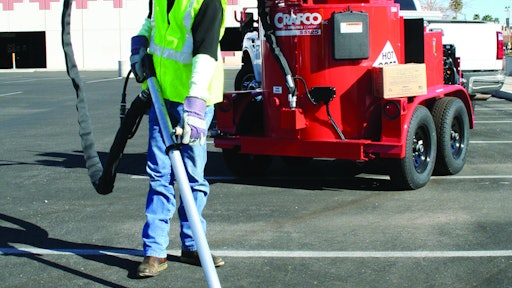
For contractors looking to offer additional services, the available options can be intimidating. Whether you are a striping contractor or a sealcoating contractor, it may be tough to choose what service is an affordable startup and with a great market potential. Cracksealing is one option available to contractors searching for another valuable service to offer their existing clients.
By offering cracksealing services, contractors can help their existing clients extend pavement life. With limited equipment, it can also be a relatively low-cost venture contractors can pursue for added revenue.
Why Cracksealing Protects Pavement
There are several reasons why cracksealing is essential in maintaining the quality of a pavement. Sealing cracks with the appropriate material will help preserve the base and subgrade. "By sealing the cracks and keeping out moisture, you will prevent potholes and subgrade issues," says Jason Stepp, national sales manager for Stepp Manufacturing. "Cracksealing is about keeping the water and moisture out of the subgrade and from underneath the pavement. Water, snow, ice and rain accumulate inside the crack. The moisture in there freezes and then the water thaws, but the frozen ground can't absorb the water. At night, this water freezes creating potholes."
Cold weather isn't the only detrimental season to cracked pavement. Subgrade issues can also arise during warm months. "In summer, water washes out the subgrade underneath the pavement," Stepp says. "Now the pavement has nothing to support it, and you get recessed cracking. When the traffic rides over this surface it opens the potholes."
According to Tom Pfuelb, eastern regional sales manager of Crafco, Inc., cracksealing is the most effective maintenance service. "Cracksealing is one of the most effective preventative maintenance operations anyone can perform on their pavement to extend its life," he says.
Equipment That Gets the Job Done
Before purchasing cracksealing equipment, contractors must have several key points set. First, they must know the type of work they want to complete — driveways or parking lots. Next, before purchasing equipment they must have a budget set based on the type of work they will complete. "Contractors must look at the cost of a unit, what they are getting, and the safety features of the equipment," says Cliff Cameron, director of sales at KM International.
Purchasing the appropriate size of equipment is essential for contractors to find success. Contractors want to avoid purchasing a unit that is too small or too big for their services. "If someone is just starting out I tend to put them in a little bigger kettle than they may need right now," Stepp says. "Cracksealing is one of those services that when you start doing it, it is a big growth area for business."
The startup times and recovery times is also essential when purchasing equipment. "We are able to get hotter quicker and recover faster," says Craig Walter, sales manager at SealMaster. "Nothing costs you more than standing on the side of a road or on a big parking lot waiting to melt material down."
Contractors will also have to choose between a diesel engine and a propane powered unit. Stepp suggests that propane may be a better option for the contractors who complete a few projects a year while a diesel engine would be more efficient to the contractor using the equipment frequently.
Another feature contractors will choose from is an oil jacketed kettle and direct fire units. With an oil jacketed kettle, contractors will have a tank filled with oil and the oil heats the product through indirect heat. Stepp Manufacturing makes several oil jacketed units. "You have constant agitation and a smooth, even heating system. You also need to have some type of temperature monitoring controls so you don't over or under heat the material," Stepp says.
KM International manufacturers an “Air Jacketed” fully self contained 55 gallon unit. The unit has a pipe burner system that is thermostatically controlled. It is much like an oil jacketed unit without the oil and works on convection/conduction principals controlled thermostatically.
Crafco manufactures a direct fire unit. Direct fire units, unlike oil jacketed kettles, have the flames directly heating the material. With direct fire units, contractors will have a basic kettle, torch and hole for placing the materials.
Cracksealing Starts with a Clean Crack
In order to provide customers with the best end product it is essential to complete the proper prep work. With cracksealing, contractors must always clean the cracks. "Moisture is one of the biggest evils for cracks," Cameron says. "Once we dry out the cracks the rubber will bond well. With the Crack Jet II or a heat lance you can go out there and efficiently dry the crack."
