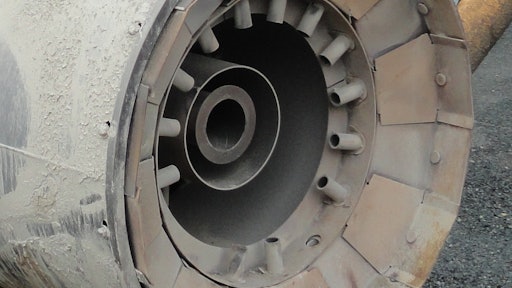
Last issue, I talked about burner tuning and the proper tools to use to analyze the performance of your burner, and how both of these things can optimize fuel consumption at your asphalt plant.
In this column, I'll explain how precise control of the equipment and routine maintenance will go a long way to keeping your burner tuned, saving fuel consumption and your bottom line.
As a regional Hauck Burners sales center for the Western U.S. and Canada, I get to play with a lot of very cool technology. The newest lines of burners and controls are simply awesome. In February, we installed the latest version of their BCS7000 on a plant in New England.
To say it is working flawlessly is an understatement. This is in large part due to the fact that we performed maintenance on their existing burner. This control is easy to use and very intuitive.
In the process of some serious plant upgrades, we pulled off the existing Echo-Star II, ESII 075 burner. While it was off, we performed some routine maintenance. We cleaned everything, patched a hole blown in the burner body from the mixing drum “blue smoke” fan, and replaced some missing parts.
As evidenced by this picture, our ESII had lost some natural gas nozzles in the course of its 18-year life. Also, you can see that we are getting a bit of aggregate raining through the flame path at the burner end. This is where the wet material is coming from in the nose of the burner. We cleaned this all up, freed up the spin vanes, and replaced the missing nozzles.
To solve the aggregate raining down on the burner we built a pent-roof over the nose of the burner that extends out about a foot. This keeps the aggregates from spilling through the flame path.
Once we adjusted the NG pressure to 3.5 pounds and started running, I performed a burner analysis using my PCA-235 and the CO was around 100 ppm. Perfect. So this burner required no adjustments other than cleaning. Now we have a happy customer, and I'm off to install and tune another burner, this time up in Washington state.
To summarize, the first step in burner tuning is precise control of your equipment. In this case, I made sure all the linkage was secure and not worn, then I set the burner up to factory recommended settings. Next came routine maintenance.
In this case, the burner was already out so it was easy to accomplish the routine maintenance. But taking the burner out is not necessary. All the cleaning and adjustments I made could easily have been accomplished with the burner installed. Just remember “Lock Out-Tag Out” procedures to protect yourself and your employees.
As it turned out with this burner, the only real adjustment I had to make was a small one to fuel pressure, and it was ready for the upcoming paving season.