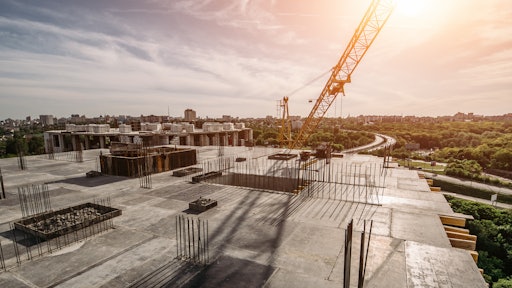
Placement of concrete in hot weather conditions can make it difficult to maintain concrete quality and desired properties. However, it is not just the temperature of the concrete that must be controlled during placement, as other factors such as ambient temperature, humidity, wind speed and exposure to sunlight also play a significant role in the hydration process of cement.
All of these factors are difficult to control in the summer months and can alter the physical setting characteristics of the concrete mixture. In fact, hot weather conditions can create a wide range of difficulties in placing and finishing fresh concrete, such as:
- Increased water demand and accelerated slump loss;
- Higher rate of setting times, resulting in finishing difficulties;
- Increased tendency for plastic and drying shrinkage cracking to occur;
- Potential difficulties in controlling entrained air characteristics; and
- Inability to reach desired strength requirements.
In addition to the hot weather concreting practices, the use of evaporation retardants will help prevent rapid evaporation and shrinkage cracking. Employing a water fog spray at the concrete placement site will keep the humidity high and the air temperature low.The Euclid Chemical Company
Although specific project requirements will vary, it is generally recommended to employ hot weather concreting practices when the concrete temperature reaches the range of 77-95⁰ F (25-35⁰ C). An 18⁰ F (10⁰ C) increase in the temperature of the ambient air where the concrete was produced and/or placed can reduce its setting time by as much as two hours. This rapid hardening can complicate the scheduling of saw-cutting and subsequent concrete placements.
Concrete temperature can be reduced during the batching process by reducing the cement and water temperature, as well as the cooling aggregates.
Mitigate the Effects of Hot Weather on Concrete Placement:
- Schedule concrete placement during cooler periods of the day, or at nighttime;
- Use a concrete consistency that will allow for rapid placement and consolidation;
- Reduce the time of concrete transport, placing and finishing;
- Use temporary moisture retaining films immediately after concrete placement;
- Use methods to limit environmental exposure, such as windscreens and sun shades;
- Cool the concrete by using chilled water and water-saturated aggregate during production.
Scheduling concrete placement and work for the cooler parts of the day can make a big difference for the warmer months.The Euclid Chemical Company
In hot-weather environments, there is an increased tendency for cracks to form due to rapid evaporation of water from the concrete. Consequently, evaporation rate is one of the most critical factors to take into consideration during hot weather concreting. The evaporation rate is the rate at which moisture is being lost from the concrete or mortar surface, which affects a few elements of a concrete or repair mortar placement.
An 18⁰ F increase can reduce its setting time by as much as two hours.
If the evaporation rate is too high, water is leaving the surface too rapidly and, in turn, creating difficulty during the finishing operations. Equally important is that a high evaporation rate during placement and initial curing greatly increases the likelihood of plastic shrinkage cracking in the concrete surface. Plastic shrinkage cracks makes a concrete surface vulnerable to the future intrusion of water and chlorides and leaves the surface with an overall unpleasant appearance.
Evaporation rate is a function of relative humidity, concrete temperature, air temperature and wind velocity at the time of placement. Below is a brief summary of how each of these properties affects the evaporation rate:
- The lower the relative humidity, the higher the evaporation rate.
- The higher the concrete temperature, the higher the evaporation rate.
- The higher the air temperature, the higher the evaporation rate.
- The higher the wind velocity, the higher the evaporation rate.
In addition, the "five point" chart from ACI 305 – “Guide to Hot Weather Concreting” can be used to help aid in calculating approximate evaporation rates.
Protect Yourself & Your Crew in the Heat: More from ForConstructionPros.com
How to Prevent Heat-related Illnesses on the Jobsite - Don't show up to the jobsite without a plan to prevent heat-related accidents. Download this guide to assist your construction team during the upcoming hot summer months.
Seven Safety Tips to Protect Construction Workers From Extreme Heat - Excessive heat and sun exposure pose significant dangers for construction workers. Western Specialty Contractors offers tips for preventing heat-related illnesses.
18 Tips to Stay Cool on the Jobsite in the Summer Heat - Getting through a hot day takes planning and preparation; don't show up to the jobsite unprepared for the heat.
Shrinkage Cracking
Plastic shrinkage cracking becomes a strong possibility during periods of rapid evaporation of water at the concrete surface. Although it is most often associated with placing concrete in hot weather conditions, plastic shrinkage cracks can also form in cold weather conditions when the temperature of the concrete is high compared with the surrounding air temperature.
Plastic shrinkage cracking is commonly associated with hot weather concreting but can occur at other times including periods of cold weather or whenever the surface concrete dries and shrinks because of rapid moisture loss.The Euclid Chemical Company
In addition to the hot weather concreting practices listed earlier, the use of evaporation retardants will help prevent rapid evaporation and shrinkage cracking. An evaporation retardant works by forming a thin, monomolecular (single molecule) film across the entire surface of the treated concrete. Evaporation retardants are hydrophobic, meaning the water within the concrete is held in place until such a time that the film evaporates, and the bleed water breaks through the surface. Thus, evaporation retardants are ideal for use in hot, dry, or windy conditions where rapid moisture loss at the concrete surface causes the concrete to crust over, become unworkable, or crack.
Employing a water fog spray at the concrete placement site will keep the humidity high and the air temperature low. Effective fogging puts a cloud of water drops in the air over the concrete. As the drops evaporate, the humidity of the air goes up, and the slab's evaporation rate goes down. Once the fog cloud settles to the concrete, it accomplishes secondary purposes of providing an artificial bleed water and cooling the concrete surface.
In order to mitigate plastic shrinkage cracking from the inside, the use of set-retarding and hydration stabilizing admixtures can help lower water demand, extend working time and maintain strength. Adding the many benefits of fiber reinforcement to the mix can also minimize cracking and reduce crack widths.
About the author
Jennifer Crisman is director of marketing services at The Euclid Chemical Company, a leading manufacturer of specialty concrete and masonry construction solutions. A 20-plus-year industry veteran, Crisman manages the marketing communications activities for Euclid’s expansive line of admixtures, fiber reinforcement, concrete repair products, flooring materials, and decorative concrete systems.