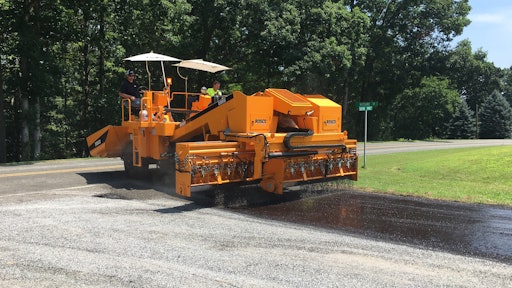
Chip seals are a popular preservation tool to help maintain roadways at a lower price point. A mile of chip seal costs about $36,000, compared to $86,000 + per mile for asphalt overlay, making it a very cost effective preservation treatment. For this reason, municipalities turn to this option to extend the life of their pavements in a quick and cost-efficient manner. The seal acts as a wearing course that helps to waterproof the surface, seal small surface cracks and improve surface friction.
Materials are put down using a tack distributor, followed by a chip spreader that disperses aggregate in an uniform manner making the process mostly seamless for both the agency and the contractor. That is of course if the equipment is properly maintained and ready to use.
"A machine that is properly maintained will perform as designed," Wayne Burgess, rapid response technician at VT LeeBoy says. "Keeping up to date on the machines normal maintenance schedule will help keep the spreader in efficient operating condition. Routine maintenance and observation will help with little to no downtime."
Machine Calibration & Daily Use
Chip spreaders are designed to put down a specified amount of material over a certain area. Aggregate coverage needs to be uniform and complete. Piles of aggregates or areas missing coverage will lead to premature failure of the treatment.
Newer machines have processor-controlled systems to get the chip application rate correct. The amount of aggregate being put down will be determined by the design specification and inspectors will be on site to make sure crews are meeting those specs.
"If you can’t apply the proper PSY (pounds square yard) to the road, it can lead to the machine being removed from the job site," Burgess says.
Making sure your machine is properly calibrated on a regular basis will help ensure you meet project goals.
"How you check the calibration is determined by the type of spreader you are operating," Burgess says. "LeeBoy/Rosco spreaders are calibrated by using a one square yard mat and spreading an application over the mat. Once achieved, the inspector will weigh all material on the one square yard mat. That weight will be the machines application. This setting then can be adjusted up or down by using the PSY application in the computers setting."
Machine calibration should be checked monthly to ensure proper application and checked with each new material you put through it.
"For every different material that you want to put through a chip spreader you should calibrate it," Brian Horner, director of sales at Etnyre International says. "You want to use the computer and to make sure the opening of the gate equals the aggregate type so that that rock is fully at your specified application rate. There are five memories on a chip spreader for each aggregate size and you calibrate the machine based on aggregate type for each job."
For machines that are mechanically driven, this includes watching your machine on the jobsite to make sure aggregates are dispersing properly.
"On SealMaster machines, contractors should watch the feedgate opening," Cody Hale, national business development manager at SealMaster says. "The first few minutes of operation will tell the best opening distance for the size of aggregate being used."
No matter what kind of chip spreader you use, the aggregate is delivered to a receiving hopper. From there, the material is conveyed to the spreading hopper. Some machines use augers, some flow gates, to move and spread the aggregate out along the spreading hopper so it will fall in a uniform veil from this final hopper onto the tacked surface. These are all wear parts that will need to be monitored on a daily, weekly and monthly basis
Belt tracking and augers should be a focus of attention for operators.
"Belts don't wear out until they rip so the biggest thing with the belts on these machines is keeping them adjusted properly each day," Horner says. "You don't want to over tighten them and you don't want them so loose that they slip when they kick on. Over tightening on the other hand will ruin the laces because there's a lacing that connects it and if you over tighten those, you'll eventually pull the lacings apart and then you will have to replace the lacings or at some point you'll have to replace the belt."
Hale adds that daily maintenance on your machine should also include properly greasing the equipment.
"Daily greasing of fittings is recommended under heavy use," he says. "Keeping the tires properly inflated and keeping the unit greased for proper wear and a long life are most important. Weekly inspections should be done to make sure no parts are out of alignment or broken. If not maintained properly, the unit could potentially unevenly disperse the aggregate. This will cause an uneven finish on the surface of the roadway."
Deep Dive During Rebuild Season
Like any other piece of equipment you own, the chip spreader features wear parts that will need to be inspected at regular intervals and replaced during rebuild season if necessary.
One of the main wear parts mentioned above is the auger that moves the material through the machine. Over time, the metal begins to wear from the aggregate passing through the auger to be dispersed on the road. Make sure to check this during rebuild season. If it is passed it's useable life, it needs to be replaced before the next season begins.
"Auger wear will be noticeable throughout the season by operators as they won't be able to travel as fast when they're spreading," Horner says. "When augers get smaller, they can't drag the rock out to the end, so operators will notice the wear on the augers because they can't deliver the material they want at a certain speed and they will need to be replaced."
Most spreaders have rubber or poly lagging that surrounds the belt and receiving hopper that is a major wear part on these machines.
"Leeboy/Rosco CSH & CSV models we have metal wear seals on each of the application hopper gates," Burgess says. "These will wear over time and can be adjusted to ½-in. of thickness until they are eventually replaced. The life of all wear items is commonly dependent upon the amount of material put through machine over time."
Another commonly overlooked item is a gate "reset" on these machines during the off-season.
"In order to maintain good calibration, every winter, somebody should go through and adjust all the wear points on the gates and adjust what we call the null and the scale," Horner says. "This is the open and the close of the gate so the machine's computer knows when that gate is fully closed and fully open. To do this, equipment owners should go through the procedure of not only mechanically setting the gates down, but then you have to tell the computer where that zero is and where that full open is.
"If this isn't done, the operator may think that the gate is at position is zero but they are actually opened a quarter inch so you're really getting more rock than what you want because we're already starting at a quarter inch open," Horner continues. "A lot of people just don't do that and it's something that should be done every year to ensure the machine knows where actual zero is."
Pay Attention & Be Alert
While routine maintenance will help keep the machine out on the job instead of in the shop unexpectedly, if your crew notices something is not right with the machine, it's their responsibility to have it checked out before it heads out to another project.
"The operator and crew should always be aware of any issues that the spreader may be experiencing," Burgess says. "If something on the spreader is not performing as designed, then it needs to be addressed by a technician."
Be sure to always refer to your manufacturer recommended maintenance schedule for guidance on your equipment.