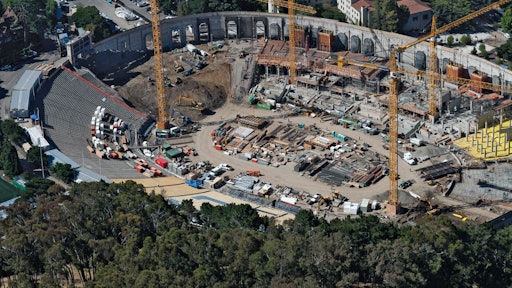
Webcor Concrete is a division of San Francisco-based general contractor Webcor Builders. The GC business started in 1971, always self-performing its concrete work on projects throughout its growth. In 2000, Webcor Builders recognized its strength in structural concrete work and saw opportunities to expand the company by offering concrete services to other GCs. Webcor Concrete landed its first job as a concrete subcontractor in 2001.
The concrete division
For much of the 2000s, Webcor Concrete specialized in residential and commercial high rise construction. It averaged between 80 and 90 percent of its annual sales with its parent company, bidding the remainder of its projects with about 15 different GCs in the San Francisco area. Its management team includes Chris Plue, Greg Lafayette and Jitendra Pahilajani.
Being part of a general contracting firm allows Webcor Concrete to offer several advantages to outside GCs it works for. Len Vetrone says one is its understanding of construction beyond concrete. “A lot of concrete subs don’t have the same level of appreciation of the downstream impact tolerance conflicts can have on other trades,” he says. “We can add value for a GC or builder/developer when we can assist on these issues in preconstruction meetings.”
Value engineering is another area where Webcor Concrete excels. “When GCs allow us to share our experiences on what works and what doesn’t work on projects, they will see the results reflected in the schedule, price, safety and final quality of the project,” Lafayette adds.
Pahilajani says the top reasons why other GCs hire Webcor Concrete is they are price competitive and can deliver a fast construction scheduled. “We brought the 3-day cycle on high rise residential to this market,” he explains.
“First and foremost, we want to work on Webcor Builders projects. They are our No. 1 client and those projects are where we are most profitable,” Lafayette adds. “But the way Jit, Chris and I approach business is Webcor Concrete needs to survive with our without Webcor Builders. That’s what makes us competitive.”
In October 2008, Webcor Concrete found itself at a turning point. With the high rise market bottoming out, the company did two things to keep jobs coming in -- it pursued other building markets and diversified geographically.
Webcor Builders opened offices in Seattle, Southern California and Guam. It also hired Vetrone, who had prior experience bidding public jobs. Utilizing the experience from within the concrete division and Webcor Builders, Webcor Concrete landed jobs building hospitals, public works buildings and military structures.
The changes in the economy also affected Webcor Concrete’s client mix. While before 2008 it was doing the majority of its work for its parent company, during the downswing it took on the majority of its projects for outside GCs. Just recently, as the market has begun to pick up again in the San Francisco area, Webcor Concrete is again seeing a transition back to working most of its projects for Webcor Builders.
Its diversification beyond the high rise market opened up opportunities for future growth as the construction market cycles upward again. With experience building a broader range of projects, Webcor Concretes expects to surpass its peak sales of $186 million in just a few years.
Green strides
Webcor Concrete’s focus on sustainable construction stems from its parent company’s commitment to the process. Phil Williams is a vice president at Webcor Builders and leads the company’s Sustainability Group. After Webcor Builder’s first LEED project in 2005, the company dedicated itself to sustainable building practices, at the corporate level and in the field.
Today, 98.6% of the company’s revenue stems from LEED projects. Webcor Builders utilizes BIM on every job, offers complimentary LEED paperwork processing for clients, and strives to reduce waste through an integrated engineering approach that eliminates premium pricing for sustainable construction. The company views sustainable building as a standard, like safety, and requires everyone on each job, subs included, to pass both an online safety test and an online sustainability test.
