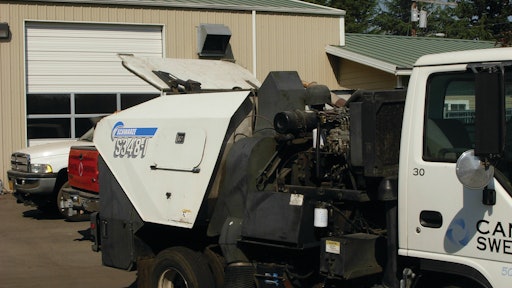
Safety remains essential to every contractor, employee and jobsite. While there are always standard safety procedures to follow, contractors should always keep an eye open for additional ways to keep their crews safe. Mike Wagoner, owner of Cantel Sweeping located in Gresham, OR, is one contractor who took action when a safety opportunity presented itself.
At the time Wagoner purchased Cantel Sweeping in 1993 it was a small sweeping company with seven employees and six trucks. Now, the fleet is up to 18 sweeper trucks and the company employs 24 people. Currently, 90 percent of revenue comes from parking lot sweeping, 7 percent from striping and 3 percent from pressure washing.
Safety community meetings unearth opportunity
During one of Cantel Sweeping's safety community meetings Wagoner was reviewing the accidents that occurred during the past few years. "A little theme started to arise, the drivers would climb up on the back of the trucks to open the hopper door manually," Wagoner says. "We had a couple of slips. This would happen quite often during the fall when it had been raining and the back bumper would be slippery and wet."
Any sort of slip is hazardous to employees, and Cantel Sweeping employees had suffered from three slips over the course of five years. "When someone slips, it's not just that they could hurt their leg, but they might hurt their arm or shoulder straining to catch themselves," Wagoner says. "Even though different parts of their bodies were being injured we determined it was caused by the slips."
Dustin Moist is in charge of overseeing the Cantel Sweeping fleet as well as completing a thorough accident review anytime an accident occurs. During these reviews, his examines the equipment, the employee and the training that took place with an ultimate question of how to prevent the same incident from happening again.
After looking into the slipping accidents, Moist discovered a solution—electric actuators. "The actuators were on the newer trucks we had purchased from Schwarze," Moist says. "At that point, we thought why not retrofit all of the trucks."
Moist purchased everything needed at once to complete the retrofit on 12 units. Slowly, with every free day, the mechanic installed the actuators on all of the older units. "It's a fairly simple installation," Moist says. "There is no real fabrication, and the bracket systems that they had for newer trucks fit the old truck fairly simply with just a little bit of electrical work required."
Employees will see both a safety and an efficiency benefit from the installation of the actuators. "Overall it makes the driver's job easier because we require them to open the back door when they dump to save the life of the seal for the door," Moist says. "As it's easier for them to open the back door they are willing to do it. We won't have to replace the seals and other parts as often because of it."
While cost can sometimes inhibit decisions for upgrades or new installations, Wagoner saw only benefit from investing in the actuators. "However, we reasoned that preventing one or two accidents would more than pay for them."