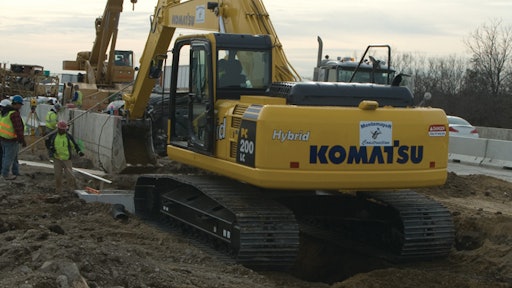
Joe Montemayor, president of Montemayor Construction, didn't waste any time before putting the Komatsu Hybrid PC200LC-8 through its paces. The morning after he took possession at an official product launch and key ceremony held at his company's office/equipment yard in Elgin, IL, the industry's first production hybrid excavator was at work excavating and removing/replacing storm sewer pipe and structures for a tollway project on I-294 in one of Chicago's northern suburbs.
Montemayor Construction is one of a select group of contractors that are being given an opportunity to conduct long-term demos of the hybrid machine to collect performance and marketing data. The units have been in production since June of 2008; are already being sold in Japan and China; and are now being launched into North America.
"We have 10 locations that we're going to take this equipment to," says Dave Grzelak, chairman and CEO, Komatsu America. "We'll basically be going to locations around the country with high emissions, such as California, New York City... The idea is to get it out and do some testing to see how it works in our particular environment."
The hybrid system
Upon initial inspection, the Hybrid PC200LC-8 looks very similar to the conventional PC200LC-8. However, the differences become apparent once you open the service compartments.
On the conventional model, the engine drives the hydraulic pump, which then powers such machine functions as upper structure swing. On the Hybrid, the upper structure is driven via the hybrid system, which consists of an electric swing motor, power generator motor, capacitor and diesel engine.
The system works by converting the kinetic energy generated during swing braking into electricity, which is sent through the inverter and captured by the Ultra Capacitor. "With the hybrid system, we've been able to harness energy that is normally lost as heat - dissipated energy in the field - and we've converted it back to electricity to power the machine," says Erik Wilde, vice president, product marketing, Komatsu America.
Unlike a battery, the Ultra Capacitor is able to store and quickly dispense the energy on demand. "A battery is basically a chemical reaction. It's a slow process to get that chemical reaction moving," Wilde points out. "We developed our capacitor to store energy and dispose of it very quickly... You get full command of power right away."
In addition to powering upper structure rotation, captured energy can assist the engine when accelerating under work load conditions.
The power generator motor is positioned between the engine and hydraulic pump to ensure effective power transmission to the hydraulics, and to charge the capacitor during periods when no work equipment or travel functions are in use. It also receives power from the capacitor for engine assist on demand from the Hybrid controller.
The benefits of the hybrid system include reduced fuel consumption and engine emissions. Based on customer trials, the technology offers 20% to 40% fuel consumption reductions (depending on the application) compared to the conventional PC200LC-8. The more the technology is utilized by swinging and regenerating energy, the greater the fuel consumption benefit.
The Hybrid also emits up to 22 lbs. less carbon dioxide (CO2) per hour of operation vs. its conventional counterpart. "We're reducing the CO2 significantly," Grzelak states. "It emits 25 tons less than a conventional machine in a year."
Getting the feel for hybrid technology
Montemayor Construction was selected as a long-term demo partner for the Hybrid model due to its experience with Komatsu equipment. Its fleet includes Komatsu excavators ranging from the PC160 to the PC300. "They were looking for a company that does high-profile work that likes the Komatsu excavator or primarily uses it," says Montemayor.
The family-owned construction firm specializes in underground construction. It does heavy-highway work for customers such as the Illinois Department of Transportation, Illinois Tollway Authority, O'Hare and Midway Airports and various Chicagoland counties and municipalities, and has recently branched out into private site development.
First impressions of the new machine proved deceiving. While the Hybrid was still in the yard, the contractor's top operator took a turn behind the controls. Initially, he wasn't very comfortable with its operation. "[The engine] takes some getting used to because it idles down. Usually, when it idles down, you think, 'I'm bogging down the machine. I'm doing something wrong.' So you let go of the controls; you ease up," Montemayor explains.
But once the operator got it out on the jobsite, it was a different story. "Typically, when you're asking more from the machine, the computer is revving the [engine] up, whereas, in this machine, it's constant. It's much smoother; it's not as abrupt. It doesn't hesitate.
"When you hear it idle down, you think you're asking too much, but you just [need to] keep going," he continues. "It's just getting used to the feel of the machine. It's a little different, that's all. Once you get past that, it behaves the same [as a conventional excavator]."
With it being just the start of the eight-month demo process, it's too soon to tell what the long-term impressions of the Hybrid may be. But the contractor has demoed other machines in the past and, according to Montemayor, you can usually tell pretty quickly if a machine isn't going to meet expectations. "You know right away," he asserts.
"[With the Hybrid PC200LC-8], they hit the mark with what you're used to getting," he states. "They did do a good job."
Specs at a Glance
Operating weight: 43,643 to 47,260 lbs.
Net engine hp: 138 hp @ 2,000 rpm
Bucket capacity: .66 to 1.57 cu. yds.
Arm digging force (SAE): 27,780 lbs.
Bucket digging force (SAE): 31,080 lbs.
Swing torque: 49,907 ft.-lbs.