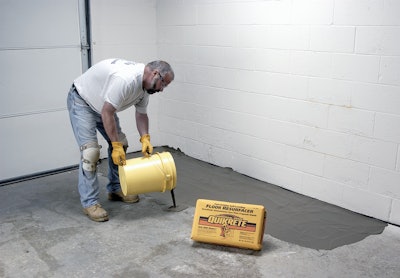
The customer asks you what to do. “Should I replace my concrete drive or can it be repaired and saved? My garage floor is severely pitted from salt damage and water. Can it once again be made to look new without having to dig out and replace the old floor? Or my parking lot has several prominent cracks. Can they be repaired and made to look aesthetically appealing or does the entire parking lot need to be replaced?"
Depending on the project in question and a few variables, the answer, unfortunately, to these questions is often subjective.
New mindset
“Ten years ago, replacing damaged concrete was often the preferred solution to repair,” relates ARDEX Engineered Concrete Repair Systems Field Specialist Dennis Layne. “The ensuing decade, however, changed that. Economic realities made less-expensive repair options more attractive, as has the push for a more sustainable, greener building environment. Being able to repair existing concrete instead of removal and replacement, seriously reduces the carbon footprint.”
He emphasizes that technology has kept pace, allowing repair products to be faster drying, stronger and more durable than their predecessors. “Contractors are becoming more savvy about these products and can offer repair solutions that might otherwise have been overlooked.”
Still, Layne says it comes down to the extent of damage and whether to repair or replace has to be determined case-by-case. His counterpart on the east coast, Chuck Knight, agrees. “First, ask yourself if you can restore it to its original integrity. Consider how deteriorated the concrete actually is. Is there spalling, which refers to exposed aggregate on a concrete structure? If so, the concrete will likely have to be replaced. Is the damage caused by poor installation? Again, if the answer is yes, replacement is the best option. If it’s merely a worn or chipped surface, commonly referred to as delamination, then repair is a viable option.”
Concrete will eventually wear out, adds Layne. “Over time, the elements will cause the concrete to break down. In the north, especially, where there is wide temperature swings, cracking is more commonplace than in the southwest. Pitting caused by salt is also prevalent in northern climates.”
The question is how much spalling is there? How much chipping is there? Is there a structural break? How much material is missing? If it’s too much, then the concrete will need to be replaced; repair would not be an option.
Matter of degrees
“A rule of thumb is if the repair requires more than two inches of material, then it would probably pay off to replace the concrete,” explains Joe Rizzo, Regional Manager for Oldcastle’s construction products division. “If it is less than that, there are a number of products on the market that can restore both the concrete’s structural integrity and aesthetic appeal.”
He continues, “but deterioration or extent of damage may not be the only criterion for making a decision. Clearance can be an issue if the repair involves pouring a layer of cement over the existing concrete. Time can be another consideration. How long can the structure be out of commission? Then there are aesthetics to consider, as well.”
Again, he notes that new products on the market can be real problem solvers. “New materials can be placed to a feather’s edge or be used to fill in pitted and spalled areas, and in both cases be ready to walk on within a matter of hours. Aesthetically speaking, new repair materials can be stenciled and stamped to incorporate a wide variety of designs, ultimately making a repair project look like a new pour. The repair material can be structural, as well. A load-bearing driveway, for example, can be repaired with cement-based material rated up to 10,000 psi.”
Base concerns
Concrete can deteriorate for any number of reasons. Poor installation is a common culprit, with not enough attention paid to the sub base, matching the application to the cement product, or the location of expansion joints. Concrete expands in the heat and contracts in the cold. If the expansion joints are not spaced properly, the stress caused by the expansion and contraction will result in cracking.
There are occasions, then, when repair definitely isn’t an option. “If the subbase is eroded, then the concrete section will have to be cut out and a new subbase put in and compacted,” relates Frank Owens, Quikrete vice president of marketing. “Large cracks are problematic, too, especially those that extend all the way through to eventually erode the subbase. They will let in water and the freezing and thawing cycles will ultimately find the weak points in the concrete and create further deterioration.”
Owens notes that if subbase isn’t an issue, then the decision to repair or replace may come down to expense. “It costs from $3.50 to $5.50 per square foot to replace concrete. However, leaving the old concrete in place and applying a concrete resurfacer with a squeegee reduces the costs substantially. Material cost for the resurfacer would be about $.25 per square foot. Depending on the extent of surface scaling, the only surface preparation would entail pressure washing.”
Interior, too
It’s not just exterior surfaces that deteriorate over time. Interior floors can become uneven from settling or just plain wear and tear and replacing them can be more costly than replacing exterior surfaces.
For repairing uneven or worn interior concrete floors, contractors can use a self-leveling floor resurfacer. Owens notes that such products are effective at raising low areas that are up to 1 ½ inches deep. He explains its application: “Start with a good clean slab, apply a bonding adhesive, and allow it to dry. Pour the resurfacer in 1-foot strips. It then will melt together raising the low areas. Our fast-set self-leveling resurfacer will dry within two to four hours compared to 24 hours for its normal set counterpart. Both should be allowed to cure seven days before installing tile or carpet.”
Owens says the product can be used outside if the environment is controlled to protect the floor from wind, excessive heat and other natural elements.
Many of the same products used to repair horizontal surface can also be effective with vertical surfaces, such as exterior retaining walls and interior load-bearing walls.
“Replacing some basic vertical surfaces, especially load-bearing walls, can become very expensive,” says Rizzo. “Coatings that improve aesthetics and also give durability to the surface become a real time and money saver for the property owner.”
There’s no question that contractors can offer customers more repair options than ever before. Although the makeup of concrete hasn’t changed dramatically over the last 20 or so years, repair products have. Polymers help create a strong bond between new and old concrete, acrylics add strength, and attractive finishes disguise patching and other repairs. Concrete surfaces can not only be filled in, leveled, livened up and strengthened without expending the time and money to replace old concrete, surface treatment can actually make them look as good if not better than new.
Yes, as the above manufacturers point out, there are occasions when replacement is the only option. Short of that, when time, money, aesthetics and sustainability are priorities, repair becomes a very attractive alternative.