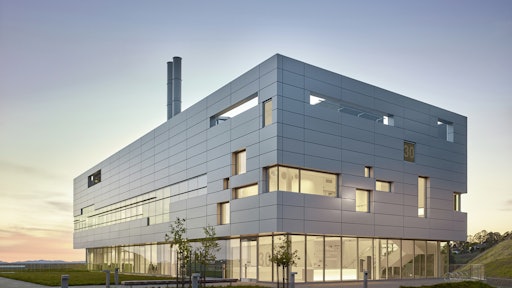
When you’re tasked with designing and constructing a facility that will house over 100 researchers from the U.S. Department of Energy (DOE), sustainability has to be top of mind.
SmithGroupJJR was contracted to design and McCarthy Building Companies, Inc. (McCarthy) was retained to build a Solar Energy Research Center (SERC). The center was renamed Chu Hall, after former Berkeley Lab Director Steven Chu, who later went on to become U.S. Energy Secretary. Chu Hall is a $59 million research facility located at the DOE’s Lawrence Berkeley National Laboratory (LBNL) in Berkeley, CA. Following Berkeley Lab’s mission to “create sustainable, carbon-neutral sources of energy,” the design and construction team voluntarily responded to the DOE’s mandate of 30% energy savings based on ASHRAE 90.1. LEED Gold certification.
Chu Hall is Berkeley Lab’s latest addition to a collection of buildings that create a hub of interactive and collaborative research. Situated in Berkeley’s Old Town neighborhood, the new 39,000-square-foot, three-story building is the new home for the DOE-funded Joint Center for Artificial Photosynthesis (JCAP), the nation’s largest research program dedicated to the development of an artificial solar-fuel generation technology.
Previously, the JCAP researchers worked in a leased space in West Berkeley. In addition to JCAP researchers, the building also houses the administrative offices of the Kavli Energy NanoSciences Institute, which explores energy science and nanomaterials.
Each Level a Challenge
Prior to construction, SmithGroupJJR was tasked with designing a building that was limited by campus planning requirements. This required that the new building be lower than the nearby Advanced Light Source building dome which is the landmark of the LBNL campus.
The design of Chu Hall then had three architectural components, each situated on one of the building’s three levels. The project team was tasked with overcoming unique challenges that were designed for each level.
Level 1 is the subsurface “Plinth,” which takes up more than 50% of the overall square footage and was designed to be an ultra-low vibration space to house laboratories sensitive to light and vibration.
"The programmatic restrictions required light and vibration sensitive equipment to be housed on the ground level," says Suzanne Napier, AIA, LEED AP BD+C with SmithGroupJJR. "This restriction and the topography of the site helped shape the site planning concept by burying the Level 1 vibration sensitive and light sensitive spaces and allowing for the opportunity for creating a larger public plaza between this building and the adjacent building. This helped reinforce the concept of an elevated box/plinth on a light glazed open element at grade level. The site response and programmatic requirements helped shape and reinforce the design concept."
"One of the main challenges this anti-vibration concept created was that Level 1 was the slab-on-grade area so we had to pour an 11 inch thick slab in a restricted area, around structural walls, structural steel, etc., while trying to maintain a high level of floor flatness requirements for the vibration sensitive equipment,” says Robert Parks, McCarthy’s project manager in its Northern Pacific Division. “With the use of laser scanning, we were able to ensure a high level of floor flatness and evenness that was required for the type of equipment the owner had planned for the facility."
An acoustic consultant was brought in to evaluate mechanical, electric and plumbing equipment isolators, and duct and equipment isolation throughout the spaces as well. Napier says this helped to review the implementation of these measures. Vibration evaluations were performed in the spaces at the end of construction as well to evaluate the actual spaces met the vibration criteria set forth in the design.
Level 2, located on the ground level, is the “Breezeway.” Designed to foster interdisciplinary interaction, it is the location for the main door and entrance lobby, shared office space for principal investigators, cubicles for theory researchers and small and large conference rooms.
Level 3 is the “Corona,” a simple rectangular form that houses wet lab spaces as well as research to develop technology needed to assemble nanoscale components into active systems.
Outside, a new courtyard space serves as a central meeting point used by Chu Hall researchers as well as those from nearby labs in the Old Town neighborhood.
DOE’s Need for Energy Efficiency
In order to comply with the LEED certification Berkeley Lab was seeking on this project, SmithGroupJJR designed and McCarthy installed many sustainable features into the building.
