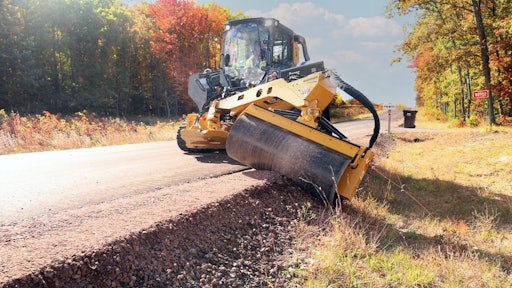
The nature of building a road has not changed much throughout the years, in terms of the earthworks, constructing a foundation, creating an embankment, and paving the sub-base, base, and top layer according to traffic load and weather conditions.
What has changed is that the roadbuilding technology being used to execute the tasks has become more sophisticated and now includes alternative power sources, artificial intelligence, and remote control.
The Case for Using New Technology
Experts at Topcon, which develops technology for the construction industry, stressed the importance of why contractors should digitize their paving workflow, noting that demand for quicker delivery and increased sustainability on projects puts heightened focus on the need for large-scale digital transformation.
The experts pointed out that technology helps to mitigate the challenge of finding skilled machine operators. Additionally, material costs call for more efficient approaches to jobs, to avoid waste.
The experts listed five reasons why now is the time to integrate the latest technology into a company’s operations. Today’s technology:
- Maximizes efficiency, a plus in projects where short timeframes to complete paving work are common in projects requiring full closures.
- Improves accuracy and consistency.
- Saves money and materials by speeding up the process.
- Increases jobsite safety, reduces human error, and requires fewer people on the jobsite.
- Enhances a connected workflow.
Additionally, today’s technologies help to extend the lifespan of equipment and assist in mitigating the labor shortage.
“We are also all very aware of the tremendous labor shortage across the U.S., and especially in industries like construction. It is taking a toll on our customer’s ability to complete work,” noted Jeremy Dehnel, director of sales at Road Widener, which produces road construction equipment attachments.
“This has driven interest in a need for machinery that has the technology and features to complete more work with a smaller crew,” he said. “We have always sought to design solutions to limit labor and increase safety.”
New Technology Options Abound
Dehnel noted that among the number of trends influencing the equipment that contractors look to for paving technology and other road construction, is machinery that is compact enough to keep one lane open in the work zone to reduce traffic congestion.
To that end, Road Widener offers the FH-R material placement attachment and Offset Vibratory Roller, designed for easy operation without the need for extensive training.
“They connect to equipment commonly found in contractors’ fleets, including skid steers, compact track loaders, front loaders and graders,” Dehnel said.
Dehnel pointed out that with the U.S. Department of Transportation Road to Zero safety initiative and an overall focus on safety in the construction industry, “we recognize the importance of OEMs and contractors working together to ensure that crew members get home safely each night.
“One area that Road Widener noticed a gap in construction safety is in compaction, which is why we developed the Offset Vibratory Roller,” he added. “This attachment is designed to allow the host machine to drive safely on level ground while compacting sloped shoulders, ditches, trenches, and other hard-to-reach areas alongside the road. These tasks have typically put road crews in danger of rollover accidents, and increased workers’ comp costs and poor safety ratings.”
The FH-R material placement attachment can run a wide variety of materials including asphalt, aggregate and gravel, so contractors can use it for different utility and road construction jobs, said Dehnel.
Remote Control Promotes Safety
The FH-R requires only one operator to run, which can be done remotely from the comfort of the host machine, increasing the crew’s safety by keeping them off the road and out of harm’s way, Dehnel added.
“Its accurate material placement prevents material from scattering onto the roadway, eliminating the need for an operator to follow with a street sweeper to clean up,” said Dehnel.
The Offset Vibratory Roller is designed to offer the same benefits of the FH-R, in terms of operation from the host machine cab, as well as the additional safety benefit of eliminating rollover risk when compacting material.
Additionally, the compact design of both the FH-R and Offset Vibratory Roller allows the attachments to be transported with a standard trailer and pickup truck rather than a lowboy trailer and semi required by a large, self-propelled shouldering machine, Dehnel said.
Road Widener also offers the Curb Backfiller accessory for the FH-R material placement attachment.
“This really comes down to efficiency and how the Curb Backfiller accessory accelerates project timelines, increases safety and cuts out unnecessary steps in the backfilling process,” Dehnel said of its use on construction projects.
The Curb Backfiller accessory is designed to easily attach to the FH-R and can fill on the righthand side by default, or the left, with dual configuration and precisely dispense material over the curb to backfill with dirt or aggregate.