Williams explains the decision to go green was rooted in more than environmentalism – it was the standard the commercial real estate market was trending toward. In an effort to remain competitive, Webcor Builders embraced sustainability completely and worked to make it one of the company’s core values. The company is even supporting the message beyond its own walls by working to develop sustainability standards on the city and state levels.
Webcor Concrete started adopting sustainable concrete practices as its parent company got more involved in green construction. Webcor Concrete was a pioneer in the San Francisco area in pushing cement replacement percentages in concrete, regularly using 20 to 30 percent fly ash or slag mixes as early as 2005.
Another area where Webcor Concrete focuses on sustainability is in reducing the amount of lumber waste. After a project, all plywood and dimensional lumber is returned to a central lumber yard and inventoried. Before they place a lumber order for a new project they check the central yard to find out what they can reuse before ordering new. The company is in the process of taking this a step further.
“We are working on a metric that measures the amount of lumber used and reused on a project. We can eventually assign a number to a project based on the amount of lumber that went into and came out of a job. This will allow us to track jobs so we can work to reduce lumber use on all projects,” Pahilajani says.
Virtual building and the use of BIM (building information modeling) is another aspect of the company’s sustainable building practices, allowing them to engineer forming systems and other elements of the job to minimize waste. They also strive to value engineer projects to reduce the overall amount of concrete used on a project. Lafayette says just by reducing an 8-inch deck thickness to 7-1/2 inches they can save on weight, ready mix and rebar. “Tracking green points is important, but it also makes us a more profitable company. The driver is it reduces the cost of a job by minimizing waste,” he explains.
Sustainable jobs
Two recent projects exemplify Webcor Concrete’s mission to further sustainable building practices and how concrete’s green aspects are helping it gain market share over competing building methods like steel construction.
The company is just finishing work on the San Francisco Public Utilities Commission headquarters, a project seeking LEED Platinum certification. The building will use 32 percent less energy, use 60 percent less water and will have a 50 percent smaller carbon footprint than similarly sized buildings.
Webcor Concrete was hired as the concrete sub to Webcor Builders. The public bid project sought a design that would remain functional after a large seismic event so the city could run fire and other disaster services out of the location. The owner also desired a building that could achieve LEED Platinum status and have a 100-year lifespan. Webcor Builders and Webcor Concrete achieved this for not a dollar more or a day longer than other construction methods.
Webcor Concrete used 70 percent cement replacement mixes in the foundations along with smaller cement replacement where strength gain was a factor. The project attained 50 percent cement replacement overall. Concrete’s long-term durability contributed to the 100-year lifespan. And the use of vertical post-tension in the concrete core walls will allow for the flexibility necessary in the case of a severe seismic event. The building is an example of what can be attained with concrete as a construction material and where the standard for sustainable concrete construction is headed.
The reconstruction of the University of California - Berkeley’s Memorial Stadium, home of the Golden Bears, is another example of concrete’s capabilities as a construction material. The stadium was originally constructed of concrete in the 1930s. It sits on an active fault line, running almost directly through the stadium from one end zone to the other.
The owner wanted the new stadium rebuilt in concrete, but the consulting engineers said it was impossible in the time frame the owner wanted and that it would need to be built with steel. Webcor Builders won the bid as the GC, then asked Webcor Concrete to value engineer a design that utilized concrete construction in the necessary time frame. The owner approved the all-concrete design, the bid went out for the new plans and Webcor Concrete won the concrete sub work.
The new stadium retains the original 1930s concrete façade, preserving the historic look of the stadium. The internal structure integrates modern seismic design utilizing cast in place concrete throughout the walls, columns and seating risers; large hydraulic shocks that will allow the building to move during an earthquake; and a flexible strip that runs along the fault line that allows the earth to shift independently of the surrounding structure.
On both these projects, Webcor Concrete’s expertise and value engineering experience beat out structural steel bids because of the benefits the owners saw with concrete. The company works with the design community to take advantage of these benefits in addition to concrete’s sustainable attributes. Webcor Concrete’s commitment to pushing the boundaries of concrete’s contributions to the green building community while offering solutions to build structures at the best value for their customers helps set a standard for the industry.