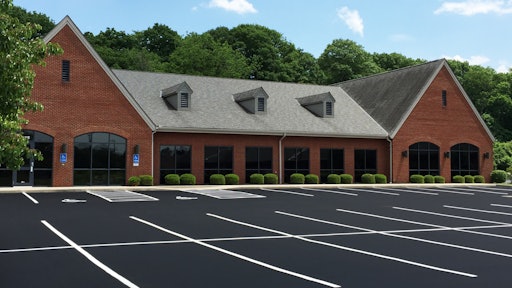
Although sealcoatings have been an indispensable part of asphalt pavement maintenance programs for the past six decades, it is imperative to recognize that sealcoatings are engineered products that must be used with a thorough understanding of their performance properties which, in turn, are accomplished through proper steps encompassing project planning, execution and management of sealcoating projects.
The Basics
A refresher in sealcoatings is always helpful prior to embarking on its more intricate aspects.
Sealcoating acts as a true “barrier coat” between asphalt surfaces and destructive elements such as ultraviolet rays, gasoline, oils, salts, fat etc. The very term "sealcoating" means keeping the redeeming properties of asphalt (such as waterproofing and flexibility) sealed in to prolong the pavement life and preserve its functional properties. After all, pavement is a sizable investment. It has been technically acknowledged that sealcoating extends the life of a sound pavement by more than 300%, at one-third the cost of pavement replacement.
In appearance sealcoatings are thick semi-fluid (like house paints) dark-chocolate brown colored, water-based coatings. They are essentially fine dispersions of binders (commonly refined tar, specialty resins, and asphalt), clays, fillers, and specialty chemicals in a medium of water. The four major components in sealcoatings are:
- Binder is the backbone of sealcoating compositions, the component that is responsible for imparting protection, preservation and beauty, while bonding tenaciously to the asphalt pavement.
- Clay and fillers impart tensile strength, hardness and abrasion resistance. It is imperative to maintain the proper balance between the toughness and flexibility of the sealcoating for its proper functioning.
- Water is the dispersion medium in which all the ingredients stay stably dispersed. It offers the ease in handling, application and storage.
- Specialty chemicals perform specific functions (such as water repellency, flexibility, specific resistance to salts and petrochemicals) while maintaining the physical stability of the sealcoating.
There are three major types of sealcoatings:
Refined Tar-based sealcoatings (RTS) are based on RT-12, a highly refined grade of coal tar, which, in turn is generated during the conversion of coal into coke for steel metallurgy. RT-12 is composed of numerous very stable chemicals that are not affected by the destructive elements of weather, the sun’s ultraviolet rays (UV), salts, gasoline, oils, fats and other petrochemicals. RTS has been the workhorse of the industry for several decades and their properties and compositions are fully delineated in many specifications.
Specialty resins, which have the performance properties of RTS, including resistance to weathering, UV, salts, gasoline, oils, fats and other petrochemicals. The technology of specialty resins is confidential to each producer.
Asphalt Emulsion-based Sealcoatings (AE) are petroleum-based and are formulated using either hot asphalt (AC) or pre-emulsified asphalt. Although the AE-based sealcoatings generally lack resistance to petrochemicals (gasoline, oils, fats, etc.), they work very well in maintaining the surface integrity of asphalt pavements and keep cracks from appearing. Over the years, the performance of AE coatings has been fortified with chemicals and specialty rubber polymers.
Now returning to the purpose of this article. It is aimed to bring all major aspects, step by step, into focus for convergence to successful sealcoating jobs.
1. Planning
The very first step is the job evaluation and competitive bidding.
Pavement Assessment:
- A thorough assessment of the general condition and age.
- Was it previously sealed or never sealed? If sealed, then what was it sealed with? It is important because major manufactures caution sealcoating over surfaces coated with Gilsonite-based products.
- Cracks -- their extent, size and depth, all of which is relevant for choosing crack fillers (cold or hot applied).
- Condition of the base and subbase. Are there any signs of water pumping through the cracks such as unexplainable water puddles or clay streaks along the cracks? If so that’s a sure indication of poor drainage. Sealcoatings are bound to fail in such areas regardless of how many times you go back and attempt to fix the problem.
- Surface contamination assessment. Check for oil and rust spots, also if the pavement is heavily wooded or tree lined, which may require treatment with a specialty primer.
- Polished aggregates, especially at entrances, exits and heavy traffic areas. These areas, too, should be primed for good bonding of the sealer to the pavement. Commonly, sealcoatings are prematurely worn off from such areas if not primed.
- Automatic Sprinkler Systems have been noted to damage the sealcoating films during the early stages of drying and cure. Automatic sprinkler systems should be turned off during the sealer application and for a minimum of 24 hours after application of the final coat of the sealer. As a practice, make sure that sprinklers are angled in a manner as not to drench the sealcoated surface. The water run-offs leave unsightly white streaks on beautifully sealcoated surfaces due to the deposition of insoluble salts, magnesium and calcium chloride that cause hardness in water.
Measurement: Online tools, which are good for a quick estimation of the area, should be supplemented with the physical inspection and accurate assessment of the pavement as described above.
Job Costing should include:
- Selection of sealcoating material
- Crack filling, patching, base or subbase replacement
- Primers for oil spot priming and specialty primer needs for wooded and tree-lined sections
- Traffic markings, signage, etc.
