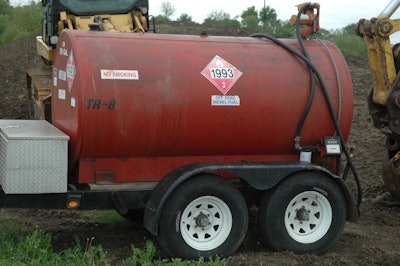
The cleanliness of the diesel fuel in your equipment has a major impact on uptime, especially with the advent of Tier 4-compliant engines that rely on high-pressure common rail fuel injection systems. Because these engines work at higher fuel pressures and have smaller injector openings, even the smallest amount of water or particulate can prove problematic.
The stringent cleanliness requirements place a greater demand on fuel filters. Even small pieces of dirt or dust that don’t get filtered out of the fuel can get stuck in the openings of injectors, causing decreased engine performance or system malfunctions. Consequently, filters must now prevent sub-visible particulate from entering the engine. Particulate in the 1- to 5-micron range must be removed, whereas 20 years ago, particulate removal was in the 50-micron range. (The human eye can see 40 microns and above.)
Newly refined fuel is normally clean and free of excessive moisture. Refiners and pipeline operators adhere to strict fuel storage tank maintenance procedures with regular removal of water bottoms and occasional chemical treatment to ensure ASTM specifications are met. Unfortunately, once fuel leaves these facilities, contamination can occur during transport, storage and use.
Why Water is Enemy No. 1
Water in diesel fuel is the most common source of problems. With engine injection pressures reaching 15,000 psi and above, removing water from fuel is essential to maintaining performance. While just 20 years ago engines were able to burn water that entered the fuel system, now even the smallest amount of water can cause an injector tip to blow and the engine to need overhauling.
Water Contamination Wreaks Havoc on Diesel Fuel Systems
Diesel fuel is capable of holding some water in solution. But as the ambient temperature decreases, the water has a higher potential of separating from the diesel and accumulating in the bottom of the fuel tank. Water in diesel fuel that is not a dissolved component is considered “free water.” The most common cause of free water is poor housekeeping of storage tanks. The most common cause of dissolved water is the composition of the fuel itself, or additives that help to dissolve the water into a solution.
Water in suspension in burning fuel reduces the amount of energy available and may result in lower horsepower output. Water in fuel tanks, lines, injectors, filters, etc., will freeze more readily than fuel. Most fuel freezes at less than -20° F; water freezes at 32° F. Note that the cloud point of diesel is around 10° F to 15° F. The pour point is typically around 0° F.
Low levels of water dissolved in the fuel are not necessarily a problem. However, free water in diesel fuel could result in excessive injector wear, filter plugging, power loss and corrosion of engine fuel system parts. You can often tell if there is a problem by a simple visual inspection. If the fuel is hazy, or there is evidence of free water, then there is too much water in the fuel system.
To remove water from fuel, many filter manufacturers will use an absorbent technology to literally absorb the water. Once the absorbent can no longer absorb and hold water, the filter must be replaced.
Factors Contributing to Water Contamination
Several factors can contribute to moisture accumulation in diesel fuel, including climate, storage tank installation and fuel handling procedures. Temperature changes can cause suspended water in the fuel to settle out. And areas with high humidity accompanied by low temperatures would be expected to experience greater incidences of water accumulation from condensation.
For instance, any time warm fuel is placed in a cooler tank, whether for storage or transport, suspended water or moisture will drop out of the fuel as it cools. This makes it necessary to periodically drain off the water, which is a simple task. Since water is denser than fuel, it always settles out to the bottom of the tank.
The longer fuel is stored, the more pronounced the water condensation problem becomes. If water is allowed to remain in the diesel, microorganisms or bacteria can form that feed on the hydrocarbons in the fuel. This results in slime, which can clog filters, cause a foul odor and result in discoloration of the fuel.