Pfuelb agrees to the importance of proper crack prep. "The most important thing to have in mind is a clean, dry crack and hot sealant," Pfuelb says. "A clean and dry crack is critical to the performance of the sealant. Dirt or moisture will compromise the bond of your sealant. If you are applying crack sealant to a crack that is dirty or wet it greatly increases the chance of the sealant failing."
To guarantee proper cleaning of the cracks, contractors can use compressed air to blow the crack clean and dry; a heat lance that uses compressed hot air to remove debris and clean cracks; or a crack router, which follows the existing crack, carving a niche or reservoir to contain the cracksealing material. Research has shown that using a router, such as Crafco’s Model 25 or Model 200, to prepare cracks for sealing results in repairs lasting 50% longer than cracks sealed without a router. However, routing takes additional time and is more costly to the end user, and Stepp warns that if the equipment isn't used properly it can be detrimental to the pavement. Still another option is KM International’s Crack Jet II. "The Crack Jet II heats the crack, dries the crack and etches the walls of the crack so you get maximum rubber adhesion giving you a better quality repair," Cameron says.
As for bidding, contractors have two available options to complete the job. One option is to measure by area. "I'm going to go onsite, drive around, and look for a heavier cracked area and lighter cracked areas," Walter says. "I'm going to find something on a heavier cracked area and measure off a 1,000 square foot in that particular pad and do two or three other pads in the area. I'm going to pull all the cracks in that particular 100 by 100 foot square. I will add them all up, multiply by the space, and divide it by 5. One pound of material will fill 5 feet of crack and that will tell me how many pounds of material I will need."
The second option is to measure each individual crack. "You specifically measure each crack, and you let the customer know the exact linear footage of the cracks to be filled," Cameron says. "As a contractor, you need to know how deep and wide the cracks are, how much material you are consuming during the process, and know what your bottom line is for you to be profitable."
Safety is always a concern when operating equipment. "You should wear hard shoes and long pants, and if you are operating the machine you should have safety glasses on," Walters says."You should wear something in case material splashes up at you, and you definitely need to wear bright colors. If you are in a parking lot you need to mark off areas."
Success Through Material Selection
Another area of cracksealing that will ensure a successful application is the quality of materials used. "Contractors will find a local producer of a good, quality product," Cameron says. "They need to make sure the rubber they buy is for their temperate zone and of the right quality for the job they are doing. They also need to get a product that will withstand the type of traffic that is using it."
Contractors must also be aware of the material need for their specific unit. "The direct fire materials are designed to be used in a kettle or melter that has the flame directly on the kettle resulting in a higher temperature," Pfuelb says. "Oil jacketed materials can't withstand such a high temperature."
Other materials used during cracksealing are blotting materials. These materials help avoid track marks from vehicles that can drive over the surface before the material is set. "Protection of the sealant until the pavement can be opened is critical because you will get tracking of the sealant or ticking, which is car tires grabbing on to the sealant and ripping it off of the pavement before the material is cold," Pfuelb says.
Several materials are available that contractors can use to protect the sealant including sand and boiler slag (marketed as Black Beauty). "We have the Sand Liner, a canister that will take Black Beauty and drop it right down on top of the crack," Walter says. "The best part is if you are going to sealcoat that particular day you can hot pour crack fill and sealcoat within the hour."
Another available product is Crafco's Detack. "Detack is a biodegradable liquid that can be applied with a garden sprayer," Pfuelb says. "That will be a bond breaker to prevent material from tracking."
Avoiding Common Cracksealing Mistakes
When starting off, contractors may make a few mistakes as they learn how to properly complete cracksealing. Improper cleaning of cracks is one mistake that can create problems with cracksealing. "One of the biggest mistakes a contractor can make is not assuring the pavement is clean and dry," Pfuelb says. "That is critically important to the success of the material. I've seen people just go out there with a hand broom and backpack blower, blowing the pavement clean and thinking that is adequate."
Contractors must also be aware of the required temperature for their material so they do not overheat it. "The sealants are made to have a specific application temperature range," Pfuelb says. "If you overheat the material, you damage the components of the sealant which will affect the performance of the material."
