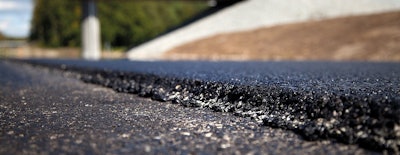
Rollers with an oscillating drum have proven their worth in a number of compacting applications. They are particularly well suited for compacting asphalt when vibration should be minimized, for instance on thin asphalt lifts, bridge decks, near building foundations and concrete structures.
The benefits of oscillation
An oscillating roller mainly exerts horizontal forces on the asphalt layer, together with the static load from the machine itself. The roller is always in contact with the surface and the horizontal movement ‘massages’ the surface.
This leads to efficient compacting with very little vibration transmitted to the surrounding environment. This more gentle compacting allows the roller to be used in vibration-sensitive areas. Oscillation is also beneficial when joining existing and newly laid asphalt layers.
The lack of vertical movement with oscillation reduces the risk of over-compacting and damage to the aggregate. Oscillating compaction is also quieter and more comfortable for the driver.
How it works
Oscillating compacting of asphalt is usually performed with rollers featuring twin drums, one with vibration and one with oscillation. The drums can be activated individually, and the oscillating drum is commonly placed at the rear.
In the oscillating drum, two rotating eccentric weights are placed away from the drum center to generate the back-and-forth oscillating motion of the drum as it moves across the surface. This means that, as opposed to the vibration system, the drum does not move its axis of rotation, but rather oscillates around it.
Counteracting tougher wear with tougher steel
The trend towards thinner asphalt layers and harder aggregates favors the use of oscillating rollers. Oscillating avoids the drawbacks of vibration which is often too severe for the thinner layers that are becoming more common.
The horizontal oscillating movement although creates a grinding effect on the drum’s surface. The active life of a roller is often more than 10,000 hours. To avoid the need for a drum replacement because of excessive wear during this time, the usual solution is to use a thick drum made of mild steel such as S355 (A36). However, equipment manufacturer Dynapac decided to take their design in a different direction.
Searching and finding the solution
Dynapac wanted to use a relatively thin steel to make the drum light. There is no advantage of having a thick and heavy drum, quite the opposite. With a lighter drum, it’s possible to reduce the size of the mechanical components that rotate the drum and create the oscillations. This in turn reduces the fuel consumption of the roller, to the benefit of the operator.
When Dynapac’s design and production team looked for a working solution, they targeted a 16 mm (6.630 in.) thickness for the drum. To ensure the service life was long enough, they also needed a hard steel that was able to cope with the particular wear challenge seen on an oscillating drum. Plus, they needed to be sure it could be bent into a perfectly round shape without having to invest in new rolling equipment.
The abrasion-resistant steel Hardox wear plate from SSAB promised to deliver on all accounts. After consulting with material and production specialists at SSAB’s Knowledge Service Center and testing different grades of Hardox wear steel, Dynapac concluded that Hardox 450 had the optimum mix of hardness for wear resistance and ductility for workshop performance. The proper welding process was worked out together with SSAB.
“In this project we have worked very closely with SSAB‘s wear and manufacturing experts. We used their knowledge to establish the best way to bend and weld the drums. This cooperation has been very valuable when developing our new oscillating rollers,” says Andreas Lager, manager for structural analysis and design at Dynapac.
When the production techniques were in place, a couple of full scale prototypes were constructed and put into action in regular field tests.
“Our prototype rollers were monitored for up to 1000 hours of tough operation and the oscillating drums showed hardly any wear at all. It was really satisfying to see that the grooves from the turning of the drums were still clearly visible on the drum surface,” says Andreas.
Perfect for speed & high productivity
A large number of Dynapac’s oscillating rollers in the CO series are now in full operation around the world. Some of the machines have been involved in a prestigious project in Asia, ensuring a perfect surface on the new Formula 1 race track in Hanoi, which will be ready for racing in 2020.
“A Dynapac roller normally requires extremely little maintenance. The timing belts inside the oscillating drum are however something that might need to be replaced during the machine’s lifetime. This is the case on all oscillating drums due to how they are constructed. Therefore we have put a lot of effort into making the change as simple and fast as possible. A belt swap on both sides in a Dynapac CO roller can be done in as little as two hours, thanks to a smart design and easy access through large manholes on each side of the drum. I think this must be some kind of record,” Andreas concludes.