"Many sustainable features were chosen as part of the overall energy efficiency goals and objectives of the project to achieve 30% or better than ASHRAE as an absolute minimum," Napier says. "The building was designed and will be operated to use as little energy as possible, so the sustainable elements were carefully chosen."
Mechanical energy-efficient features and sustainable design elements include a runaround heat recovery, which in the winter utilizes the building’s waste heat energy to heat the outside air brought into the building and cools it in the summer. This includes high-efficiency condensing boilers, high-efficiency chillers with variable frequency drives, evaporative pre-cooling hybrid system and individual office VAV terminals with switch for window interlock, which is essentially a mechanical system that knows when a window is open in the office floor.
"This system was the main challenge for us," Parks says. "The final testing and commissioning of this system was difficult. The heat recovery system had many different sequence configurations to ensure that the project optimized energy performance of the mechanical systems. This process required an extensive level of testing, commissioning and adjusting to ensure the system was tuned in at the highest level of energy optimization."
Lighting, energy and water conservation measures are also significant at Chu Hall. A narrow building footprint on Levels 2 and 3 with abundant windows and skylights allows for daylight to enter and minimizes lighting consumption. LED and energy efficient lighting, lighting controlled-light sensors for occupancy, and daylight sensors are used throughout the building, along with daylight harvesting lights that dim when sufficient daylight is available.
Water consumption will also be reduced by 30% with energy-saver plumbing fixtures, landscaping with efficient drip irrigation system and drought resistant plant selection.
Other sustainability features of Chu Hall include a green roof at the north and south portions of Level 1 to provide thermal insulating qualities and minimize heat gain. Building orientation was set to an east-west axis, with the smallest façade facing west to reduce heat gain in the afternoon. Energy efficient, low-E glazing glass was used on the exterior to retain building temperatures. Onsite development was reduced by using adjacent parking, allowing minimized paved areas and more native plantings.
Over 35% green power usage in Renewable Energy Credits (RECs) were designed for Chu Hall. Renewable energy sources include solar hot water panels for hot water heating and photovoltaic panels that power electrical outlets in offices on Level 3.
Napier acknowledges that installing these systems and using some of these materials were more costly upfront, but the benefits outweighed the cost in the end. "Some of these features had an added premium, yes," she says. "They were re-evaluated in many value engineering sessions throughout the project as the budget was monitored."
"Chu Hall featured many sustainable elements in the design, and the project team initially targeted a LEED Silver certification for the final building," Parks says. "Through the course of the project, however, we were able to work collaboratively with the design team and subcontractors to achieve extra LEED credits to push the project to exceed the LEED Gold threshold."
To earn the additional points for LEED Gold certification, the project team was able to achieve the following:
- Increased water use reduction by 40% (exceeding the goal of 35%)
- Increased energy optimization by 40% (exceeding the goal of 36%)
- Achieved 3% onsite renewable energy with the addition of the PV System and Solar Hot Water Systems
- Performed additional measurement and verification of systems
- Added public transportation access
- Worked with the recycling companies to achieve over 95% waste diverted from landfill, which qualifies for exemplary performance; and
- Selected materials with a higher level of recycled content that were manufactured within the region and that were with rapidly renewable content
Sustainability Goes Hand-in-Hand with Quality
To ensure these goals were met, the project team implemented a comprehensive Quality Control Program, which consisted of extensive weekly walk-throughs and evaluations of installations and construction. McCarthy also developed a Water Infiltration Prevention Program which included creating exterior plaster and finish floor mockups and thoroughly water testing the exterior skin.
One unique design requirement that was a challenge for quality, was the architecturally exposed concrete walls. "We constructed the formwork in a manner allowing for full liquid head concrete pours, which eliminated the pour lift lines you would typically see in a concrete wall after it is stripped," Parks says. "Our project team utilized BIM technology to achieve the design and sustainability goals of this project. This project had some very complex mechanical systems in order to achieve its high level of energy optimization.
“One example is that the building had both heating and cooling coils installed at the zone level,” he continues. “This required additional levels of BIM coordination to ensure everything was installed per the plans without conflicts in the field."
While the project involved many materials and methods that helped the building to achieve LEED Gold, Parks indicated that there were not any specific challenges to these increased LEED goals or use of materials as the project team was comprised of seasoned green building professionals.