It provides a cleaner, more accurate process by backfilling curbs and keeping debris off the roadway and boosts efficiency, accuracy, and safety by replacing a backfilling method typically done manually by workers with shovels, said Dehnel.
Crew members can operate it with the original FH-R remote to improve convenience and reduce the number of needed laborers to just one, he added.
“This not only removes the manual labor aspect of backfilling projects, but also eliminates the cleanup process,” Dehnel said. “Backfilling with a bucket or shovel scatters material outside the curb, requiring a final cleanup step. The Curb Backfiller accessory eliminates the need for street sweepers.
“Contractors can accomplish more with their host machine without having to haul in additional heavy equipment. The Curb Backfiller excels in applications such as residential developments with new curb and parking lots with green space requiring backfill.”
The accessory is designed to keep new curbs intact with a protective wheel that prevents the accessory from scraping against the curb and to provide not only a better backfill, but also a longer curb life, Dehnel said.
All Road Widener equipment is remote operated.
“Both our FH-R Material Placement attachment and Offset Vibratory Roller are controlled from the comfort of the host machine with a user-friendly remote,” said Dehnel. “Each connects to commonly owned host machines such as most loaders, skid steers, compact track loaders and graders.”
Moving the Needle on Intelligent Compaction
Intelligent compaction is not necessarily new, but has made major advancements recently, Mark Eckert, product manager, Compactor, Compact Assist, Volvo Construction Equipment (CE) noted.
Volvo now offers three different packages of its Compact Assist software, providing varying degrees of access to the core functions of pass mapping, temperature mapping and density/stiffness mapping.
Compact Assist Start is the company’s entry-level package “that’s perfect for customers who haven’t used intelligent compaction before,” Eckert said. “It provides real-time information on pass and temperature mapping in a system that’s as easy to use as a smartphone.”
Compact Assist is the middle level that is ideal for those looking to record and track data across a jobsite, he added.
“It includes pass and temperature mapping like Compact Assist Start, but also provides greater accuracy and reporting opportunities through the addition of a high-accuracy GPS antenna, recorded and saved job data, automatic job report creation with USB and over-the-air downloads,” said Eckert.
Compact Assist with Density Direct is Volvo’s most comprehensive package that combines all the features of Compact Assist with the addition of density mapping functions “for those serious about increasing productivity and delivering a faster bonus,” Eckert added.
The Trimble Roadworks Paving Control Platform is Trimble’s next generation machine control paving technology, said Kevin Garcia, Trimble’s general manager of civil specialty solutions.
“The latest version of Trimble Roadworks includes horizontal steering control and automatic screed width functionality specifically for Vogele Navitronic asphalt pavers,” he added. “This functionality automatically steers properly equipped asphalt pavers and controls the screed width according to a 3D design, making it Trimble's most advanced 3D paving system to date.
“The auto steering and screed control functionality provides higher quality and more accurate paving faster and with substantially less operator fatigue than traditional asphalt paving methods. The system also helps reduce waste and improve jobsite sustainability, making it easier to accurately estimate material quantities and use less asphalt during the paving process.”
BOMAG’s remote-controlled single drum roller (SDR) is designed with safety top of mind “with the goal to prevent major safety issues for construction companies by taking the driver out of the dangerous areas at the construction sites,” said Ruben Garcia, BOMAG product marketing manager, soil compaction.
“The operator can fully control the equipment from a distance up to 100 meters from the machine for a safe operation even in challenging conditions along edges, in trenches, or in the risk of a landslide,” he added.
As this story in IRONPROS about CONEXPO 2023 noted, one of the several trends in today’s roadbuilding technology is the rollout of more battery electric vehicles. More intelligent vibration control and autonomy options are emerging. Machine data and performance is augmented by technology offering comfort, ease of use and a more comfortable environment for the operator in the cab.
Volvo’s new battery-electric compactor, the DD25 Electric, brings the advantages of lower noise and zero-emissions equipment to road building, noted Justin Zupanc, head of electromobility and autonomous solutions, road products, Volvo Construction Equipment.
“This double-drum compactor offers 24 kW of available power, which is 30 percent more than its diesel counterpart,” he added. “The result is a more responsive machine in terms of speed and vibrations. The 360-degree visibility and high-frequency compaction allow operators to achieve a smooth finish with speed.
“It can do all the jobs a similarly sized diesel machine can do, including street repairs and patching, parking lots and driveways, and its emissions-free operation allows the DD25 Electric asphalt compactor to help organizations meet emission regulations or their own sustainability goals.”
The DD25 Electric can operate for a full shift on a single charge, depending on the type of job and intensity of the work cycle, Zupanc pointed out.
“The machine comes with an integrated on-board charger that enables charging from zero to 100 percent in as little as three hours,” he pointed out. “With an optional off-board DC fast charger, this can be achieved in just over an hour.”