- Logistical management costs
- Labor and management costs
2. Sealcoating and Materials Selection
- Standard or premium grade? Would the sealer generally require the addition of performance boosters? Also include the cost of sand/aggregate and other components for recommended mix designs.
- One coat, two coats -- or additional coats per project specification? For most residential driveways only one coat is recommended if the driveway has been regularly sealed at two- or three-year intervals. You do not want to build too many coats because that could result in surface crazing (spider-webbing) issues.
- Sealcoatings should meet all applicable specifications: ASTM, Federal, FAA, GSA, commercial, special projects.
- The sealer must have a proven track record. Seek references and talk to your friends in the industry. Get comparative studies.
- Obtain certification from the supplier and the assurance that any complaints will be addressed and resolved promptly.
- Does the sealer comply with all applicable regulations? Special attention should be paid in the regions where RTS are banned. Also make sure that the sealer is compliant to recently imposed restrictions of PAH’s (polycylic aromatic hydrocarbons) levels in the sealer. Pleading ignorance is not an option.
- Is the price competitive for sealers with similar (or claimed) performance properties? Again, ask your supplier. Is sealer supplied as a concentrate or “ready to use” (RTU)? You may want to weigh both options. You may find the RTU option suitable for your operational controls, but be aware that with RTU you may have to readjust the mix design for the amount of water, additives and possibly sand/aggregate. Seek you supplier’s help.
3. Application Planning:
- The supervisor and the crew must read the Safety Data Sheet (SDS) and manufactures’ brochures/instructions on sealcoating and all the products prior to application. Safety in handling, application, clean up and discharge of the washing should be strictly followed for the safety of the workers and the environment.
- Selection of the equipment and tools for the job at hand. All should be in good working condition and spare parts should be handy for on-site repairs.
- Time management is important and can make all the difference in the bottom line profits. Plan with right size of the crew, well-delineated task order, and attempt to minimize chances for delays such as multiple runs to the factory for sealer.
- Follow good sealcoating practices with special attention to Storm Water Management Best Practices (BMP’s). Contractors should plan, minimize and mitigate to protect the environment from potential discharge and pollution possibilities. For BMPs:
o The first step should be to identify important natural resources and environmentally sensitive areas; then set protection priorities. Do not sealcoat within 100 feet of a wetland.
o Minimize environmental impacts by reducing potential run-offs/pollutant loads (not just the sealer). Block during the sealer application. Do not apply if thunderstorms are in the forecast.
o Pavement and ambient temperatures must be a minimum of 50° F. Do not apply sealer too late or too early in the season.
- Furnish the crew with all personal protection equipment. Explain and enforce other safety requirements.
4. Pavement Preparation
As with all surface coatings the pavement should be clean and free of surface contamination and defects.
- Clean the pavement by brushing and blowing. Scrape the high dirt-built areas and pressure wash if necessary. Remove all vegetation from cracks.
- Crack fill, patch and in-depth base repair.
- Prime oil spots and special problematic areas, especially under tree lines.
o Oil Spot Priming. This is an essential step, which is frequently overlooked and bypassed. It may not be a significant factor for most home driveways but must be considered for commercial applications where you see the extent of oil dripping on the parking lots of big chain stores. Sealcoatings will not bond to oil spots if they have not been properly cleaned and primed. Follow manufacturer’s recommendations. Also check if the oil drippings have soaked into the pavement over the years and damaged the asphalt. It may require patching.
o Aggregates in the pavement become polished (smooth, slick to touch) over years of use. The extent of “polishing” is directly proportional to the amount of traffic and the traffic pattern. For sealcoatings to be effective it is essential the surface have some roughness. Without priming, sealcoatings commonly wear off from the entrances, exits and the driving lanes of commercial parking lots. The remedy is to prime those areas with a thin coat of a specialty primer that is designed to penetrate into the “polished” aggregate and provide a bonding surface for the sealer.
5. Material Preparation for Sealcoating
- Follow mix design recommendations from the manufacturer and/or project engineer. Mix design simply means adding and mixing water, sand/aggregate and additives (optional) to the concentrated sealer in recommended proportions for specific job requirements. Water must be potable, sand/aggregate clean, angular within specific mesh sizes.
- Make sure that the components are thoroughly mixed in your equipment. Sealcoating machines with mechanical agitation should be kept running for the most part during the sealcoating application.
- Do not alter the mix design without the prior approval of the manufacturer and/or the project engineer. Obtain a mix design recommendation from the supplier if using a ready-to-use mix. The quantities of the commonly added components (water, sand, additives) to the sealer have a profound effect on the overall performance and longevity of the sealcoating. For example;
o Too much water will reduce the dried film thickness and result in premature failure.
o A low amount of sand may affect the surface traction and the finished surface may not have a uniform textured appearance.
o Do not use additives other than those recommended by the sealer supplier. Additives are specialty chemical blends, which are designed to work with specific sealcoatings. They may not be compatible with the sealer, if not supplied by the same manufacturer.
6. The Finer Points of Sealcoating Application:
- Apply sealcoatings according to specifications and manufacturer’s instructions for the number of coats and coverage rates. Any deviation should be pre-approved by the sealer producer.
- The drying time in between the coats and the final cure should be strictly followed.
Conclusion
In order to accomplish a successful sealcoating job, it is essential that all sealcoating phases in planning, material selection, and the final clean-up be meticulously planned with due consideration to the personnel and environmental safety. I have purposely elaborated upon some major and very important aspects, which may not be commonly available in the supplier’s literature. A job well planned and executed is very likely to be successful.