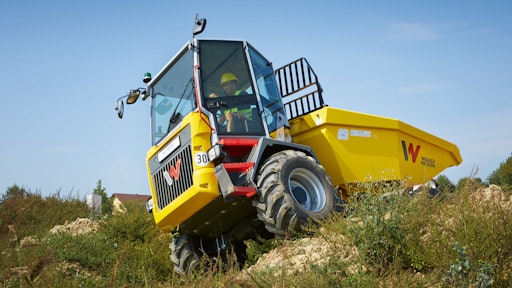
Jobsite access is perhaps the most important consideration when materials need to be moved across a construction site. Two alternatives to conventional earthmoving machines that have gained traction in North America are the site dumper and the rubber track (crawler) carrier.
Due to confined work areas, European contractors have long relied on site dumpers to efficiently move and place materials.
“Traditionally, the North American site dumper market has been behind other parts of the world, such as the UK, which is the current volume leader for these machines,” says Jay Quatro, commercial product manager, Wacker Neuson. “One market in particular we have seen growth in is the golf course industry. Utilizing turf tires, bulk material such as sand and topsoil can be hauled across the golf course at higher rates of speed than a traditional tractor or skid steer and placed precisely were needed.”
“In the UK market, every jobsite would have a site dumper almost without exception,” Peter Bigwood, general manager, Mecalac North America, agrees. “Here, we are seeing growth in certain applications for site dumpers. Concrete contractors like to use them to bring concrete into areas where they don’t want to bring a big mixer truck or a pump. We have a concrete chute accessory that we bolt on so you can precisely place your concrete and not splash everywhere.”
Another big application is the handling of landscaping materials. “For landscaping, hardscaping, golf courses, cemeteries, we put higher flotation turf tires on them so you are not tearing up the ground as you are working,” notes Bigwood.
“Site dumpers are gaining popularity in North America, especially with rental equipment companies and in specialty applications,” adds Ryan Carter, Mecalac regional sales manager.
Consider Dumper Benefits
There are many upsides to using dumpers on a jobsite. “Site dumpers are excellent for moving bulk materials,” says Quatro. “They typically have a smaller footprint and can easily maneuver in confined areas and on busy jobsites, as well as travel over rough terrain.”
They are designed for off-road applications. “The articulated pivot point provides off-road capability and excellent traction, allowing dumpers to access areas on the jobsite that other material movers simply cannot go,” says Quatro. “Additionally, they provide excellent visibility to the load when compared to a dump truck.”
The use of site dumpers can open up the potential labor pool. “A great benefit is that any operator can run the machine. It’s easy to operate with intuitive controls, and does not require a commercial driver’s license or extensive training as you would have with a dump truck or ADT,” says Carter.
The dumpers really solve a problem on cramped or sensitive jobsites. “I don’t think anyone would argue that site dumpers, which are very compact, will replace dump trucks on most large construction sites,” Carter acknowledges. “However, there are situations where access is limited or ground conditions are sensitive. That is when site dumpers, like our MDX series, really shine.”
He adds, “Site dumpers excel at precise material placement and work in confined spaces. They are compact and highly maneuverable in a range of ground conditions, while being capable of carrying payloads of up to 9 tons.”
A site dumper can be paired with other compact equipment to make an earthmoving system. “Looking at macro trends with the growth of mini-excavators, it makes sense that you would have a mini-excavator and a site dumper,” says Bigwood. “They work very well in tandem.”
Access Difficult and Sensitive Terrain
There are key attributes that enhance dumper maneuverability.
“On our site dumpers, the steering is articulated and the way we design them, the wheels are perfectly symmetrical and the same distance from the pivot post,” says Bigwood. “When you are driving through heavily rutted jobsites in the mud, the wheels follow each other in the same track.” This provides a smoother ride. “There are some site dumpers out there that are asymmetrical and that gives you a much rougher ride.”
“An articulated, oscillating chassis ensures excellent maneuverability and off-road capability,” Carter states. “When space is tight, a site dumper is a heavy-duty solution for maximum efficiency.”
Dumpers do not tear up the ground. “You can go into areas with the turf tire option, deliver the material and not tear up the ground like a skid steer would,” says Bigwood.
