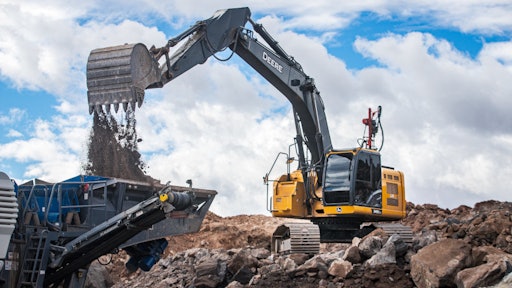
I've been spending lots of time in Utah, and among the many takeaways is the steadily increasing value of crushers to a roadbuilder's fleet. What does Utah have to do with crushers? Historically, Utah's aggregate market has been robust due to the state's growing construction and infrastructure development. The demand for aggregates, including sand, gravel, and crushed stone, has witnessed steady growth in recent years due to population growth, housing projects and infrastructure investments due to an increase in government spending.
In fact, the U.S. Department of Transportation’s Federal Highway Administration (FHWA) announced $61 billion in funding for critical road, bridge and tunnel projects as part of the historic Infrastructure Investment and Jobs Act (IIJA). All 50 states are expected to receive some of these funds to improve transportation systems. Most state and regional road-building projects include sustainable construction requirements, with some bids requiring a percentage of recycled aggregates, like Recycled Concrete Aggregates (RCA). Even without government requirements, more and more roadbuilders are interested in RCA because it can decrease input costs and help them manage their bottom line.
People eager to take advantage of government funds and roadbuilding projects will be required to use equipment or technology that improves safety and reduces the amount of carbon emissions. From my time in Utah, I’ve spoken with roadbuilders considering adding crushers to their equipment fleet. While working with team members based in Utah, I discovered crushers are versatile machines that can be crucial for sustainable roadbuilding.
Role of Crushers in Roadbuilding
Crushers, as we all know, make big rocks into little rocks. The quality of the aggregates depends on the processing, so original equipment manufacturers have developed crushers in various sizes and capacities. Smaller models, like jaw crushers, cost the same as large trucks straight from the manufacturer; while extra-large crushers can cost millions.
Crushers are separated into primary and secondary categories. As the name suggests, the following primary crushers perform the first round of compaction.
- Jaw Crusher: These large-scale, heavy-duty crushers use compressive force by feeding material into the “V-shaped” jaw. One side of the V remains stationary while the other side of the V swings against it. The material is forced from the wide opening of the V to the narrowest point, creating a crushing motion. Jaw crushers are widely used to reduce rock into non-uniformed gravel.
- Gyratory Crusher: This crusher’s hopper is lined with “V-shaped” pieces. The mantle and the concave are shaped like a cone, similar to a jaw crusher. Gyratory crushers are small, precise machines often used for crushing more extensive materials when the desired shape needs to be uniform.
Many government projects require a secondary crusher to refine the aggregate to a predictable, uniform and material. The more uniform the material, the more likely operators will be able to compact materials together consistently and pave smooth roads. The less uniform the material, the more time pavers will take to find the right force to spread the concrete or the asphalt and build a lasting road. Roadbuilders can choose from one of the following secondary crushers.
- Cone crusher: Used in large-scale industries, cone crushers apply pressure onto the material and squeeze it against a rotating mantle to create compression and force. First broken down at the top of the cone, the material falls into the cone crusher's lower, more narrow part. This process repeats until the material is small enough to drop out of the bottom opening. Cone crushers are used in asphalt pavement resurfacing or gravel pits to prepare gravel for rural roads.
- Roll Crusher: A Roll crusher reduces material by compressing it between two rotating cylinders parallel to each other. The cylinders are mounted horizontally, resting on strong springs, and the other is permanently framed. The material is then fed between the two.
Choosing a Crusher
While working in Utah, I've met many talented and experienced people building vital roads. When roadbuilders purchase a crusher, they increase their access to recyclable materials, but choosing the right one can be tricky. The right machine will depend on the roadbuilder project’s needs, use frequency, and material type the crusher will break down. Roadbuilders can make a smart investment by considering a specific crusher model’s adaptability, efficiency and reliability alongside the project’s needs. Let’s look at how those factors can help guide the selection of the right crusher. Roadbuilding projects have varying requirements, such as tight timelines, regular reporting progress, or several materials used by third-party parties. However, the project's profitability may not justify a significant investment in equipment, so a roadbuilder should consider the reliability of a specific crusher model. Roadbuilders can take advantage of opportunities in the aggregate market through a few different options of equipment or technology that can solve challenges.
Crushers will only become more popular in the next five years as sustainable building becomes more emphasized across the U.S. Consider visiting with a trusted partner to learn more about Crusher equipment or technology. To see more information about road and bridge projects, check out the Department of Transportation’s Notice of Funding Opportunities on their website.