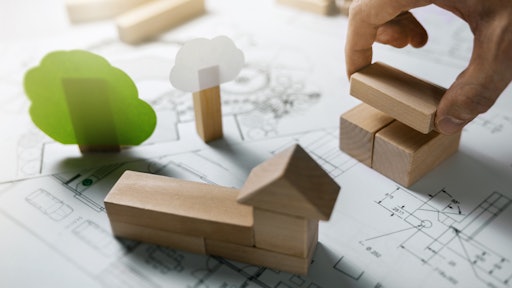
As construction waste quickly fills our landfills, it also takes away a significant portion of the bottom line. There's a lot of factors in play, of course, but most common come are inaccurate ordering, inefficient material tracking, and the simple reality of assembling a building; it happens. There's no definitive way to eliminate waste, however contractors can look at ways to minimize.
While technologies are helping contractors stay organized and help lessen over-ordering of materials, prefabricated panels are starting to find a foundation. Because prefabrication takes a lot of the design decisions to the plant, it presents an opportunity to reduce the potential of construction waste on site and increase the speed of construction.
Let’s look at two companies building awareness in the concrete panel market: Nexii Building Solutions Inc. and Vero Building Systems.
Nexii Building Solutions Inc.
Brothers Michael and Ben Dombrowsky invested 10 years of research and development into the creation of a high-performance material. They were searching for an efficient and sustainable method of building to address the waste and inefficiencies they saw during their earlier careers in construction. In 2019, Stephen Sidwell partnered with the brothers to create Nexii Building Solutions Inc. (Nexii) and became CEO the same year. The company is based in Vancouver, BC, Canada.
Nexii is a manufacturer of prefabricated panels that are made with the company’s proprietary material, Nexiite, providing what Nexii considers to be a more sustainable alternative to ordinary portland cement-based concrete. Panels can be installed by Nexii team members and Nexii-certified assemblers. (Fun fact, the name Nexii takes inspiration from “nexus” or a means of connection.)
“Our purpose and our day to day is that we're designing and we're manufacturing high performance buildings and building products,” says Dr. Zosia Brown, PhD, LEED AP BD+C, Well AP, the Vice President, Sustainability at Nexii. The panels are designed to be sustainable, cost efficient, and climate resilient.
The Courtyard by Marriott hotel in Nanaimo, BCNexii Building Solutions Inc.
Nexii designs and manufactures panels in a climate-controlled plant and says that it can get panels flat-packed, packaged, shipped, and assembled 75% faster than conventional construction with minimal waste on site. For Brown, Nexii’s panels are the first line of defense for energy efficiency in the built environment with a highly insulated, high-performing, and airtight building envelope.
Nexii panels are bolted in place on-site. Then, at the end of life for the building, they can then be disassembled and reused. This draws a straight line from construction waste reduction and embodied carbon reduction to keeping the valuable materials in use. This panel design also allows extension and reconfiguring of existing buildings.
The Nexiite mix is comprised of 50% sand, water, a non-portland cement based binder, and “a couple other additives ingredients that create a special blend,” explains Brown. The result is a panel with a high-strength concrete-like skin encapsulating an EPS insulated core. Panels weigh a fifth to a sixth of the weight of a conventional precast/tilt-up insulated enveloped equivalent.
Because of the proprietary Nexiite material, she says that contractors should be able to find a reduction in carbon as well as transportation emissions. Nexii can produce 8, 10, or 12-in. thick walls as well as roof panels - dimensions are dependent on the application, with the company’s largest panel currently 10 by 35 ft. Reinforcement is also dependent on the project application.
Omicron, an integrated development service, design, and construction firm out of Western Canada (and wholly owned subsidiary of Nexii), does the assembly installation. Omicron recently collaborated with Nexii to complete the construction of the Courtyard by Marriott hotel in Nanaimo, BC with partner PEG.
Nexii Building Solutions Inc.
The building envelope is only one part of an entire building system. Recognizing this, Nexii has connected various solutions within its Integrated Technology Partnerships program. Companies like Honeywell, Trane, and Pella all provide key components in delivering a net zero building solution. Brown explains that Nexii has recently been working with Siemens to develop an EV charging infrastructure solution that uses Nexii panels as a pedestal combined with Siemens technology to charge fleets.
The Nexii team has a clear focus on efficiency. “We've had huge success with some of our early builds,” says Brown. Nexii is currently targeting clients with projects that can use one design that can be scaled to multiple locations—specifically in the commercial and industrial sector. Yet, Nexii has aspirations to extend into more verticals, like residential and retrofitting.
“The mass timber structure is a great example of something that would pair well with a Nexii envelope,” says Brown. “You get a low carbon structure, but you can protect that from the elements with a durable product like a Nexii panel.” In fact, the company is working on its first building combining the two (mass timber with a Nexii envelope). The structure is currently in design and planned for Ontario and Nexii is scheduled to begin assembly in 2024. The construction techniques, according to a May 10 report, “will reduce embodied carbon emissions by 1,480 metric tonnes” and is targeting LEED Silver certification.
Previously, the company’s panels were also used in the construction of 10 highway rest-area buildings within New York state.
“Sustainability is really core to the product and a large part of my work is making sure that we’re waking the talk on our sustainability plans,” says Brown. And Nexii is walking the talk, with the certifications to back it up. The company’s manufacturing plant in Squamish, BC, has recently been TRUE Gold certified for zero waste by the Green Building Certification Institute – a first for the construction manufacturing industry in North America. Along with Nexii’s Squamish location, the company is considering a number of other locations across North America.
The TRUE certification required Nexii to demonstrate that it is diverting over 90% of waste from a landfill and prove less than 10% contamination across a range of categories.