“The main benefit of a dumper is it’s a dedicated machine that moves material on a job. They have incredible off-road capabilities,” says Quatro. “While a dump truck is much better on a road to move material down a freeway or highway, dumpers are much better in off-road applications moving material around on a [jobsite]. They have a permanent hydrostatic four-wheel drive. It’s easy to operate for anybody.”
Dumpers are versatile, as well. “Contractors are using them to move all sorts of material, from gravel, backfill, sand, dirt, traffic signs, trash and whatever they have to move on the job,” says Quatro. “Concrete is another application that we see for dumpers. Think of them as oversize concrete buggies. You can use them to place concrete for large flatwork jobs as well as for smaller jobs.”
Different Sizes for Different Applications
There are several sizes of site dumpers available. Mecalac offers dumpers from 1 to 9 tons, with or without enclosed cabs.
“The skip on the 3-ton Mecalac machines will hold between 1.3 and 1.6 cu. yds. of liquid, depending upon the model,” says Bigwood. “Concrete would be a typical application. The 3-ton size tends to be a sweet spot for concrete contractors.”
As the name implies, this model can carry about 3 tons, though capacity depends on the material being handled. The machine itself weighs about 5,000 lbs. Its hopper (or skip) will hold approximately 2 cu. yds. of material struck evenly with the top of the hopper and approximately 2.5 cu. yds. if the material is heaped.
The 3-ton model is Mecalac’s most popular size class. “The 6- and 9-ton models you might find on a typical road construction application, in golf course construction and maintenance and many other applications where larger payloads are required,” says Bigwood.
“In the UK, where dumpers are everywhere, they will use a 9-ton when they are clearing the site and they will bring in a 6-ton when they are moving the material around,” he continues. “Then it goes down to a 3-ton when the houses start to go up. When they are doing the final landscaping, they might use a 1-ton because that will easily get between the buildings.”
Even the largest Mecalac models are relatively compact. “Weighing in at 9 tons, our largest model is approximately 15 ft. long, under 8 ft. wide and approximately 11 ft. tall,” says Carter. “Add in Power Swivel technology that features forward and swivel tipping mechanisms — allowing the load to rotate 90˚ on either side while being tipped — and you have a winning combination for working in the tightest of spaces. If there is low headroom, for example, the operator can still work with ease. The compactness of the machine also makes it easy to transport from jobsite to jobsite.”
Precisely Place Materials
Dumpers are available with both straight and swivel skip models. Contractors looking for a little extra capacity, and fewer moving parts, may want to consider a straight skip. Swivel skip models, on the other hand, can swivel the skip 90˚ in either direction to precisely place materials in confined spaces.With the swivel skips, dumpers are able to precisely place materials in confined space.Mecalac
“Most of Wacker Neuson’s site dumper models have a 180˚ swivel skip that allows the operator to place material to either side,” Quatro comments. “That is where they outperform a traditional dump truck. Backfilling trenches and working on the shoulder of a highway in a single lane of traffic are two examples of where a dumper is very efficient.”
“We’ve always had a lineup of small dumpers — 3-, 5-, 6-, 9-ton wheel dumpers — for confined space hauling for a situation where you don’t want to... or you don’t have the space to get dump trucks in and you don’t need a full-sized haul truck,” says John Dotto, product application specialist, Wacker Neuson. “If you are doing some site work that requires a good bit of material hauling and you don’t have a lot of space, a dumper makes a lot of sense.
“There is one downside when looking at conventional dumpers,” he continues, “and that is when they are fully loaded, visibility becomes a concern. New technology is available to eliminate this concern and there are some unique features that can make a dumper more productive and safer on your jobsite.”
Rotating Operator Console Adds Safety
Wacker Neuson’s Dual View (DV) range of dumpers has a feature that enables the entire operator console to swivel 180˚. This allows the operator to face either the front of the machine or turn and face the skip.
“We took the operator’s platform and made it a 180˚ swivel console,” says Dotto. “You can stare at the skip when you are working. When you are ready to haul, you pull down a lever, spin the whole console around and you have your steering wheel and your joystick, all your operational features, [spinning] with you. Now, you are traveling in a direction looking basically out the rear of the machine, which is now the front.”
