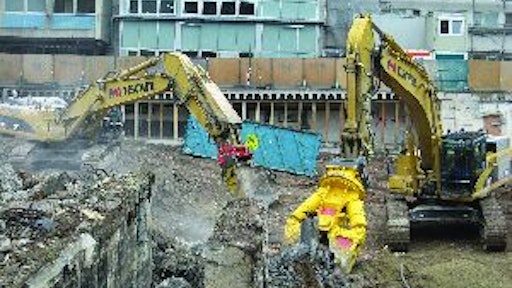
List prices for concrete crushing and shear attachments can range anywhere from roughly $25,000 to $450,000 or more, depending on attachment type and size -- in some cases, representing nearly half the cost of the carriers on which they're mounted. In order to protect this sizable investment, you need to keep such attachments in peak operating condition. A good starting point is to follow manufacturer recommendations for proper service and use.
"Keeping a concrete crusher or shear attachment clean of excessive dirt and debris, adhering to the manufacturers' recommendations for lubrication type and intervals and staying within the published guidelines of blade clearance and jaw profile will give you the maximum component life and more favorable operating performance," says Kevin Loomis, product manager - hydraulic attachments, North America, Atlas Copco Construction Equipment.
"Keeping equipment well maintained is key to performance," adds Tracy Black, operations manager, Kenco, "which directly affects profit."
DAILY INSPECTION POINTS
Daily inspection of an attachment will enable you to catch problems early, which also keeps small problems from turning into large problems. "Check for signs of wear, and keep the attachment clean, painted and greased," Black advises. "This will not only add life to your attachment, but it will also make it easier to spot problems should they occur."
According to Loomis, daily maintenance should include procedures such as lubrication of moveable components; visual inspections for cracks in the structures or damaged hoses; checking threaded fasteners to ensure they haven't loosened or are in need of replacement; and checking for proper cutter blade clearances.
For R. Baker & Son All Industrial Services, daily service and inspection are a standard part of equipment operation. This New Jersey-based demolition, dismantling and rigging contractor operates throughout the U.S. Its fleet includes two LaBounty UP50 Universal Processors and a Wagway C-4200 concrete crusher used for demolishing buildings, processing scrap and crushing and sizing concrete; as well as LaBounty MSD 1000 and MSD 7500 shears used for building demolition, cutting steel and processing scrap.
"Our operators are trained on the proper use and inspection of equipment and attachments," says Damon Kozul, PE, CHMM. "Daily basic maintenance is performed on each machine or attachment, which includes grease fittings, and making any minor adjustments or repairs. In conjunction with daily maintenance, daily inspections are conducted each day and recorded on inspection reports. Deficiencies, wear or damage are noted and sent to our mechanics to schedule repair or replacement."
Operators and/or service technicians are also required to replace pins as needed, and check bushings for tightness. "Along with daily checks, any locking mechanisms, fasteners, retaining bolts, etc., need to be checked prior to operation for the day, just from a safety standpoint, to make sure everything is connected," says Mark Rafn, senior engineer, Stanley Hydraulic Tools.
It's important to correct any problems as they arise. Even something as simple as a lost bolt could become a catastrophic failure if left unattended. "If you lost or broke a bolt and you operate without it, you could risk further damage downstream," says Rafn. "That missing $2 bolt could turn into a $10,000 repair job."
WATCH THE WEAR SURFACES
According to Loomis, weekly maintenance may include rotating cutter blades on shear attachments equipped with multiple wear surfaces, and hardfacing to build up or maintain a certain profile of the teeth or jaws on concrete crushers.
"Rebar cutters should be sharpened," adds Black, "and, along with any teeth, replaced when needed."
Visually inspect common wear items such as the teeth and cutter blades to identify worn edges, chips or reduced overall profile. "Cutter blades will also commonly have a clearance specification that is measured with a feeler gauge to determine the need for additional shimming or replacement," says Loomis.
"We find that the knives of the shear or cutting area of the concrete pulverizer attachment are most subject to wear and damage. Pins and bushings are also subject to ancillary wear and damage," says Kozul. "When the attachments become worn and damaged, production is noticeably affected. The shears do not cut as well, and the scrap metal we are cutting can get bound in the shears. On concrete pulverizer attachments, materials can also get jammed or bound in the teeth."
Most crushing attachments are designed so that cutting edges can be removed, replaced and taken back to the shop to be "rebuilt" via hardfacing. This can significantly extend their working life.
Rob Murray, product line manager, Stanley Hydraulic Tools, cites a contractor in Minnesota that alternates two sets of cutting edges between three concrete pulverizers. "They don't let the [edges] wear down so far that they have to apply a lot of heat on them to build them back up. And they're able to get four or five years out of two sets," he states.
"The problem comes when... you let them get worn down so far that you have to apply too much heat to them," he explains. "Pretty soon they become brittle and they will break."
A replacement cutting edge kit for a concrete pulverizer may run anywhere from $2,000 to $4,500, depending on the size of the attachment, he notes. Compare that to the cost of a four-hour rebuild plus materials, and the cost difference is substantial.
To eliminate any guesswork, Stanley LaBounty provides a template for its Swift-Lock cutting edges. "A customer can hold the template against the tooth and verify if it is worn down to the point where it needs to be maintained or not," says Murray. The template makes rebuilds easier, as well. "[The welder] is able to use that template to build it back up to original specifications."
Shear blades, on the other hand, aren't designed for rebuilding. "They're made of a special hardened alloy material that is not conducive to being welded on," says Murray. Instead, they are indexable -- in other words, they can be rotated to extend wear life. "If the wear has created a radius on the cutting edge of the blade to a certain specified dimension, it needs to be rotated. When all four sides or segments are used, it's disposed of."
"We watch for the shape of the blades, and look for clearances," notes Kozul. "For a shear to cut correctly, there are specified tolerances between the knives. Once production slows or steel materials start to bind, we try to repair or replace the blades as necessary."
ADDED COSTS OF NEGLECT
It's not uncommon for operators to cut thinner materials when shear blades are sharp, then move into heavier steel or concrete processing as they start to dull. However, there is a risk in letting the blades wear too far.
"If you neglect maintenance and let it wear to an extreme, you could be putting on additional loads that are detrimental to the structure," Rafn points out. "What happens is a tooth will get worn so thin that it will break off and you won't notice it's missing. Then you start wearing into the receiver, and you're in trouble."
On concrete crushing attachments, the factory-machined cast receiver is weld-in replaceable, but at a price roughly equivalent to the cutting edge kit. "It requires a little more effort, but it's not catastrophic," says Rafn. "In the shears, it's a little more problematic because now you're down into some structural material. Yes, it can be remanufactured, but at quite a cost."
The costs of neglect can quickly mount up over time, eating away at your ROI. "You could build a case around doing maintenance [based on] 'this is what it's going to cost' and 'this is what it's going to save.' But if you don't do it" Murray states, "you are going to end up compromising your return on investment schedule."