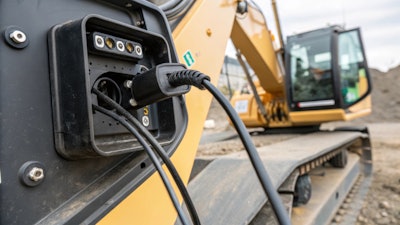
The more industries lean into electrification, the more a profound realization sinks in – the battery is only the tip of the iceberg.
This realization is critical for Original Equipment Manufacturers (OEMs) in industrial sectors. While battery choice is certainly important, the selection of accompanying components that interact and integrate with it is equally crucial. Among these components, chargers often don’t receive the attention they deserve. Yet, they hold a significant impact on the effectiveness of electrification.
Here are six ways charging technology continues to advance equipment electrification, as well as strategic industry insights for OEMs to optimize these technologies for maximum benefit.
1. Enabling Greater Integration
For decades, a charger’s purpose was relatively singular: recharge the battery. This one-dimensional relationship meant components often operated in isolation, leading to inefficiencies.
In contrast, modern chargers are integral to more intelligent, connected machinery. Advanced charging solutions open up new design options for OEMs:
- Partial integration enables active communication between the charger and Battery Management System (BMS). This unlocks efficiencies through ‘smart charging’, where two-way data feeds optimize the charging process.
- Full integration takes this a step further, creating an intelligent ecosystem where all components and even external systems work together in real-time. A fully integrated system enables additional conveniences, such as DC fast charging and data-gathering telematics.
Armed with intelligent charging technology, OEMs can passively improve overall efficiency while actively leveraging valuable data to enhance future operations.
2. Increasing Battery Lifespan
Before delving further into charging technology, it’s important to establish that successful electrification hinges on viewing both the charger and the battery as a cohesive unit.
The simple act of swapping from internal combustion engines (ICE) to electric drivetrains improves total cost of ownership due to reduced maintenance. This makes sense given the mechanical differences: ICE produces noisy, explosive combustion and sizzling oil, whereas electric drivetrains hum quietly along with zero emissions. Electric drivetrains are also more efficient — boasting 90% or more efficiency versus ICE’s average of 35% to 40%.
Given these advantages, why isn’t electrified machinery the go-to choice? One major reason is the higher initial cost, much of which is concentrated in the battery.
This is where the charger circles back into the picture. A 2024 study shows that a charger optimized with intelligent algorithms slows battery degradation and prolongs lifespan, further reducing the total cost of ownership. These benefits only compound in demanding industrial applications.
Chargers thus continue to drive electrification by maximizing returns on battery investments.
3. Tailoring Machinery to the Application
While off-the-shelf components are always preferable, custom-built chargers pave the way for machinery tailored to the application. This approach allows for more precise integration, optimizing the machine's overall performance and efficiency.
Specifically, this could include:
- Calibrated charging profiles – Specific charging profiles designed to match the unique duty cycles of different machinery ensure that equipment is charged for maximum battery life and efficiency based on its usage patterns. For instance, chargers for heavy-duty excavators have different profiles compared to a warehouse forklift, reflecting the distinct operational demands and environments.
- DC-DC adapters – This integration is crucial when auxiliary functions separate from the machinery’s primary operations are needed. These adapters convert the battery's DC output into the precise voltages and currents required for additional components, such as lighting systems, sensors, or communication devices.
- DC-AC inverters – These connections convert DC power from the battery into AC power—necessary for machinery requiring higher power inputs, or for operating AC-powered tools and systems. This is particularly useful in applications where the machinery must provide its own power supply, such as mobile construction equipment or field service vehicles that use various electric tools.
These are only a few examples of the possibilities an advanced charging solution enables. Much more than a mere medium for electricity, a purpose-built charger facilitates safe and efficient power transfer at multiple levels across the system.
4. Elevating Efficiency
While this benefit may seem obvious, the massive boost in efficiency that chargers offer is worth reiterating. Where electric drivetrains already boast impressively efficient energy use, intelligent chargers elevate this even further. In fact, research highlights that algorithmic chargers can achieve up to 46.3% greater efficiency compared to traditional, non-optimized chargers.
Advanced chargers also support features like regenerative braking, which captures and repurposes energy that would typically be lost during deceleration. This energy is then reused, effectively increasing the overall power efficiency of the machinery.
5. Enhancing Operational Flexibility
Particularly as we see an increase in standardization and electrical infrastructure, charging technology is driving electrification by offering unparalleled options for the next generation of off-road industrial machinery.
Consider just a few examples:
- Onboard chargers are integrated directly into the machinery, allowing battery charging wherever equipment can be connected to the electrical grid. This translates to added convenience and reduced downtime since equipment can be charged during off-hours at the job site, eliminating the need for transport to a separate charging facility.
- Offboard chargers are external systems that offer higher power and a faster charge versus onboard systems. These are particularly useful when machinery needs rapid top-ups between uses (opportunity charging) for longer shifts. Offboard systems can accommodate multiple machines or provide quick-swap capabilities for batteries, reducing charging time.
- Wireless chargers eliminate physical connections, reducing wear and tear. The technology works by parking machinery over inductive charging pads, allowing for automatic and effortless charging. Wireless setups are advantageous in harsh environments where exposure to elements can damage physical connectors. They also benefit OEMs utilizing Automated Guided Vehicles (AGVs) and Autonomous Mobile Robots (AMRs) by eliminating the need for a manual plugin.
- Modular charging systems consist of scalable charging modules that can be customized to meet specific power needs and expanded as requirements grow. This flexibility is crucial for fleets of varying sizes and machinery types, enabling a tailored approach to charging infrastructure that can adapt to changes in the operational scope or the addition of new equipment.
With these versatile options, modern charging technologies support industrial machinery electrification, improving operational efficiency, sustainability, and flexibility.
6. Improving Safety
Smart chargers enhance operator safety at every level. Take thermal management, for example. While useful for optimizing charger efficiency across various temperatures, this technology primarily ensures both battery and charging systems perform their operations safely and without overheating.
Intelligent charging systems thus play a critical role in supporting the overall safety framework of electrified machinery. These systems are designed to power and manage auxiliary safety mechanisms such as:
- Emergency stop features – Intelligent chargers can ensure that emergency stop features are always powered and ready to function, providing a critical safety measure.
- Automated diagnostic tools – These tools continuously monitor battery health and performance, providing early warnings for potential issues before they lead to failures or safety hazards.
These intelligent features work both to prevent physical accidents and ensure that equipment functions within safe operational parameters, mitigating risks and extending the machinery’s lifecycle. As the industry continues to adopt electrified solutions and the machinery itself becomes more interconnected, this proactive approach to safety is increasingly necessary.
Charging Technology: Driving a Sustainable Future
As electrification continues to shape our industrial landscape, advancements in charging are catalyzing this transformation. But technology alone is not the end of this journey; it is merely a foundational step.
Beyond batteries and chargers, the true catalysts propelling us toward an all-electric future are industry knowledge and insights. By harnessing this expertise, OEMs can tailor components precisely to their applications, integrate batteries and chargers as part of a unified system, and fully utilize the diverse array of charging solutions available.
This strategic approach places OEMs at the forefront, leading the charge toward a more electrified, efficient, and sustainable future in heavy industry.