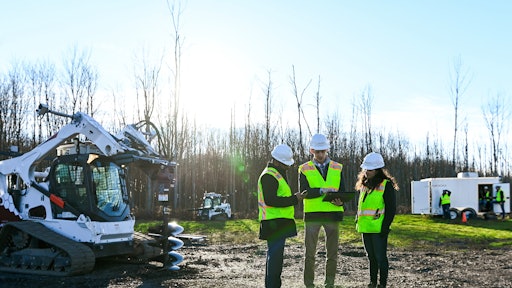
Construction equipment machine control is extending into more classes of equipment and encompassing lighter equipment. Grade control in particular is making its way beyond dedicated excavation and earthworks contractors.
A recent article on ForConstructionPros.com detailed how commercial, security, residential and other contractors have jumped onboard. Here are some things to consider to maximize return on the investment.
These choices go well beyond the decision between 2D and 3D grade control. A 2D grade control system uses physical landmarks, stakes or lasers so operators can more easily achieve grade. 3D grade controls use more advanced positioning methods, including GPS and in some cases local position systems (LPS), particularly when satellite signal is obscured by structures or landscape features.
The first of these considerations has to do with the fact that there is currently no data standard for topographic data sent to and returned from machine control technology. Contractors running mixed fleets, those who use rental equipment or contractors needing to encompass subcontractor equipment in a single digital workflow will want to pay close attention.
1. Movable vs. Hardwired
Using a single grade control system across an entire site or project is difficult if you rent machines or if you want to have a single digital workflow that cuts across subcontractors’ equipment. Relying on machine control that can be easily moved from one machine to another is one workaround. But contractors may also want to go this route if they want to avoid permanent installation or drilling holes in equipment. Some machine control tools can be installed with no tools, relying often on magnetic sensors on the boom or blade that communicate, sometimes wirelessly, with a control module that in turn automates the business end of the machine.
Many of these applications, including the Trimble Earthworks GO! 2.0 solution for compact equipment, will pair a tripod-mounted laser transmitter which communicates to removable sensors affixed to a blade. Native iOS and Android apps enable operators to use their smartphone as their primary machine interface. The application can remember individual machine profiles to ensure the grading attachment only needs to be set up once.
The iDig System, meanwhile, adds to the mix solar charging for the sensors. As is the case with other laser-controlled portable grade control solutions, iDig relies on magnetically attached sensors on the boom or blade communicate with an LED indicator in the cab.
iDig's cab-mounted touchscreen display shows the operator the machine's bucket in relation to surrounding surfaces. A light bar with red, orange and green LEDs indicates when the bucket teeth are on grade.iDig
Individual attachments, which can be moved from one machine to another, may also come with their own minimally disruptive grade control technologies.
Other aftermarket solutions, including those from Unicontrol, enable the smart components to move from one machine to the other which helps a contractor limit their investment while still using the technology across multiple machines.
“There are downsides in terms of accuracy of the sensor itself when it communicates wirelessly,” Unicontrol Managing Director for North America Rich Hilliker said. “I know a lot of those are solar powered, but they'll have their own limitations built in with that.”
While Unicontrol sensors do not move from one piece of equipment to another, the file formats travel easily into different applications, making life easier for contractors and project managers dealing with multiple grade control brands.
“We're using XML and DXF,” Hilliker said. “XML is for the surface, and DXF is for the line work, background, points and coloring. And those are the two most open common formats that any of the any of the CAD software or model building software can work with and output into. Trimble Business Center has no problem working with these.”
In some cases, contractors will want to watch for metadata that may not be included in a standard file.
“I know that sometimes there are file elements that wrap everything together,” Hilliker said. “The Topcon TP3 format for instance wraps in a localization file that's buried in there as well. For localization, we can work with anything. I've got a giant list of file types here. For Unicontrol, it's very, very, very important for us to be able to slide into an existing job site that might be using Trimble or Topcon. In order to do that, we've made our stuff work with any of these formats.”
Work is proceeding on section four of ISO/TS 15143, which will provide an industry standard for grade control topographical data, most contractors should be able to get by straddling different formats, according to Hilliker.
“A standard will be fantastic,” Hilliker said. “Because then, all of the model builders and engineers are going to work to that same standard. And then, the customers don't have to have to be confused or make sure to ask for a specific format or pay somebody to change it … There are a couple of softwares out there that can change the format, and it is just a matter of asking what the model builder actually did and getting them to output it in a different format.”
More complex projects may turn this file coordination into a time sink, though.
“I mean, I can see this getting a little messy if you have a major project with multiple subcontractors, and one of them is using that proprietary format,” Hilliker said. “It would be a little bit more work generated for the model builder, but it really it should just require hitting the output button into this standard format.”
Trimble Earthworks GO! Grade Control Platform is a 2D grade control solution for compact machine grading attachments that enables high-accuracy grading in an easy-to-use, portable platform.Trimble
2. Aftermarket vs. OEM
IRONPROS is following the evolution of machine control not only in terms of its capabilities, but the route it is following to market. The 2023 State of the Industry Construction Technology Report revealed adoption curves for both OEM and aftermarket machine control. OEM machine control was the approach used most by study respondents, with 27% using it already, 5% budgeting for OEM-based machine control and 11% planning for it at some point in the future. Only 15% of respondents, meanwhile were using aftermarket machine control, 5% had it in their technology budgets and 12% were planning to roll it out in the future.
