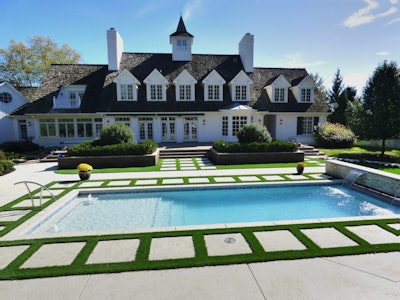
Mike Lindsey has more than once been called a workaholic. Its safe to assume many concrete contractors would likewise fall into that category.
But after almost 50 years in the business, Lindsey is not willing to take on just any project. He sets his sights on jobs that no one else can do.
“There are a lot of people that do stampings and I like to do something that no one else can do or will do. I just like the challenge of it,” he says.
In 2017, Lindsey was challenged with replicating a homeowner's vision for a white limestone pool perimeter with matching walkways.
Why Not White Cement?
Long distances and hot temperatures prevented Lindsey from using white cement to replicate the limestone look on this project. In hot weather, white cement sets up quicker and can be very difficult to work with.
“The homeowners were looking for something white, but due to the temperatures we were dealing with in the middle of summer, white cement wasn’t really an option,” Lindsey explains. Rich Grimes of Grimes Aquatech Pools and Spa
To fulfill the homeowner’s vision, Lindsey experimented with layering an ash white color harder with an ash white antiquing release.
“Even though they are the same color, there is just a hint of difference, which made a modeling in the concrete and gave it the limestone look when we texture skinned it,” Lindsey says.
Lindsey used Scofield’s Lithochrome Color Hardener in ash white, stamping with Lithotex Pavecrafters Fractured Slate Embossing Skin. This irregular-shaped, seamless tool is what creates a surface texture that looks like natural stone. He finished with Scofield’s Lithochrome Antiquing Release also in ash white, which makes separating the stamping tools from the freshly placed concrete easier.
The travel from the cement plant to the jobsite was also a significant challenge. Because the distance was so great, Lindsey’s crew added chemical reducers to the concrete to slow the setting rate. The concrete also all had to be pumped from pump trucks.
And while Lindsey did not use white cement, the concrete on this project did set a little bit slower than normal. The key, he says, is being able to control your volume. “Try not to exceed your limitations with your help,” he adds.
The Right Man for the Job
The project took about five to six weeks to complete because Lindsey and his crew had to work around the pool contractor. While Lindsey completed all the decorative work, the pool was installed by Grimes Aquatech Pools and Spa of Bloomington, Ind.
“We were assisted by the pool company, and they went out of their way to make everything right for us,” Lindsey notes.
Lindsey has been the pool company’s finisher for several years.
“The homeowner wanted to do something white and then instead of going with just white concrete, Mike came up with this white on white, and it turned out beautiful,” says Rich Grimes, president and owner of Grimes Aquatech Pools and Spa.
In fact, since then, Grimes says they’ve done several pool perimeters using the technique. Rich Grimes of Grimes Aquatech Pools and Spa
“We had done a lot of whites in the past, but it always had more greys in it. When we presented the design to the homeowner, the customer specifically wanted whiter. Mike said, ‘Well, I’ve never done this, but we could try white on white and do a sample for her.’ And that’s how it came about,” Grimes adds.
Lindsey’s willingness to try something new makes him an invaluable asset to Grimes business. Grimes initially hired him for a pool installation at Indiana University, which is where Lindsey is employed during the day.
“Since then, the reason I continue to hire him is because he's very particular about everything,” Grimes says. “We’re expected to create something special, and I'm only as good as who I hire. This something that if you don't do it every day, you're never going to be the best. He is the piece that gives us the ability to create projects that I don't have to go back and fix.”
Lindsey’s well-trained crew is another reason.
“The problem with stamping is it’s so labor intensive that you can't get a consistent job unless you have adequate people that are trained,” Grimes explains, adding that Lindsey’s crew is like a well-oiled machine. “They all know what they're doing, and they all have a position on that crew that works.”
And while Grimes does all of the structural prep work, he knows that the work of the finisher is essential.
“Everything I do doesn't show, but what he does is the most important thing. If I don't hire the person who can do that quality, then I can't produce the kind of work that we're expected to do. He’s very valuable,” Grimes adds.