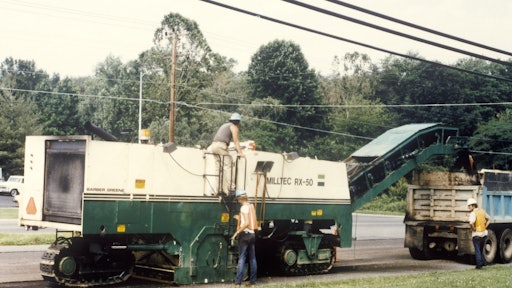
Milling machines, also known as cold planers, complete the same task today as they did 30 years ago, but they have seen several innovations over the years and are continuing to evolve. It was actually two events in the 1970s that brought about the creation of the modern milling machine.
According to the Basic Asphalt Recycling Manual from the Asphalt Recycling and Reclaiming Association (ARRA), the petroleum crisis of the early 1970s and the development and introduction in the mid-1970s of large scale cold planing equipment, complete with easily replaceable tungsten carbide milling tools, were the catalyst for a renewed interest in asphalt recycling.
In the early 1970s, recycling asphalt was relatively disjointed and inefficient, but the oil embargo at that time created a demand for a more efficient way to recycle asphalt. Incorporating recycled asphalt in the mix meant less liquid binder was required, lowering the mix production costs and the required amount of virgin aggregate. The milling machine solved many economic problems associated with limited oil supplies and high material costs of the time, much the same as it can do with today’s prices.
According to Joe Musil, a former engineer with CMI/Terex Roadbuilding, Bill Swisher, owner of the same company, realized the potential in recycling asphalt and, in 1974, created the Roto-Mill, which was the first dedicated milling machine in the United States. It was derived from a rear load dirt trimmer that had a conical tooth drum installed in lieu of a spade tooth drum, to cut both concrete and asphalt.
Since then, milling machine manufacturers have been proactive in the development of the technology of these units which have advanced exponentially in the last 30 years.
A ‘necessary evil’
“Not too long ago, the milling process was considered a necessary evil in which a paving contractor was forced to mill from time to time to correct a curb line or scarify a bridge deck,” says Jeff Wiley, senior vice president at Wirtgen America.
In the 1980s, milling machines were hydro-mechanical with manual or lever valve controls. Grade control was hydraulic and used contacting sensors. “There was no great emphasis on smoothness of the cut surface,” says David Peterson, Application Engineer with Caterpillar Inc. “The machine was simply used to remove material.”
Although those systems were very reliable, today’s milling – with its need to establish a super-smooth substrate for super-smooth HMA pavements – requires a more sophisticated system.
“Today you can read out dual grade, grade-and-slope, stringline sensing, averaging, laser-reference, and GPS coordinates,” says Wiley. “One ground man could easily control the grade from either side of the machine, compared to always having two ground men in the past.”
Production, reliability increases
The base components and features of the original machines — cutters, conveyors, engines and machine weight — are still the required components of today’s machines. However, these components have evolved over time.
With the emphasis on increasing production, cold planer design evolved from “rear loading” to “front loading” machines in order to facilitate truck loading and truck maneuvering, says Kyle Hammon, Product Manager - Mills, Stabilizers, Brooms with Roadtec Inc.
“Early milling machines were designed to operate as ‘rear load,’ meaning the secondary conveyor would extend over the milled surface to load the dump truck,” he says. “The machine would be moving in reverse compared to how they’re conventionally operated today.”
While this was the most efficient way to remove material from the cutter housing at the time, it created issues with trucking and traffic flow problems. Machines with front discharge conveyors were introduced in the 1980s, which made it easier for the truck to move with the milling machine and in and out of traffic.
Higher production and greater reliability are coveted by today’s contractors. A milling machine that would cut 2 inches in the 1980s at 30 fpm has been replaced by one that can cut up to, and over, 100 fpm today. “Thirty years ago, you would mill for an hour or two, then have to work on the machine for an hour,” says Wiley. “Today’s machines are much more reliable, and downtime is minimal.”
Horsepower has increased significantly over the years from original 375-hp machines to those pushing 1,000 hp — which are capable of milling the entire width of a lane.
Now, onboard computers boost productivity and performance, while optimizing fuel consumption and preventing overload of vital components. “The old days of cutter hydraulic and chain drives are gone, replaced by more reliable and efficient belt drives, with more power directed to the cutter,” says Wiley.
New equipment designs mean less down time in the cutter maintenance area. “Reliable bolt-on and pressed-in holder systems – which are critical to continued productivity when retooling a drum, or tool replacement after hitting buried iron – are far superior to the weld-on holders of the past,” he says. “It all amounts to greater ease of operation, with less stress on the operator and ground men.”
Versatility
Today’s contractors expect more versatility out of their milling machines and manufacturers are delivering. “Variable widths are available with segmented cutter housings to allow contractors to bolt on extensions to their cutter housing to change widths,” says Hammon with Roadtec. “Some mills are bi-directional, meaning they can operate in either direction. This allows the machine to downcut with the cutter drum, which provides better sizing, and also to provide a rear load conveyor, both are very useful for cold-in-place recycling applications.”