Original equipment manufacturers (OEM) are including machine control as an option in more products and equipment classes. While this may continue, a lack of data standards and reliance on rental equipment may mean many contractors will want to opt for movable machine control technology or ensure technology their OEM equipment comes equipped with can produce and consume topographic data through open standards.
According to Moog Industrial Business Development Manager Scott Scheffler, there are arguments for and against buying equipment with factory-installed machine control. Moog currently works strictly with OEMs to provide machine control technologies.
“There is an upside to both options,” Scheffler said. “Factory integration can be easier to setup, less intrusive on the vehicle, and include a factory warranty. Aftermarket options are great as you can utilize your existing fleet and move the solution from machine to machine.”
As newer equipment comes standard with electromechanical controls rather than hydraulics, this means factory-supplied grade control can take advantage of the new capabilities these technologies offer.
“Advanced capabilities via electromechanical actuators open a new level of control,” Scheffler said. “These actuators are always aware of their position and can leverage assistance features to help operators achieve better results, faster.”
Aftermarket machine control may also benefit from electromechanical actuators, but that will limit the applicability of the technology. Unicontrol, for instance, is releasing a bulldozer product that will only work on newer equipment.
But with this caveat, according to Hilliker, aftermarket options can put contractors back in control of what equipment they purchase.
“Unicontrol can work on almost any machine,” Hilliker said. “Our indicate-only systems on bulldozers or excavators have no limitations. Nobody has the perfect fleet—you always have mixed brands on site. It is very rate to have Cat or Deere only.”
Aftermarket options like Unicontrol may also penetrate equipment classes that have not been addressed yet by OEM solutions.
“We have had a heyday with track loaders lately,” Hilliker said. “Nobody has paid attention to that market—and we are talking about the big ones like that Cat 953, Cat 963 and Cat 973.”
3. Buy or Subscribe
While Moog works with OEMs, at CONEXPO-CON/AGG 2023 it demonstrated an autonomous track loader for delivery of solar panels to solar energy generation construction sites.
The Moog CrewMate will not be sold as standard equipment, nor is the plan to sell it outright to contractors. Rather, Scheffler said Moog would follow a strategy used by a number of other automation and robotics vendors in construction—robots-as-a-service.
“The CrewMate is neither an OEM product or a standalone item for sale,” Scheffler said. “We hope contractors will use our CrewMate solution directly to support solar panel handling during installation of large-scale projects. Our near-term strategy is renting this equipment to EPCs and contractors.”
Standard grade control technologies are available either as a subscription or as rental—SITECH offers rentals of a number of Trimble technologies including:
- GCS900 Machine Control Kits
- Earthworks GO!
- Receivers MS995, MS975
- Radios SNR930, SNR934, SNR430, Satel
- Displays CB460
- 2D Laser Systems
Dealers of Leica, Topcon and other brands of machine control rentals do the same, but Trimble also offers a more formal subscription option that helps contractors stay current on technology.
“We call it Works Plus,” Trimble Sector Vice President for Civil Solutions Elwyn McLachlan said at the Trimble Dimensions 2023 user conference. “It's a way that you can get involved with machine control and construction surveying, and access our portfolio at an easy monthly subscription rate. We're seeing smaller contractors, in particular, really taking advantage of that.”
While the Trimble Works Plus Subscription may make technology more financially accessible for smaller contractors while reducing complexity, larger contractors are also attracted to subscriptions, according to McLachlan.
“What's interesting to me is we've really seen uptake from both ends of the spectrum,” McLachlan said. “We see larger contractors just recently who have got into subscriptions, particularly around big projects that they have been awarded. They may ask themselves, ‘how do I know how to align my spending to the project budget?', and using subscriptions is a way to do that.’”
Other vendors offer options that help contractors limit or eliminate an up-front capital outlay. This is true even for emerging vendors like Unicontrol.
“It is up to the individual dealer, but any Unicontrol dealer can put together leasing offerings,” Hilliker said. “Some banks have even put together Unicontrol-specific packages. This is typically a standard lease option with a buyout at the end. But it is important to the contractor to know it does not need to be a cash-up-front sale.”
4. Automated Equipment vs. Robotics
Construction robotics though are extending beyond automation of traditional digging operations by adding end effectors and attachments and robotics that extend the utility of equipment beyond what it is designed for i.e., Moog’s solar Cobot.
In part to help contractors manage perceived risk around these new use cases, many vendors are offering robots-as-a-service payment models including Built Robotics, Advanced Construction Robotics and Dusty Robotics.
These new use cases may not be on contractors’ radar screens yet but represent new opportunities for productivity and safety improvements.
“As Cobots enter the construction space, they will support workers in the field by helping them safely achieve higher productivity with fewer injuries and less fatigue,” Moog’s Scheffler said. “We’ve already demonstrated this with just-in-time solar panel delivery and lift-assistance devices.”
Examples of net new use cases include Sarcos Robotics has a line of robots that can be configured with multiple end effectors and programmed for multiple tasks including scraping, painting, ablation and other repetitive work.