With many news stories pointing at the carbon emissions of the cement and concrete industry, it’s a breath of fresh air (if you will) to see a construction company being recognized for its green efforts.
To earn TRUE Gold certification for zero waste, Nexii tracked about 20-25 different material streams to and from its plant. This tracking provides Nexii with an additional level of control over its waste and allows the team to see exactly what is happening at the end of the material’s life. “Typically, we will be either reusing or eliminating the waste at the source or finding recycling or high value end-of-life use for the material, " says Brown. While some materials still make their way to the landfill, they are few and far between—Nexii says it is able to divert over 90% of its waste from landfills.
According to Brown, the work done for Nexii’s carbon accounting and lifecycle assessment shows that the panels are designed to have approximately one-third less embodied carbon than the equivalent conventional construction materials currently used. Nexii has also recently released Health Product Declarations for its wall and roof panels, underlining the company’s commitment to material health and transparency.
Made of readily available, locally sourced materials, Nexii brought in third-party consultants to vet its products and ensure Nexiite, and the panels themselves, do not include any Living Building Challenge Red List substances. HPDs are valid for three years.
“I think it's a very versatile product,” says Brown. “It's just a question of growing at a pace that allows us to scale our solution.”
Vero Building Systems
Soon after moving to Florida, Annette Rubin found herself in the path of Hurricane Michael (2018). The forecast had the storm predicted to hit lower Alabama but – as hurricanes do – it moved closer, just east of her area. Afterward, she started searching about building codes in her county. She had many questions about what her home could survive. Do they stay, when do they evacuate, and how do they survive the next hurricane? She soon discovered that the building code was only category three for residential builds.
Hurricane Michael was a strong Category 5, meaning there would have been significant damage to her home.
Her searches changed to how to build hurricane-safe homes, materials used, how to use cinderblock, etc., and she found Emmedue through an investment opportunity. Emmedue is an Italian company founded in 1981 with 77 plants worldwide and millions of structures built to date. Three years after Hurricane Michael, Rubin co-founded Vero Building Systems in March 2021, licensing the Emmedue M2 concrete panel building system.
What’s prefabricated is the panel design, core, and reinforcement; concrete is applied on-site. “The raw materials that we use to make our panels are not new in construction,” says Rubin. They use expanded polystyrene and double galvanized steel wire. While common in prefab buildings, their system uses them in a “very unique and new way.”
Vero Building Systems
Essentially, the panels feature a polystyrene core with double galvanized steel wire mesh on the outside finished with shotcrete gunnite or plaster. “It’s concrete, green, and globally certified as a green building system and green manufacturing,” says Rubin. Without the concrete, the panels weigh 15 lbs. Maximum width is 60 in. with a length of 40 ft.
Vero Building Systems officially opened for business Spring 2023. Panels are manufactured in Kissimmee, Florida. They integrate CAD drawings into a proprietary software to start the 3D print of panels. When ready, panels are packaged and shipping to the site. Their use seems to be only limited to their design as they can be used for both exterior and interior walls but stairs, floors, landing, roof, etc.
When a contractor builds with a Vero panel, the gunnite or plaster concrete forms a monolithic structure which provides the hurricane protection Rubin had been searching for.
“If you envision your building or the ground floor of your home, you put up all your panels, you put up the floor of the stairs, and then you use a plaster gun the same way you’d finish a pool. You go around all the walls and spray your first layer about an inch thick,” explains Rubin. Because the panels and walls are attached to the slab, everything cures as a single monolithic structure. This provides the building’s load bearing as well as fire, lift, and wind resistance.
Rubin says they even shot it with a cannon and the ball hadn’t gone through. Vero Building Systems
In a way, Vero’s Emmedue M2 panels are an inverted ICF building where concrete contractors would build with blocks of compressed foam and a concrete core. For Rubin, however, the problem comes with pests. “Termites love polystyrene,” she says. “Our panels have that polystyrene inside of two inches of concrete so they can’t get to it.”
The envelope of concrete also provides fire protection. Rubin explains that the system has been fire tested for up to two hours before any structural damage occurred – both sides of the concrete need to be heated to temperature and sustained before the heat can melt the polystyrene inside.
Contractors anchor panels into the slab by inserting the rebar into a drilled holes with an epoxy. Rebar is offset every 12 inches. Wire extending from opposite ends connect panels together.
There’s another green construction aspect – contractors can significantly reduce the need of construction lumber. As both exterior and interior walls can be built with concrete, framing isn’t necessarily needed. “You don’t have to do any framing,” says Rubin. “Where you’re going to have your electrical and plumbing, you would melt half the polystyrene and insert conduit inside. [Contractors] will run the electrical/plumbing through those conduits. Shotcrete goes right on top.”
Vero Building Systems
The shotcrete and polystyrene combination provides an insulation. According to Rubin, the standard thickness can give an R-15 minimum but a 4-5 in. thickness can increase that rating to R-60+.
Contractors interested in building this way can also find training online – and find and some efficiency as well. Vero formed a partnership with concrete construction company Skip Construction out of Dallas/Fort Worth to service the southeast and to act as a main partner for installations, but they do offer free online training with videos, quizzes, and reading material. Rubin hears from her partners that the training can help the crew build a structure 40% faster. Contact the company for information.
It’s early in Vero’s history. They launched their first plant with the first panels coming off the line early May 2023. “We are super excited to be able to empower concrete professionals, as well as general contractors, to be able to build structures that they feel good about,” says Rubin.
“That you can whip out these homes in a development and feel good that if a storm hits. Those families are going to be safe. That not only are you building with materials that are good for the environment, but they're going to be good for the end consumer and for the user and for the for the guys on site. We want to empower GCs to be able to feel proud of their crews, proud of their end result, and just feel good about keeping the community safer.”