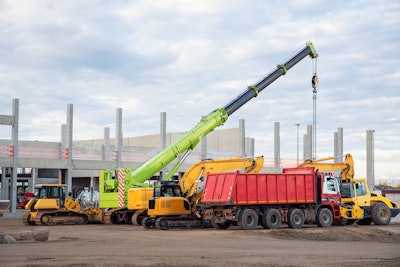
Managing a mixed fleet in today’s construction industry means more than just keeping vehicles on the road and heavy equipment in the dirt: it’s about keeping teams focused and entire projects on track. Between increasing equipment costs, complex maintenance schedules, unpredictable downtime, and the growing pressure to do more with less, 46% of fleet leaders are managing more than 10 siloed software tools across telematics, fuel tracking, inspections and safety to run their daily operations. When these systems don’t integrate with each other, it creates unnecessary downtime, duplicated data entry, missed alerts and costly delays. It’s no surprise that integrations, automating and consolidating data across multiple business systems, are quickly becoming a must-have for fleets that want to improve productivity and control costs on and off the jobsite.
Understanding the Need for Integrated Software Solutions
Construction fleets rely on various tools to track fuel usage, maintenance records, operator safety, and asset health, but when those systems aren’t integrated, teams are forced to piece together data manually. This fragmented approach makes it difficult to know the real-time status of equipment, ensure assets are maintained and job-ready, and accurately track operating costs across projects. Software integrations solve this by automatically consolidating data from multiple platforms into a centralized system of record. This reduces manual entry, minimizes errors, and gives fleet managers immediate visibility into the performance of every asset across jobs — from pickup trucks to yellow iron. With 79% of integrated platform users reporting time savings, the impact on planning, budgeting, and jobsite readiness is clear. This demand for adaptable integration-first solutions is not new but is especially key given the labor shortage in the construction industry. These shortages can be attributed to a lack of skilled workers, workplace safety concerns, and an aging workforce, among other factors. Many construction organizations have begun to leverage digital tools and AI to increase their capacity and capabilities, looking to offset these labor shortages. As reliance on technology continues to grow, solutions that lack interoperability and fail to integrate advanced technologies will start falling behind. Fleet management solutions should serve as an addition to a fleet team instead of adding to the growing list of monotonous management responsibilities.
Siloed Systems Expose Construction Fleets to Operational Risks
Just as assigning the appropriate equipment to the right project is critical, managing daily fleet operations often requires multiple tools, each serving a distinct but essential role, from ensuring asset and personnel safety to tracking maintenance and monitoring compliance. However, a lack of connectivity between these tools can lead to data misalignment through duplication and errors, and a loss of productivity when time is spent figuring out how to navigate multiple platforms. For example, a construction fleet manager may struggle with unexpected equipment breakdowns because their maintenance records, defects, and telematics data are spread across multiple systems, requiring additional time and resources from the fleet to handle and coordinate service efficiently. Increased downtime, which can cost fleets up to $760 per piece of equipment per day, can result from these inefficiencies in maintenance management, impacting service and cost-effectiveness. When construction teams lose productivity, it’s not just time that’s wasted, it’s money and project momentum. Relying on too many disconnected systems adds unnecessary administrative work and pulls focus away from what really matters: keeping equipment running, teams working, budgets in check, and jobs on schedule. Integrated solutions cut through that noise by bringing everything into one place, making it easier to track equipment status, catch issues early, and reduce downtime. Rather than juggling in between disparate platforms, teams can spend more time keeping projects moving and less time chasing information. It’s a smarter way to manage your fleet and protect your bottom line.
Modern Fleet Optimization Platforms Prioritize Streamlined Integrations
Whether due to the economy, changes in supply chain, or shifts in the labor market, construction fleet operations are becoming more complex and require insights and information from advanced tools to boost profitability. Optimization platforms, for example, are integrated fleet management systems that bring together critical data sources such as telematics, fuel, inspections and maintenance into a single, centralized platform, giving fleets a unified source of truth for all operational insights and reporting. If a construction fleet manages multiple projects across a city, the single platform can easily monitor each asset's location, maintenance status, and fuel usage. With an optimization platform, fleets can consolidate equipment diagnostics, location, maintenance history, fuel usage and operating costs to make decisions on how equipment should be used and gain the oversight they need to set their teams up in advance.
When this information is spread across disconnected systems however, it’s easy to miss early signs of wear or overlook overdue maintenance, increasing the risk of equipment failure and downtime on the jobsite. By centralizing data in a single platform, fleets gain the ability to see the full picture, connecting inspection results, utilization patterns and service history in real time. This visibility allows organizations to automate service schedules, catch inspection failures early, and proactively address critical repairs before they become costly problems. With all equipment insights in one place, teams can act quickly, stay compliant, and keep projects on track with fewer disruptions. Integrated platforms give construction leaders real-time visibility into their equipment and operations, helping them spot issues before they cause costly delays. Fleet and equipment managers are responsible for tracking equipment data like fault codes and health alerts that can signal potential failures. Without real-time integrations to sync this data, early warning signs often go unnoticed until it’s too late.
Shifting Gears Toward Connection in Construction Fleets
Organizations that choose integrated solutions gain more than convenience. An integrated system doesn’t just log maintenance history — it triggers automated service alerts, ensuring a critical piece of equipment doesn’t go offline in the middle of a project. These solutions unlock streamlined workflows, stronger data-driven decisions and faster platform adoption across teams. Integrations eliminate time-consuming manual entry, reduce errors, and drive long-term efficiency. But to truly future-proof operations, construction fleets need more than basic compatibility. They need purpose-built tools that work together seamlessly.
Construction executives should look for platforms that offer must-have integrations such as OEM telematics, on-site fuel tracking and maintenance scheduling. These capabilities directly impact jobsite productivity by minimizing equipment downtime, reducing fuel waste, and ensuring on-highway and off-highway assets are always ready to work. By adopting a fully integrated fleet management platform, construction teams can stay focused on their projects, not paperwork. The right solution should support your operations, adapt to your workflows, and act as a partner in achieving your performance goals.