Warm and humid climates can create problems with microbial growth.“Warmer temperatures tend to be more susceptible to microbial contamination with the subsequent water contamination of the fuel phase,” says Harvey.
Sometimes temperature fluctuations are cause by the operation of the equipment itself. While the equipment is operating during the day, warm air is drawn into the fuel tank. As the air above the fuel cools, water condenses. If the tank is left partially filled overnight, it is a prime candidate for moisture accumulation. Topping off the tanks at the end of the day gets rid of the humid, warm air in the tank and help prevent condensation.
What about the utilization of dessicant filters? “Utilizing desiccant filters could provide extra protection,” says Harvey. “In low humidity environments, such filters may be unnecessary. But under high humidity conditions, these filters would become saturated relatively quickly, resulting in increased operational expense. These filters perform no function if they are saturated and not promptly replaced. Conducting periodic checks for water in the fuel tanks, when performed properly, can eliminate the need for desiccant filters.”
Chemical treatment
There are chemical treatments available to help with the effects of moisture contamination. “Glycol ethers commonly used for diesel fuels are typically applied to suppress the freeze point of water which may be in a diesel system in order to prevent filter plugging from ice crystals,” says Harvey. “They are also applied to ‘dry out’ a fuel system. These chemicals, however, increase water contamination by attracting water into the diesel fuel, as dissolved water.”
In some cases there are drawbacks to glycol ethers. “The glycol ether holds the water in the fuel and thereby delivers more water to the fuel filter, injectors and combustion chamber,” says Harvey. “When properly applied, however, these chemicals can be a satisfactory part of a good housekeeping practice.”
You really need to understand the role of the additives. “Glycol ethers, used as directed, can help to minimize the effects of water in a diesel fuel system, but under the strictest definition of contamination, these chemicals actually contribute to water contamination of the fuel phase,” says Harvey. “Some common diesel fuel additives employ small concentrations of alcohol to reduce the freeze point of any water in the system, thereby helping to prevent ice crystal formation and the subsequent plugging of fuel filters.”
Read next: How Water Absorbers Prevent Water Damage to Fuel Systems
Monitor biodiesel blends
Biodiesel blends are becoming more common than in the past. But depending upon the type of blend used, you may want to closely monitor the fuel for moisture contamination,
“Depending upon the source of the biodiesel, blends can be more susceptible to water contamination,” says Harvey. “Biodiesel blends up to 5 volume percent are considered to be normal diesel fuel as defined by ASTM D-975, the standard specification for diesel fuel oils. Anything above 5 volume percent may require additional oversight and maintenance to keep the fuel system free of water.”
But no matter if you are use standard No.2 diesel of biodiesel blends, there is no substitute for good housekeeping practices. Water contamination is easily monitored, and if corrective actions are taken in a timely manner there is no reason for the resulting equipment damage or associated downtime.
This article was first published in 2012 and updated in 2020.