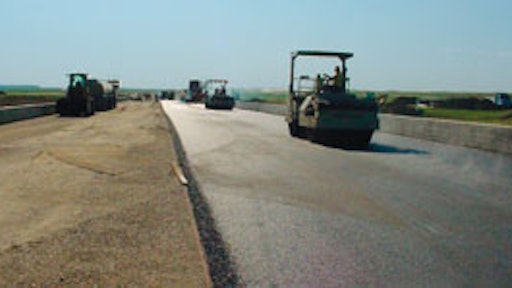
Drag strips are all about speed. Paving drag strips is all about logistics.
So when JTL Group, Billings, MT, was awarded the contract to construct Intermountain Motor Sports Park's quarter-mile drag strip, JTL sat down and put together a plan. And a backup plan. They considered the challenges, analyzed the site, studied the tolerances — and produced a smooth new drag strip recently recognized with a Quality in Construction Award from the National Asphalt Pavement Association.
The first 430 feet of the 4,000-foot-long drag strip was a concrete burn out slab; the remaining 3,570 feet was hot mix asphalt. Plans also called for construction of concrete barrier walls on each side of the track, and construction of the track itself with no seams or joints (other than on the centerline).
"Designing and paving a race track is interesting because the tolerances are so narrow," says Bill Oberlander, JTL Group project manager. "You can't have any cracks, for example, because the more cracks there are in the pavement surface the slower the cars go. It's all about smoothness and contact area and when there are cracks, even cracks as small as ¼ inch wide, the tires aren't in contact with the pavement. Cracks reduce the traction and less contact with the pavement means slower cars."
Owned by Knife River Corp., JTL operates five divisions in Montana and one in Wyoming doing site work; road, street and subdivision paving; grading; and concrete work. The Billings operation employs 125 people peak season and runs two or three paving crews at a time, depending on job size. A Billings-based sister company, Empire Sand & Gravel, was also involved in the drag strip job.
When JTL planned the drag strip project it built the concrete start pad first. At the end of the concrete burn out pad to support the asphalt they built a concrete step beneath the pavement to support the asphalt.
"We did that to keep the asphalt from settling," he says. "On a job like that, at the place where the cars transition from concrete to asphalt, you need a smooth transition. You can't have any settling so we used a concrete step to provide support."
Oberlander says that 12 inches down, JTL constructed a 24-inch-thick concrete step to underlay the asphalt. There the asphalt was 12 inches thick and gradually decreased to the typical thickness of 4 inches.
"So right at the beginning of the asphalt it's sitting on a concrete base."
Next JTL constructed concrete barriers on each side of the track. Because the start pad needed 28 days to cure, and the project didn't allow for a 28-day delay, JTL left a 30-foot-wide space in the barrier wall to allow delivery trucks to access the site mix.
JTL initially started the hot mix paving part of the job incorporating a material transfer vehicle (MTV) into the paving operation, reasoning that was the best way to keep the mix hot and reduce segregation.
"Unfortunately about one-third the way through the project the MTV broke down forcing us to shift to Plan B, which was belly dump trucks and windrow elevators," he says. "So we had to go in and pull out the MTV, pull out the paver that was working with it, and simultaneously get the backup delivery and windrow process up and running. It wasn't pretty but we got it all switched out and done."
JTL paved the 60-foot-wide drag strip using two pavers working in tandem, paving 15-foot-wide passes.
"We couldn't afford a cold joint per the specifications, so we had the two pavers out there at the same time," Oberlander says. "Pavers were generally 50 to 100 feet apart going down the strip at the same time."
He says the crews maneuvered 16 belly dump trailer trucks moving in and out of the site, two pavers, two windrow elevators, and three rollers (one breakdown roller on each side and a finishing roller for the entire mat) within the site.
"There was an awful lot of equipment in a small space, which made the job and the organizational logistics even more difficult," Oberlander says. "But we planned for all that. We thought about it, had contingencies in place, and got a little lucky."
Because paving the drag strip took four days, JTL had to determine where to stop paving each day. They eventually decided to construct a 30-foot-wide pass of a 2-inch base each of the first two days, followed by a 30-foot-wide pass of a 2-inch surface course each of the second two days.
"The paving area was so short we couldn't drop back and tie in, so we had to let the pavement cool down so it would support a truck," he says.
Another challenge was the 2-foot-thick concrete barrier wall that ranged from 30 inches to 39 inches high on each side of the track. JTL's crew slipformed the barrier walls, then had to place and compact hot mix asphalt right up against the concrete, tying the hot mix into the concrete (and with concrete start pad).
JTL Group used a polymer-modified asphalt supplied by Exxon in Billings and teamed with Rob Kukes, owner and mix design engineer of Rimrock Engineering, to develop a polymer-modified mix. He says the mix worked well and JTL's crews excelled in placing and compacting.
"We ran a profilograph over the pavement and for these tolerances we did a really good job," Oberlander says. "We couldn't have any more than a 1½-inch deviation per mile or have a single deviation greater than 0.15-inch in the surface. Considering that the asphalt pavement is only about three-quarters of a mile long it was extremely difficult to achieve that degree of smoothness within those tolerances, and we did. The crews did a great job being able to achieve that."