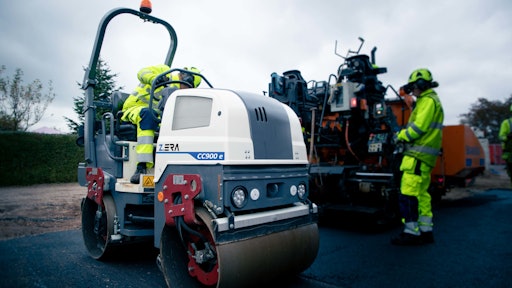
Content Sponsored by Dynapac
As the busy season winds down for many contractors, now is the time to start thinking about the equipment you will need for next year - and years to come. With increasingly stringent specifications to meet coupled with changing regulations, your purchasing decision today needs to match those future demands.
At Dynapac, we are consistently designing our equipment to not only perform today, but be able to be the workhorse your company will need to compete tomorrow as well. Those machines include updated features to meet job specifications now, as well as the technologies that will help you meet an emission-free future.
Data Driven Compaction
When it comes to meeting jobsite specifications, nothing is more important than compaction - and documentation of those efforts.
Dyn@Lyzer, a compaction control and documentation system, collects data that gives users a complete view of compaction levels achieved across the project. Information is recorded at each pass and data is continuously displayed on the computer screen. The data is, at the same time, recorded and saved allowing full traceability and quality assurance.
We pair that data with the Dyn@Link system which allows users to track machines conveniently from the office, always knowing where they are and if they are running. The user can access this information from anywhere, anytime.
By adding a notification email address the system automatically notifies the user when a machine enters or leaves a predefined area. Thanks to this geo-fence function within Dyn@Link, it is very convenient to keep track of machines, even when not logged in to the webpage.
Other types of compaction technology have also evolved over the years, changing to meet different applications. The use of oscillation rollers is gaining popularity near highly populated areas where noise of vibration is a concern and Dynapac has made the use of these machines easier for our customers.
Dynapac constructed our oscillation drums out of Hardox® 450 steel, which is the hardest steel that can be shaped into a drum shell which prolongs the life of the drum. This helps eliminate premature wear on the drum.
Dynapac also shortened the lengthy and difficult process of changing the timing belts for the oscillating drum’s off-centered eccentric weights. Typically, a two-day job that must be done in the shop with other brand rollers, involving dismantling the drum. Instead, the timing belts on Dynapac’s oscillating drums can be replaced in two hours and can be done in the field if necessary.
Production today while helping you meet the needs of tomorrow is just one way Dynapac is working to be Your Partner On The Road Ahead - driving the construction industry forward through innovation.
Electric that Exceeds Expectations
Another way we are helping future-proof the construction industry is by being a leader in the development of electric equipment.
Construction business owners have heard about the future of construction equipment and how electrification will change how the industry works. Dynapac has been at the forefront of electric-powered equipment with the introduction of an emission free product almost ten years ago - a prototype electric roller. The need for zero emission projects is gaining momentum and in 2021, we entered a new ERA “for an emission free world” with the introduction of our Z.ERA equipment.
Last year, we introduced the new Dynapac CC900e - the first-of-its-kind electric-powered tandem roller. The machine was designed to compete in the 1.5 tons tandem vibratory roller class. But, unlike the diesel fueled model upon which it is based, the new CC900 e tandem vibratory roller produces zero emissions at the point of operation.
Although the battery system used in the new model is both proven and popular, it was subjected to rigorous testing to ensure that it meets the specific needs of the compaction equipment sector and is capable of withstanding the vibration generated by the roller. During that testing, prototype machines have clocked a massive amount of hours in operation.
But Dynapac didn’t stop there.
In helping drive the push towards full paver electrification, we unveiled the Dynapac SD1800 electric-powered paver. As a glimpse of things to come, it will help lead the way to a new era of more environmentally friendly machines and cleaner construction site environments.
Its new electric drive comes with a highly efficient 3-phase permanent magnet synchronous motor (PMSM) that provides 55kW of power to the hydraulic system (screed, undercarriage).
In terms of paving autonomy, and depending on the type of job, application, and intensity of the work cycle, the SD1800We offers up to four hours of rugged performance with one single charge. Charging is done with a provided CE-compliant Type 2 plug for 400V, 6-32A, 1.4-22.0kW AC and completed via a wall box or a charging station.
The SD1800W e is also chargeable using a Type 2 AC or CCS2 DC. Depending on the battery's condition (temperature, battery cycles) charging, takes around 3 hours to go from 5% to 80% at 400V 22kW (AC) and 40 minutes to go from 5% to 80% at 80kW (DC). And while charging while working is not possible, one can pre-heat the screed with the charger (with Type 2 AC or CCS2 DC) while waiting for the material to arrive, thus preserving the battery level.
The electrified journey has just begun. Our electric equipment is being developed each day, arriving at a time when many equipment manufacturers are looking to electric power to help reduce and ultimately eliminate exhaust emissions.