Another note for contractors is the pavement condition. "Not all pavements are good candidates for cracksealing," Pfuelb says. "Where ever there is a crack that is an opportunity for water to infiltrate the pavement and cause additional damage to it. A pavement can become so badly damaged it is beyond the scope of cracksealing." Pavements with spider cracking and alligator cracking are often unable to be repaired using cracksealing.
When look at purchasing cracksealing equipment, contractors need to first decide how cracksealing will supplement their existing business and then purchase the correct equipment: too small will frustrate them and too big may never pay for itself. Cameron says, "The bottom line is people need to look and think outside of the box. Contractors need to look at the long term profitability of their business."
SIDEBAR
Melter Applicators in the Industry
There are several available units from manufacturers ranging in size, type and application use. KM International manufactures the KM55 rubber melting kettle with a fully self-contained thermostatically controlled melting kettle. The KM55 has a 55 gallon kettle and can complete 10,000 lineal feet per day.
Contractors can also choose among several units at SealMaster. The most popular is the 260 allows contractors to run all day long, doesn't require crews to feed it constantly, and it has an 85 cfm air compressor. The unit also has a 50-foot hose reel to blow out the cracks. It can be mated with the heatlance.
Crafco manufactures units ranging from 10 to 30 gallons all the way up to a 400 gallon unit. One available unit from Crafco is the Mini Melter. It is a hand agitated, direct fire unit that has a 10 gallon melter/applicator.
Stepp manufactures the Stepp OJK unit with a 75- and 125-gallon capacity. The unit can be run on propane or diesel heat, and it is available with an overhead boom that prevents hose damage while reducing operator fatigue.
Cimline manufacturer's melter/applicators for cracksealing. The Magma Series has four available units including the 60 gravity melter, 110 gallon, 230 gallon and 410 gallon units. Operators have the flexibility to operate automatically or manually depending on the sealant and climate conditions. The hydraulic manifold provides consistent pressure in forward and reverse to alligator and material pump.
The KERA 145HD rubberized crackfilling kettle from Marathon Equipment , Inc. features a heated hose and wand delivery system. The unit has a built-in overnight heater with a 145-, 260- and 400-gallon capacity. An optional 80 dfm air compressor is available with the unit.
SIDEBAR
Contractors not wanting to invest in a cracksealing melter/applicator or who don’t repair large amounts of cracks often choose to seal cracks with a cold pour crack repair material, which testing has shown can be expected to last one to two years. Testing has found that cold pour material, which has a safety advantage because it doesn’t require heating, is generally most effective on cracks 3/16 inch wide or less.
According to the National Center for Transportation Research (NCTR), cold pour materials “can be applied during times of high humidity or when cracks are moist or damp,” though such conditions do require extended curing times. NCTR research has demonstrated that the ideal conditions for cold pour sealant application are when the air temperature is above 40 F and rising. Cold pour sealant should not be applied if the air temperature is below 50 F and falling.
“Due to the low viscosity of cold pour sealant, the material will penetrate into the crack easily without any need for routing procedures,” NCTR reports. “It is critical that the vertical surface of the crack be clean to insure that the cold pour will adhere to the crack.”
Allstates Coating Company manufactures the Super Flex Cracksealer, a single-component, cold pour rubberized crack sealant. It is quick curing and durable in all climates with a non-tracking formulation.
The LASTEK CP-3405 Crack Sealant from Maintenance Inc. is a elastomeric, cold applied for asphalt. The material remains flexible below -20 degrees F. It can be used to fill cracks up to 1.25 inches wide.
Star Inc. manufactures the Star Sta-Flex, a rubberized cold pour crack filler. No heating is required before application, and it is a tough, flexible and durable material.
The Brewer Company manufactures Brewer Tough Stuff, a cold pour, flexible rubberized asphalt emulsion crackfiller. With excellent flow properties, it is a ready-to-use formulation for asphalt surfaces.
Unique Paving Materials Corp. manufactures Kold Flo Pourable Crackfiller. The material is modified asphalt emulsion crack filler that can be used on asphalt. It is fast curing and drivable within 30 minutes. It is available in drums, buckets and bottles.