Three- and four-track machines are now offered to fit contractor need and preference. Track design has changed over the years to deliver more traction when working in deep or tough cuts. Steel tracks with polyurethane pads have helped to increase tractive effort of these machines.
There are also more choices available today in terms of cutting width and power for milling machines. For instance, smaller mills have been developed to efficiently handle smaller scale tasks such as milling around manhole covers. Customers now have the option to diversify their fleets which can benefit them by broadening their specialized capabilities. This affects how they manage their fleet as well as how they estimate jobs.
“Added machine flexibility and utilization means more dollars and higher profits,” says Wiley. “The most significant technology advance has been the new ability to use one machine for multiple applications.
“For example, today you can buy a machine on which a contractor can quickly change cutter patterns, from perhaps a 5/8th-in. spacing to a 1/4-in. spacing to fit particular jobsite requirements,” he says. “You can also fit smaller cutter widths into the same unit to cut a smaller-width cut instead of having to acquire or rent a whole new machine to do that width.”
Cutting innovations
Tooth consumption was very high years ago. “Today, you use less teeth because they have at least three to four times the life as compared to the past,” says Wiley.
One recent innovation in this realm is the introduction of PCD (polycrystalline compact diamond) bits.
“Ordinary carbide tipped tools need replacement quite frequently,” says Peterson. “Stopping the mill to replace these can be costly considering you might be stopping a fleet of trucks, an asphalt plant and a paving crew; plus, you might have time restrictions on certain jobs like tunnels or airport runways.”
PCD bits, a.k.a. “diamond bits”, are designed to last 40 to 80 times longer than carbide bits and have reduced risks associated with bit replacement.
“Diamond bits do not change length as they are used which is different than carbide,” says Peterson. “Carbide bits get dull and grow shorter as they wear, causing uneven milled surfaces and potentially causing grade inaccuracies. Dull bits can also lead to more fuel burn– up to 15% more. Diamond bits will stay sharp longer and will always stay the same length, providing smoother, more accurate cuts with less strain, less fuel consumption and less wear on the machine. ”
Cutting patterns – such as micromilling with a fine-tooth drum – are also customizable to particular jobs with many options offered to the contractor.
Dust control
The silica dust issue has shaped milling machine design in recent years. In late March of this year, the Occupational Safety and Health Administration (OSHA) issued its final rule which reduces the permissible exposure limit (PEL) for respirable crystalline silica to 50 micrograms per cubic meter of air and requires employers to use engineering controls (such as water or ventilation) to limit worker exposure.
As of January 1, 2017, all cold planers over 60,000 pounds must be equipped with a method for pulling dust away from the mixing chamber to protect the ground crew from exposure to silica.
Milling machine manufacturers have been proactive with the issue and have already begun modifying their machines to meet the new limits. Most of the standard approaches from manufacturers include a blower at the lower conveyor to capture the dust from the cutter housing and channel it up the conveyor. Tapping into the machine’s on-board water system for cooling cutter teeth, a sprinkler system on top of the belt is used to keep the dust down.
At Bauma this spring, BOMAG unveiled a prototype for a different approach to dealing with silica issue by eliminating the dust.
“The system works by electrostatically charging the silica dust so it binds together to form larger flakes that cannot be inhaled by workers, thus nullifying the potential detrimental effects of silica dust,” says Tim Hoover, product manager, mills and MPH equipment for BOMAG Americas. "We are currently putting the system through field evaluations.”
Smarter machines
Today’s milling machines are also smarter than they were three decades ago.
Throughout the years, the industry has seen an expansion in technology for grade control.
“Today’s sonar control system with multiple-eye skids help to control the depth of cut better than manual sensors that run off of string lines,” says Hoover at BOMAG. “This requires a more sophisticated machine design with more electronics, but it has helped to increase speed and accuracy.”
Taking advantage of advanced electronics on engines and modifying hydraulic systems, today’s machines have load controls on engines. “If the machine encounters a tough-cut section of the pavement that puts more load on the engine, the milling machine automatically adjusts speed to the difficulty of cut,” he says. “This improves productivity while reducing wear and tear on the machine.”
Telematics systems for milling machines give more operating data to key contractor and dealer personnel than at any point in the cold planer’s 40-year history on the market.
“Telematics can track fuel usage and machine utilization,” says Hoover. “Additionally, fault codes can be forwarded to key service personnel, so minor issues can be addressed before they become major expense items. These systems can also track machine location as well as automatically give service reminders.”
Looking down the road for milling machine design, technological innovations will be at the forefront for these machines.
“The milling process and the end result will be similar, but new technology will allow troubleshooting in the field to be remotely controlled,” says Wiley at Wirtgen America. “Maintenance will be monitored from a main office, and actually already is in some areas.
“Cutter designs could change dramatically from what we know today, to a much cleaner design,” he continues. “The operation of these machines will be less stressful, with more operational functions performed by the machine. There will be even more accurate control of grade, and the quantity of millings placed in the truck. Someday more advanced technology could enable one-man operation, instead of three.”
Another trend to keep an eye on: 3D control systems. “Pavement rehabilitation using 3D control systems allow reshaping of the surface during milling,” says Wiley. “They work independently of references on the ground, instead using a digital terrain model as specified parameter for the milling depth. A milling machine equipped with the 3D control system delivers the desired milling accuracy in the millimeter range.”