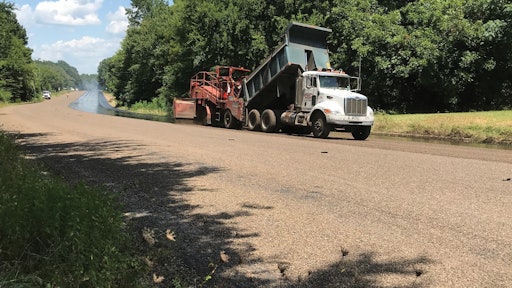
Safer roads begin with safer materials. For paving projects using asphalt chip seal, lightweight aggregate made from expanded shale, clay or slate (ESCS) has a greater bond strength and skid resistance than quarried aggregates, which enhances road safety not just when the pavement is placed but throughout the life span of the product.
Lightweight aggregate’s ability to improve road surfaces is due to its manufacturing process. The raw material is heated to 2000 degrees Fahrenheit in a rotary kiln. During this step, it softens and air bubbles form. The bubbles remain as unconnected pores when the aggregate cools. These voids inside ESCS particles allow the oil sealant to penetrate deep within the aggregate mix, resulting in fewer incidents of dislodged pavement. They also resist polishing to maintain a high level of skid resistance.
While these qualities help contractors create safer and longer lasting roads, they are not the only ways lightweight aggregate made from ESCS can create higher quality asphalt chip seal. After the material cools, it is crushed, sifted and re-crushed to create a highly regulated particle size. This not only ensures consistent coverage but also reduces the damage large chips may cause to paving equipment. In these ways, asphalt chip seal made from ESCS improves paved surfaces from the day it’s placed to the day it’s replaced. The following takes a closer look at the many ways bond strength, polish resistance and consistent chip size contribute to safer and higher quality roads.
Void is bond: increased bond strength is more than just retention
ESCS’s internal network of unconnected pores increases the bond strength between it and the oil sealant. This leads to a greater percentage of chip retention when the asphalt chip seal is first placed. In fact, Carbon County, Utah noted that initial chip retention increased from 30 percent with quarried materials to 99 percent with ESCS in a 2017 report.
Greater chip retention means fewer passes that crews must make to achieve adequate coverage, reducing labor costs and wear-and-tear on equipment. It also means vehicles kick up fewer chips during construction, reducing damage to constituent cars and potential injury to nearby crew members. The increased bond strength also resists raveling and dislodgment as the chip seal ages—even in areas that experience harsh weather.
For example, to test the durability of asphalt chip seal made with ESCS lightweight aggregate, the Utah Department of Transportation (UDOT) resurfaced 20 miles of interstate with the material. After a year, representatives from UDOT reported there were no areas where chips had been dislodged and no claims or complaints about vehicular damage. It is important to note that during this timeframe, the asphalt chip seal experienced the extreme heat of Utah summers and the weathering caused by snowplows and de-icing equipment, both of which can prematurely damage a paved surface.
Not only does the initial and long-term bond strength of asphalt chip seal create safer roads, but it also means less expenditure on maintenance and repair over the lifespan of the material, both of which translate to a higher quality road.
No skidding: lightweight aggregate resists polish
The voids within ESCS particles also create a high-friction surface for a substantially greater skid number than quarried materials. Because these voids are found throughout each particle, lightweight aggregate in asphalt chip seal resists polishing, the process through which a pavement becomes smoother over time. While quarried materials’ skid number declines drastically as vehicles pass over it, ESCS has a surface that is constantly renewed, maintaining a relatively static skid number throughout its service life. Since lightweight aggregate provides a long-term, high-friction surface, it can help increase the stopping rate of vehicles. This can contribute to fewer collisions, resulting in a lower number of roadside injuries and fatalities.
It also provides more grip to preserve safer driving conditions during heavy rains. According to the Federal Highway Administration, over 544,700 people are injured in crashes on wet pavement annually. The high-friction surface of asphalt chip seal made from ESCS can help reduce these numbers by mitigating unsafe driving conditions caused by inclement weather.
Improving safety in all conditions is a measure of paving quality. Asphalt contractors who use lightweight aggregate in their chip seal can point to skid and polish resistance as key components of assessing the ability of pavement to provide value.
Consistency, consistency, consistency: chip size and weight reduce potential for damage
Because lightweight aggregate is processed, manufacturers can highly regulate particle size—unlike quarried materials that can have chip sizes that vary widely. Since quarried materials cannot be regulated as closely, a large rock may make it into an asphalt chip seal mix and clog the machinery. This delays project completion, increases construction costs and puts crews in danger unnecessarily.
Lightweight aggregate’s consistent particle size sidelines the risk of equipment damage to create safer working conditions and reduce the time needed to complete a paving project. Further, consistent particle size helps contractors more accurately estimate material costs. It also helps reduce oil shot rates to improve road surfaces in a cost-efficient manner.
Likewise, the consistent and lightweight nature of ESCS can decrease potential for damage while increasing coverage. Because lightweight aggregate can weigh up to 75 percent less than quarried material, contractors can see more miles of coverage per ton. In addition, if a piece of pavement were dislodged, its lightness would lessen the force of its impact, causing fewer and smaller damages to vehicles in general.
The consistent particle size and reduced weight contribute to safer and more efficient construction as well as safer roads in the event of pavement damage.
Say goodbye to rocky roads
Due to its increased bond strength, high-level of skid resistance and particle size and weight, lightweight aggregate can help improve asphalt chip seal and thereby improve the safety and quality of the roads that use it. As such, this material can help departments of transportation and asphalt contractors around the country create better and more resilient roads, benefitting both the professionals that maintain them and the drivers who use them.