With the seat and console swiveled 180˚, you are essentially looking out the windshield of a mini haul truck. “You don’t have that visibility concern of heaped material in front of you,” says Dotto. “You don’t have debris flying back in your face if you are in an open ROPS dumper. It addresses a couple of those safety concerns and inconveniences of driving in the direction of the material and just flips it around 180˚. We have [DV models] available in foldable ROPS four-post canopy and full HVAC cabs in the 6-, 9- and 10-ton size classes.”
The ability to rotate the operator platform 180˚ does add to the purchase price. “It’s going to be about a 10% to 15% premium over our standard dumper,” says Dotto. “I think that you will more than make up for it with the productivity gains that you will be able to get by being able to turn that seat around and drive in the travel position.”
Rubber Track Carriers Meet Large Challenges
For those who need to maximize material-handling capacity in poor underfoot conditions, a rubber track carrier provides a versatile solution. Rubber track carriers combine the speed and smooth ride of a tire-equipped vehicle with the traction of a steel-tracked unit.
“A crawler can be an everyday piece of equipment, but it particularly shines over soft or uneven terrain — any time material needs to cross a stream, for instance,” says Mick Heibert, KATO-CES crawler carrier product manager. “When a heavy rainfall might stop your fleet of dump trucks and therefore your site prep for multiple days, crawlers can easily continue operating. The uses are really endless.”In severely confined jobsites where turning a traditional machine around is impossible, the ability to rotate the upperstructure 360˚ and drive out in any direction is an advantage.Morooka
He adds, “New users are seeing the benefits of crawler carriers in different industries like utilities and oil & gas, and they understand how that can translate to certain applications in their line of work.
“Crawler carriers can safely reach places that a truck cannot go due to grade, elevation or ground conditions,” says Heibert. “The wider tracks of a crawler displace the weight of the equipment and its payload across a greater area, significantly reducing ground pressure ratings. When working in soft mud or otherwise unstable soil conditions that can stop a wheeled dump truck, the crawler carrier cannot be matched. Additionally, the lower ground pressure is a cost- and time-saving feature in environmentally sensitive areas, where preservation of the ground’s structure is required.”
Low ground pressure and a lower center of gravity are what really separate a crawler carrier from a dump truck. “The ability to safely move materials over rough terrain, larger grades and in poor soil conditions allows jobsites to operate more efficiently,” says Heibert. “The added safety aspect is also beneficial for everyone on site.
“To a lesser degree, the superior maneuverability of the crawler is helpful in tighter quarters,” he adds. “With zero-turning capability, a crawler can operate in smaller spaces than a traditional dump truck.”
Morooka USA has been supplying these machines since 1958 and currently offers a lineup with maximum load capacities ranging from 8,378 to over 40,000 lbs. “Crawler carriers can access jobsites that dump trucks cannot get to,” says Morooka’s David Byrd. “With the machine’s weight spread out across the large rubber tracks, ground pressure is kept to a minimum. This prevents the machine from sinking into soft ground. With more rubber on the ground, crawler carriers have an easier time navigating obstacles, as well.”
The ability to swivel the upperstructure of the crawler carrier also allows access into confined work spaces. “Morooka offers a complete line of rotating track carriers,” says Byrd. “In severely confined jobsites where turning a traditional machine around is impossible, the Morooka rotator spins 360˚ to drive out in any direction.”
The benefits of the rubber track carrier have led to continued market growth. “The growth in this segment is highlighted by the number of competitors entering the market over the past five years,” says Byrd. “A field previously offering only a few choices is now four times larger and the number of crawler carriers entering the workforce is steadily growing — roughly 10% annually.”
Congested or tight access jobsites are driving the popularity of smaller crawler carrier models. “We are finding a lot of popularity among trail builders, typically using one of our smaller models such as the KATO IC37 or IC55,” Heibert comments. “When you are working so far off the highway and literally building the trail as you go, you are often working with some incredibly tight and rough terrain. Our equipment can easily and efficiently transport materials for small hiking trails or larger trails for ATVs and side-by-sides.”