The DD25 Electric compactor requires much less time and money in terms of maintenance because it does not have an engine, said Zupanc.
“Charging a battery is more cost-effective than buying diesel fuel, and there’s no need for engine-related maintenance products like engine oil, oil filters, diesel particulate filters or diesel exhaust fluid,” he added.
The DD25 Electric is the newest addition to Volvo’s electric lineup, which also features three electric compact excavators and two electric compact wheel loaders.
The machines are designed to offer the same performance as their diesel counterparts, “so any task a roadbuilder uses a compact excavator or wheel loader for could also be done by these battery-electric machines,” Zupanc noted.
Because road construction usually involves medium or large class sizes, Volvo is launching its midsize EC230 Electric excavator in North America in 2024.
In early 2023, Volvo introduced remote control technology called Short Range Remote Control as an option on the company’s EC250E, EC300E and EC350E excavators.
The remote control works at approximately a 100-meter distance, and the operator can communicate electronically with the machine via a radio transmitter and receiver.
“Ideal applications include ones where visibility, falling debris or machine rollover may be an issue, as well as when the operator needs to keep a closer eye on the tool. If a road construction project includes steep grades or needs enhanced operator visibility, Short Range Remote Control could be a solution,” Zupanc pointed out.
AI is Playing a Greater Role
BOMAG has a number of AI projects in the pipe, Garcia said.
The company’s remote controlled single drum rollers is just the beginning of a number of technologies the company will be rolling out, followed by lane assist/field assist technology, teleoperation electronic coupling, highly automated SDR, and full autonomy compaction, he adds.
Learn, Connect, and Grow at the Premier Pavement Industry Event
The optimal experience in learning, networking and equipment demonstration presents itself through PAVE/X: The Pavement Experience. The immersive trade show takes place January 30 to February 1 at the Henry B. Gonzalez Convention Center in San Antonio, Texas.
The educational program features tracks in paving, striping, sweeping, sealcoating, and business management. More than 20 pieces of equipment will be demonstrated for the attendees. Networking opportunities enable attendees to connect with other attendees and equipment manufacturers.
Tech-enabled Road Repair and Construction: A Multi-Billion Dollar Opportunity
There are numerous opportunities for constructing new roads and repairing existing ones, with alternative power, AI and remote control giving contractors the ability to do so efficiently and safely.
Making the case for that opportunity is the ‘D’ grade that the American Society of Civil Engineers (ASCE) gave the nation’s roads on its 2021 report card.
The ASCE noted that there are more than 4 million miles of public roadways in the U.S., with these roadways expected to withstand an ever-increasing volume of traffic each year.
The growing wear and tear has left more than 40 percent of the nation’s public roadways in poor or mediocre condition. The majority of those roads tend to be on urban and rural collectors and the non-interstate system.
The ASCE noted that timely, preventive maintenance of the nation’s roads with better materials extends the life of pavement and costs less than reconstructing pavements after they reach failure.
The increased use of innovative materials to preserve and rebuild pavements that are better suited to today’s vehicle loading and more resilient to environmental impacts has led to longer lasting pavements and lower life cycle costs, the ASCE pointed out.
The ASCE noted that advancements in technology have created opportunities for the nation’s road networks. That includes advanced pavement monitoring where the use of moisture and temperature sensors are embedded in the pavement, which have made it possible to collect information about the condition of road pavements more quickly and with less impact on roadway users.
The advent of smart pavement is opening up the possibility for features like radio-connected sensors being embedded in a road to constantly monitor and report the pavement’s changing condition or to charge electric cars as they drive along, thus reducing the need for off-road recharging stops, the ASCE noted.
In early November, the U.S. government announced it will allocate $2 billion through the Inflation Reduction Act to fund 150 low-embodied carbon materials projects, including repaving. A list of the projects can be found here.
The announcement is designed to further the Buy Clean Initiative, which prioritizes the purchase of asphalt, concrete, glass, and steel that have lower levels of greenhouse gas emissions associated with their production, use, and disposal.
It is viewed as another step toward President Joe Biden’s federal sustainability goals, including a net zero emissions federal building portfolio by 2045 and net zero emissions procurement by 2050.
For example, the government allotted $11 million for LEC asphalt, concrete, and steel to address deteriorating infrastructure including repairing and replacing aging roads and parking areas in the Champlain Land Port of Entry in Champlain, N.Y.
Another project allocates $33 million in LEC concrete, steel, and asphalt to replace parking lot, sidewalk, roadways, bridge replacement and to install new fencing, all aimed at improving safety, drainage and accessibility at the Denver Federal Center in Lakewood, Colo.