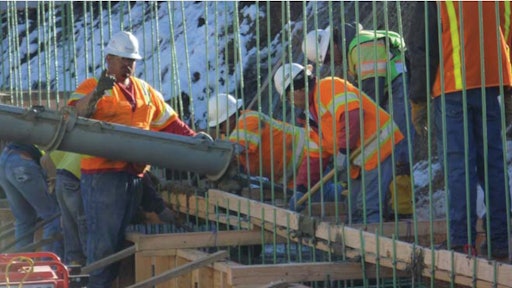
Thrasher Basement Systems is a contracting company that specializes in the repair and remodeling of basements and foundations. The company handles basement waterproofing, foundation repair, crawl space clean-up, basement finishing - just about anything that requires construction or repair in a basement. The company has grown over 300 percent in the past ten years, a real testament to their expertise and reputation for quality work.
Along with the increase in business came some of the typical growing pains, including the challenge of keeping track of their tools and equipment as they were issued to employees and jobs. In 2009, Thrasher Basement decided to install the Checkmate Toolroom Tool Tracking System with a rugged Honeywell mobile barcode scanner from Dynamic Systems to solve this problem.
Thrasher Basement also purchased the Maintenance Scheduler Option so the company can be sure that all its equipment is maintained as required and is available for use when needed. Today, the system is installed in Thrasher Basement’s headquarters and is used by up to three employees to track tools, equipment and consumable items.
Checkmate Toolroom is designed to keep track of tools, equipment and consumables - who has them, when they were checked out and when they are due back. A barcode is scanned to identify the employee or job and another is scanned to identify the equipment. The use of barcode for transactions has proven to be 60 percent faster than manual check-out and virtually 100 percent accurate.
The company says training was relatively minimal with the shop foreman being the main employee trained on implementing the system.
Dan Thrasher stated that they have reduced their tool expense by at least 25 percent since installing Checkmate Toolroom. The job foremen are able to schedule specialty tools so they are available for projects, eliminating the duplicate purchase of more expensive tools.
Thrasher’s management especially likes the reports that identify how much each employee is spending on tools, which has significantly reduced employee waste and theft.
The company considers Checkmate Toolroom a successful program because it has helped them better manage their tool inventory. It has also made the crew leaders and crews more aware and more responsible for the tools they check in and out.