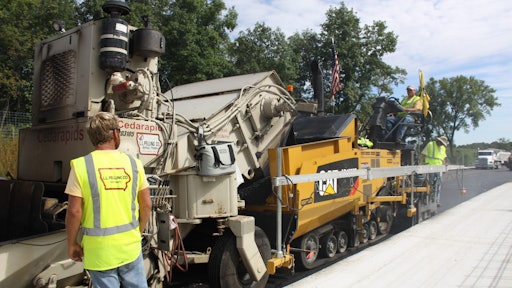
In September, the Asphalt Pavement Association of Iowa (APAI) held an open house to highlight the Highway 100 Extension project near Cedar Rapids, IA.
Highway 100 is a state highway located in Linn County, IA. The route is located primarily in Cedar Rapids and Marion and is known locally as Collins Road. It begins at Edgewood Road NE in Cedar Rapids and ends at U.S. Route 151/Iowa Highway 13 in Marion
The project included HMA perpetual paving a four-mile stretch of Highway 100 mainline from Covington Road to just east of Edgewood Road. It included the construction of HMA and PCC shoulders and longitudinal grooving of dual Highway 100 bridge decks over Old Ferry Road, Cedar River and Ushers Ferry Road. The contractor was LL Pelling headquartered in North Liberty, IA.
The full-depth perpetual asphalt was 12.5-in.-thick HMA on 15.5-in. rock subbase. This was a new section of highway, and field modifications were made to provide a strong and drainable support for the pavement.
“This project was designed to meet the predicted traffic volume,” says Greg Mulder, P.E., director of Iowa DOT’s Office of Construction and Materials. “Parts of the design included drainage, subgrade, subbase and pavement thickness.”
In order to help improve fatigue cracking resistance in the lower lift, reclaimed asphalt pavement (RAP) was not allowed, says Roger Boulet, District 6 materials engineer with IDOT.
“The target for lab voids was decreased to allow an increase in binder content in the lowest base lift,” he explains. “The RAP percentages were submitted by the contractor and approved by the IDOT for the mix designs for the upper lifts.”
A total of 120,000 tons of HMA was placed. For mix design specs, see the box on page ??
“This was a unique opportunity for us,” says Joel Gryp, general manager with LL Pelling. “We were able to construct a full-depth pavement in a rural, four-lane highway setting. IDOT predominately designs new and reconstruction pavements with PCC.”
New technologies = continuous improvements
IDOT used the Highway 100 project to pilot several innovations. “This was a typical HMA paving project,” says Mulder with IDOT. “From the continuous improvement viewpoint, however, different instrumentations were used to evaluate the potential improvement on quality, simplifying the work, and providing better safety for workers.”
Infrared temperature monitoring was piloted on this project to run a correlation on the temperature and roller coverage monitored versus the measured in-place densities of the compacted mixture, with the hope of studying the information for a possible thermal segregation specification.
“The intention is to be able to someday use technology to assist in quality assurance for the required compactive effort needed to build a quality product,” says Mulder.
Roller mapping was also used on this project to track station-to-station pass counts and mat temperature readings for each roller in the train.
“This tool will provide the information needed to compare the mapping results to actual field cores,” says Gryp with LL Pelling. “Ideally it should allow the contractor to fine-tune the pass counts for optimum field densities.”
E-construction enhancements
E-ticketing is not entirely new to IDOT. The first E-ticketing pilot project was on Highway 69 near Ames, IA, in 2015. The pilot was successful in that it provided verification of materials being loaded from a certified plant and delivered to its intended destination.
On the Highway 100 pilot, the DOT wanted further verification of tonnage and mix-type to automate contractor pay and a method for on-site inspectors to record waste and notes for auditing purposes, says Mike Schulz, business development manager with Earthwave Techologies Inc.
“On the Highway 100 project, Earthwave integrated with LL Pelling’s Astec WM2000 Load-Out System out of Plant 17 in Cedar Rapids,” he explains. “With this new capability, Earthwave’s Materials Delivery Solution software records each truck’s load-out ticket electronically in real-time, providing inspectors remote access to easy-to-use mapping and reporting features that allow them to focus more on quality inspection checks instead of collecting paper tickets throughout the shift.”
Each truck has a GPS unit installed which is then tracked through a series of geozones setup at the plant site and the jobsite. Tracking of each load consists of the following:
- The time spent entering and exiting the plant
- The precise time the truck was loaded with tonnage, material type and other pertinent data specific to the project
- Travel time, distance and route from the plant to paver and back
- Amount of wait time spent (if any) on the jobsite and the precise time the truck entered a customized geo-radius of the paver indicating material delivery
“Travel and idle times are recorded in real time for every aspect of the trucks daily routine,” says Gryp with LL Pelling.
Benefits of E-ticketing
Gryp says there are many benefits to using the E-ticketing process:
- Measures and reports exact HMA quantities delivered paperless
- Frees up the DOT inspector to actually perform quality control and inspect the job instead of time-consuming paper shuffling (HMA tickets)
- Allows the paving superintendent the ability to see where every truck is located with real-time tracking and actual load weights
- Creates an electronic trail every minute which is available on the software dashboard.
“The Earthwave software is a great tool to help in trucking efficiencies as a whole and not just this project,” says Gryp. “With multiple projects happening within a 20-mile radius, we’ve found it not only to be a cost effective way to manage our own fleet, but it’s helped in decreasing the need to hire trucks outside of the company.”
Probably the biggest benefit of using E-ticketing is safety.
“With E-ticketing, the DOT is assured the certified product is being delivered and used in the project, without having to have an IDOT inspector verify each individual delivery truck,” says Mulder. “The safety aspect comes from not having to have an inspector maneuver through truck traffic to collect paper tickets from each truck. This ticket taking can now take place remotely from a safe distance through the cloud-based information in the delivery system using an app on a mobile device.”
Schulz says the E-ticketing process also helps save money. “Inspectors can record waste and notes for individual tickets in the field using smartphone and tablet applications and easily tabulate tonnage and mix type totals for contractor pay, cutting out days of processing time when calculated manually. When factoring implications for lost or misplaced tickets, the efficiency gains extended to both the contractor and DOT are even greater.”
Gryp with LL Pelling notes that IDOT had the Highway 100 project budgeted at $18 million and the bid came in at $15 million.
Despite above-average rainfall during the project, the Highway 100 project can be viewed as another successful step toward implementing new innovations and E-construction methods into IDOT projects.
To read the about IDOT’s first E-ticketing pilot project near Ames, IA, visit ForConstructionPros.com and search: 12164619.