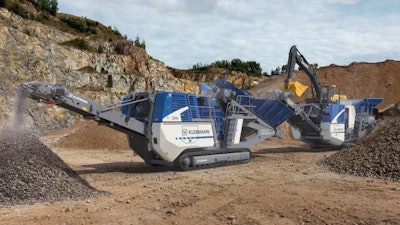
The construction industry is one of the largest recyclers in the country, recycling and reusing asphalt and concrete in massive amounts. Today's mobile crushers are ideal for use in a wide range of applications, including for asphalt and concrete or for mixed construction and demolition waste.
For larger road construction or demolition projects, on-site recycling and crushing of materials can be beneficial to the project bottom line. Processing, screening and crushing existing concrete and asphalt on-site eliminates unnecessary transportation costs and hassles. The recycled product may be used on the current project at hand, sold to another job or transported and stored for future work – saving space in landfills and saving money.
Recycling on the jobsite also mitigates the cost of buying virgin stone and it can be stockpiled to build something else on the property. Crushing concrete on site is one of the most popular forms of recycling. Other advantages of recycling concrete and asphalt right at your location include:
- Eliminating or reducing tipping fees and disposal costs
- Eliminating usage demand for much needed landfill space
- Eliminating or reducing transportation costs
- Helping preserve virgin deposits and protects the environment
- Lowering aggregate material cost for your construction project
- Lowering traffic impact and reduced energy costs
How Mobile Crushing Works
Screening and crushing plants receive the material from the initial crushing process and are small enough to be mobile. Additional crushing further reduces large particle sizes, while the screener sorts out material, allowing the right size material to pass through and returning the larger particles back to the crusher for further processing until they are small enough to be used. In order to smooth out the gradation of the crushed particle and ensure a higher quality material, the new aggregate can be fed into the crusher hopper and mixed with the recycled material.
Recycled aggregate materials offer superior compaction, better yield and greater durability over virgin (quarry or pit) aggregate bases. The use of recycled aggregates are typically authorized by State Transportation Departments for use in roadbeds and drainage projects.
To do this, contractors need specialized equipment that they either rent or own. For smaller projects, a crushing attachment or small portable crusher can be useful for turning concrete into usable aggregate.
For larger jobs, mobile crushing units are ideal. The stand-out feature of the mobile crusher or tracked impactor for recycling applications, is its mobility, combined with high productivity per hour. Units are fully self-contained on their tracked undercarriage and can easily be driven off a trailer by one operator and quickly put to work, with excellent capability for moving directly to materials. Some models are even capable of tracking (moving about on their tracks) while crushing.
Every time material is moved around or off the jobsite, labor and expenses are involved. Mobile crushers bring the machine to the job site, right to the pile and allow for efficient material processing.
Crushers: Rent vs. Own
When it comes to investing in crushing equipment, buying versus renting can offer distinct trade-offs. Buying crushing equipment usually requires a larger investment than renting; however, financing options are able to ease the acquisition. Renting can allow for a smaller initial investment; but depending on the job length and frequency of use, rental costs could add up over time.
Larger volumes of material will require a dedicated crusher, which is not only a large capital investment, but a heavy time commitment as well.
Crushers require a substantial amount of room. When you fold out a screen plant and set up a jaw crusher, the equipment is not small so you need to plan for that on project sites. You need room for the stockpiles as well.
Large crushers also require support equipment like a dozer or another excavator to feed the crusher and take away the recycled material to the stockpile.
Operating and maintenance costs also add up over time. Your crew will need to be trained on how to use the equipment and how to troubleshoot the machine in case of a breakdown. For many reasons, renting this equipment or hiring a specialized crushing subcontractor may be beneficial. If you employ well-trained team members, buying and maintaining crusher equipment may be no more costly than renting regularly serviced equipment. However, the unexpected happens, employing team members on site could resolve unexpected more quickly than waiting on service from your rental partner.
Carefully consider the economics before committing to on-site crushing. Justifying this expense requires that you have sufficient material to crush. Many say having a crusher on-site is not worth the expense unless there is 3,000 tons of material or more. Ultimately, it will come down to how much you will use the equipment and if you can keep it busy.