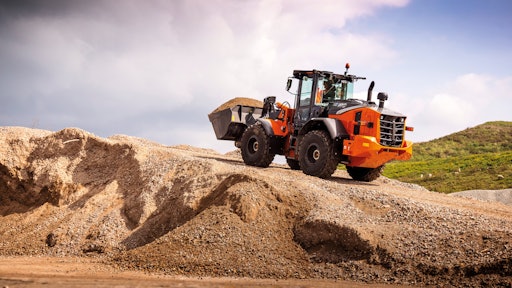
When determining which wheel loader to purchase, understanding the requirements of the job is essential. Do you need to work in tight spaces? Are you looking for a versatile tool carrier or a production loading tool? Wheel loaders come in various sizes, from compact wheel loaders under 20,000 lbs. to medium-sized loaders under 50,000 lbs. and large wheel loaders that can exceed 100,000 lbs.
Compact wheel loaders tend to be more versatile with a wide range of attachments and often offer advantages over other compact equipment choices, such as skid steers or compact track loaders. Medium-sized wheel loaders are an ideal choice when you need fast cycle times, lifting capacity and maneuverability. Large wheel loaders are true production machines.
Determining the proper size is one of the first steps in the process, and it helps maximize ROI. The size will vary according to your job requirements, such as productivity targets and the density of the material being moved. Factors to look at include the breakout force, engine horsepower, maneuverability requirements, tipping load and bucket size. If trucks are being loaded in a production environment, the wheel loader should be sized to top off a load in no more than three passes.
Once the choice has been narrowed to the ideal size, you must consider several other factors. These include the proper arm configuration, visibility, safety, productivity features, payload weighing systems and serviceability.
Arm Configurations
Standard and high-lift arm configurations are available on many wheel loader models to match the application. Standard arm configurations are popular with high-density materials due to the center of gravity of the load being located closer to the wheel loader’s front axle. This configuration also promotes maneuverability.
High lift arms are popular with lighter-density materials and when the reach is needed for placing loads in high-sided transport. Bucket sizes for these arms are often reduced due to the center of gravity of the load being further away from the machine’s front axle.
Parallel-link arms are available for wheel loader models that are often used with forks and as tool carriers. This configuration keeps attachments parallel with the ground as the loader arms move up or down. Operators have increased control while loading or unloading items. The parallel-link arm configuration also allows greater visibility when using forks or other attachments.
Comfort
Operator comfort and productivity are closely linked. Reducing fatigue allows operators to stay alert and focused for longer periods of time. There are significant differences in comfort among various wheel loader designs.
Larger cabs and ergonomic controls help reduce operator fatigue. In addition, pressurized cabs keep the operator's environment clean. Sound insulation can significantly reduce noise levels and provide a quieter working environment for the operator. Heated fully adjustable air ride seats and adjustable armrest-mounted controls are designed to comfortably accommodate operators of all sizes.
Electric-hydraulic joystick controls provide low-effort control and reduce the number of hydraulic lines in the cab.
Ride control that prevents unnecessary pitching and ensures smooth travel for the operator also leads to increased productivity.
Visibility and Safety
Choosing a wheel loader with the proper safety features can help minimize the risk of accidents and injuries. When operating a wheel loader, visibility to the surrounding work area should be a key consideration.
Cabs with panoramic visibility help create a safe and comfortable working environment. The position and design of the cab pillars and the monitor and switch panel layout are important considerations that can affect the field of view from the cab. The addition of LED lighting can also provide long-lasting illumination for safe low-light applications.
Peripheral camera systems take visibility a step further, providing an enhanced field of view of the machine’s immediate environment. Cameras can be mounted on the sides and rear of the machine to provide different views from its monitor.
Wheel loaders used in a common Y loading cycle can spend 50% of their time in reverse. The latest safety innovations address this with rear obstacle detection systems that provide visible and audible alarms. Some of these systems can intervene when the wheel loader gets close to an object.
Productivity Features
Look for productivity-enhancing features, like those that identify slopes and add power to prevent the engine speed from dropping when traveling uphill. This can reduce cycle times in lift-and-carry applications.
Some of the newest features simplify the loading process for the operator. For instance, approach speed control sets the desired speed the wheel loader will achieve as it approaches a loading point. The operator holds down the accelerator while lifting the load and the machine maintains the slower speed as it approaches the loading point. The operator taps the brake to bring the machine to a complete stop when it reaches the dump area. With approach speed control, travel speed can be adjusted with fewer pedal operations during loading. This reduces operator fatigue and fuel consumption.
In addition, auto idle shutdown and newer emissions solutions help prevent fuel waste.
In-cab monitors allow operators to adjust machine settings for enhanced efficiency. These multifunction monitors display useful information at a glance.
Payload Weight Systems
Payload-weighing systems allow you to track productivity information. Operators can check the weight of the load in the bucket from inside the cab monitor and log the material loaded.
Advanced payload weighing systems offer modes such as tip-off to truck, tip-off to pile, auto-add and manual-add that allow operators to manage loads according to the application. These systems can also warn the operator when the bucket is overloaded, improving safety during operation.
Serviceability
Airborne debris can become an issue in many wheel loader applications. This can be addressed with a hydraulically driven automatic reversing fan and wide-fin radiators. The engine air intake system should be designed to prevent dirt ingestion.
Convenient, ground-level access makes routine maintenance quick and simple.
Using telematic tools to monitor machine health also helps boost uptime. These tools can remotely monitor operational status and alert owners of upcoming maintenance needs. In some instances, the servicing dealer can now remotely diagnose issues that may arise, leading to increased uptime.
Before making a final decision, ensure parts and customer support are readily available. Check the track record of the manufacturer and its after sales support. Look for a wheel loader that’s backed by a strong dealer network trained to maximize machine uptime.
Your dealer is also an excellent resource to help find that perfect wheel loader for the task.