Above-ground tanks are more prone to significant daytime to nighttime temperature swings, which generate water. The fuel temperature drops at night, lowering the water solubility limit, and moisture drops out of the fuel. Unless the fuel is agitated, this water does not return to the fuel.
In onboard fuel tanks, temperature fluctuations are sometimes caused by the operation of the equipment. As equipment is used throughout the day, warm air is drawn into the tank. As the air above the fuel cools, water condenses. If the tank is left partially filled overnight, it is a prime candidate for moisture accumulation. Topping off the tanks at the end of the day gets rid of the humid, warm air in the tank and helps prevent condensation. Some good housekeeping practices include periodic draining of water accumulated in fuel tanks, maintaining the seal integrity of fuel storage tanks and allowing settling time for the fuel after a delivery into a storage tank. This affords water the opportunity to separate out from the diesel prior to distribution. Regardless of tank type or size, make sure it is properly sealed to prevent rainwater contamination.
There is no set schedule for draining water from storage and equipment tanks. Water should be drained from a fuel/water separator whenever free water is detected or visible in the system. Tank size does not necessarily influence the maintenance interval unless the fuel system is not properly sealed.
You should also adhere to a maintenance program that includes eliminating or preventing microbial contamination of the tank contents. Like mold on bread, algae and fungi can thrive inside fuel tanks, particularly in warm, humid climates. These microbes require both fuel and water, so the drier the fuel, the smaller your algae problem is likely to be. Since keeping all water out of the fuel is improbable, diesel fuel should always be treated with a biocide to prevent the growth of microbes.
Take Care with Additives
Other chemical treatments are available to help with the effects of moisture contamination. For example, glycol ethers commonly used in diesel fuels are typically applied to suppress the freeze point of water in the fuel system in order to prevent filter plugging from ice crystals. They are also applied to “dry out” a fuel system.
However, it’s important to understand the role of such additives. Used as directed, glycol ethers can help to minimize the effects of water in diesel fuel. But under the strictest definition of contamination, these chemicals actually contribute to water contamination of the fuel phase by attracting water into the fuel as dissolved water. As a result, they deliver more water to the fuel filter, injectors and combustion chamber. Yet, when properly applied, these chemicals can be a satisfactory part of good housekeeping practices.
Other common diesel fuel additives employ small concentrations of alcohol to reduce the freeze point of any water in the system. Since alcohol tends to attack O-rings and other rubber parts in the fuel system, it should be avoided.
Fuel Cleanliness
Fuel cleanliness has always been an essential part of maintaining the performance, reliability and usable life of all diesel engines. International Standard Organization (ISO) cleanliness codes are used to determine the cleanliness level.
Diesel Fuel Housekeeping Cuts Construction Equipment Downtime
The ISO cleanliness codes are derived from ISO 4406:99, which states particles per 1 mL. The codes show three sets of separated numbers, which refer to ranges depicting the number of particles present in fuel that are larger than 4, 6 and 14 micron, respectively. As 6-micron and 14-micron particles are both larger than 4 micron, those particle sizes are also present in the first number. The second number only shows particles larger than 6 micron, while the last number only shows particles larger than 14 micron.
In the past, a cleanliness of ISO 18/16/13 has been specified by the fuel injection equipment manufacturers, which means no more than 1,300 to 2,500 particles greater than 4 micron can be present in the fuel. This level of cleanliness requires careful fuel handling practices. Make sure all storage, transfer and equipment tanks are clean and fitted with the appropriate filters.
New engines required advancements in fuel system technology as well as in the quality and cleanliness of the fuels that the engines burn. Fuel for Tier 4 engines has to be 100 times cleaner than that used in Tier 3 engines. Where Tier 3 diesel engines can operate with fuel containing between 1,300 and 2,500 particles greater than 4 microns, Tier 4 engines can only have between 20 and 40 particles greater than 4 microns. The cleaner the fuel, the more efficiently it will burn in these engines.
Consequently, an important consideration in your housekeeping practices is to clean diesel fuel with fine filtration prior to being dispensed into your equipment.